Gravure Printing: An In-Depth Exploration of Techniques
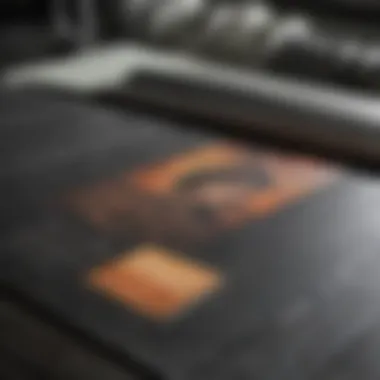
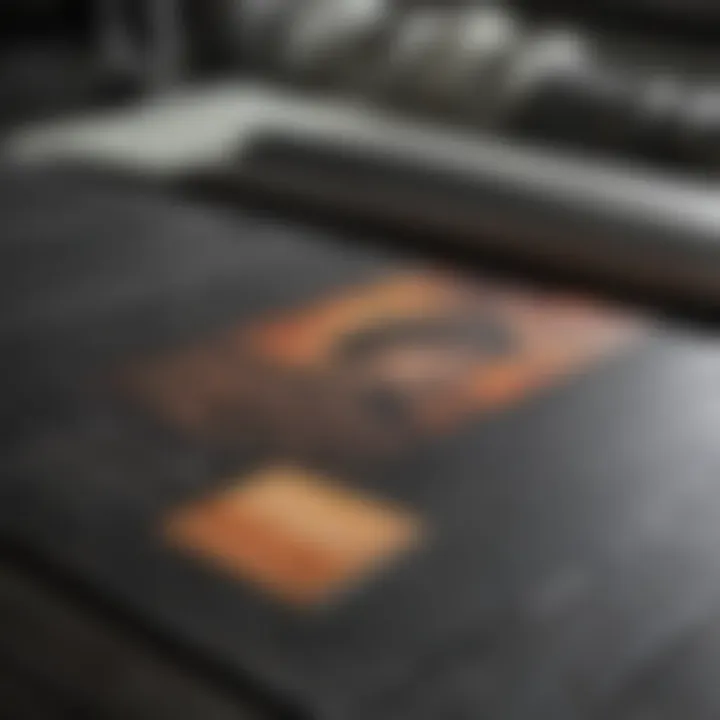
Intro
Gravure printing is an intricate and advanced method of intaglio printing. This technique has become essential in various fields, particularly in packaging and publishing. Understanding its mechanism and applications can provide valuable insights for students, researchers, educators, and professionals interested in printing technologies.
The history of gravure printing reveals its evolution from traditional processes to the sophisticated systems used today. It is worth noting the significant impact of technological advancements on the efficiency and quality of this printing method. These enhancements not only improve production rates but also address various sustainability challenges. In today's context, gravure printing remains relevant and adaptable to market demands.
Through this article, we aim to unravel the complexities of gravure printing. We will explore its operational mechanics, the materials involved, and its applications across diverse industries. A detailed discussion will also be provided regarding the advantages and drawbacks of gravure printing. This exploration will serve to underscore its importance in modern print production.
Preamble to Gravure Printing
Gravure printing stands as a prominent technigue in the realm of printing, known for its capacity to produce high-quality prints at a remarkable speed. This method employs an intaglio process, which distinguishes it from other printing techniques like offset or digital printing. The significance of gravure lies in its versatility and efficiency, making it an integral process for numerous industries, especially in packaging and publishing. Understanding gravure printing provides valuable insights into its functionality, advantages, and applications.
Definition and Overview
Gravure printing, at its core, is a method that uses engraved cylinders to transfer ink to a substrate. It's characterized by its ability to deliver consistent, sharp images and fine details. The technique operates on principles of both surface tension and capillary action, allowing the ink to fill engraved cells on the cylinder and then transfer to the substrate as it passes through the press. Gravure is often favored for large print runs due to its speed and efficiency.
The ink used in gravure is generally fluid and can contain a variety of pigments and additives. This enhances color vibrancy and durability, making it particularly suitable for products that require resistance to wear and fading. Gravure printing is commonly used for flexible packaging, magazines, labels, and even decorative wallpapers. Its capacity to reproduce intricate designs and vivid colors makes it a valuable tool in the printing industry.
Historical Context
The history of gravure printing dates back to the 19th century. Its roots can be traced to the invention of the rotogravure process by Karel Klíč in 1890. Initially, it was used for limited print runs. However, technological advancements in the 20th century paved the way for mass production. This led to its adoption in various fields, notably in packaging and publications.
The evolution of gravure printing reflects broader changes in technology and market demands. In the 1950s and 1960s, the technique gained substantial traction, driven by the growth of consumer goods and the need for high-quality packaging. Today, gravure remains a pivotal element in the printing industry, adapting to new technologies such as digital gravure, which further enhances its capabilities.
Gravure printing has transitioned from a niche technique to a mainstream method due to its efficiency and quality. This ongoing evolution ensures its relevance, as it adapts to modern printing demands and sustainability initiatives.
Mechanics of Gravure Printing
The mechanics of gravure printing are essential to understanding this sophisticated printing method. This section explores the fundamental components of gravure printing, emphasizing their roles, advantages, and potential challenges. The operational mechanics involve various elements including the design of the print cylinder, the ink transfer process, and the drying techniques utilized. Each of these components contributes significantly to the overall effectiveness and efficiency of gravure printing.
Print Cylinder Design
The print cylinder is at the heart of the gravure printing process. It is designed to hold a pattern of tiny cells that carry the ink. Each cell transfers a specific amount of ink to the substrate during printing. The depth, size, and arrangement of these cells influence print quality and ink transfer efficiency.
When designing a cylinder, considerations include:
- Cell Depth: Deeper cells can hold more ink, allowing for richer color but may also lead to oversaturation.
- Cell Arrangement: The pattern can affect ink distribution and drying time. A well-designed pattern can achieve uniformity across the print.
- Material Choices: Common materials for cylinders include steel and copper, each providing different durability and performance characteristics.
The precision in cylinder design directly impacts the quality of output, making it a crucial concern for printers. A well-crafted cylinder ensures more consistent printing results, which is vital for meeting client expectations.
Ink Transfer Process
Ink transfer in gravure printing is a unique process, dependent heavily on the cylinder's design and the viscosity of the ink. The ink is delivered from an ink fountain onto the surface of the cylinder, filling the engraved cells. Once filled, a doctor blade removes excess ink, leaving only the ink in the cells.
Some key aspects of the ink transfer process include:
- Ink Viscosity: Thick inks can enhance color density but may require specific adjustments in the printing speed and temperature.
- Doctor Blade Function: This blade plays a crucial role in ensuring that only the necessary amount of ink is retained in the engraved areas of the cylinder.
- Substrate Considerations: The type of substrate influences how ink adheres and dries. Different substrates may require different ink formulations to achieve optimal results.
The effectiveness of this process contributes to the overall success of the print job and highlights the precision required in gravure printing.
Drying Techniques
Once the ink is applied to the substrate through the cylinder, drying comes into play. This step is vital to ensure that the ink sets correctly without smudging or blending colors. Several drying techniques can be employed in gravure printing, with the most common being:
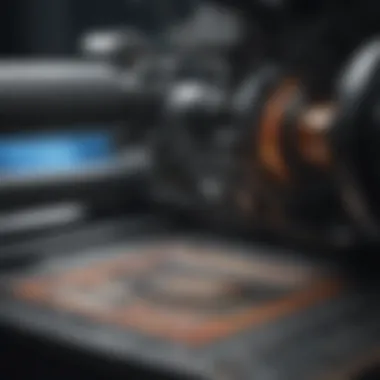
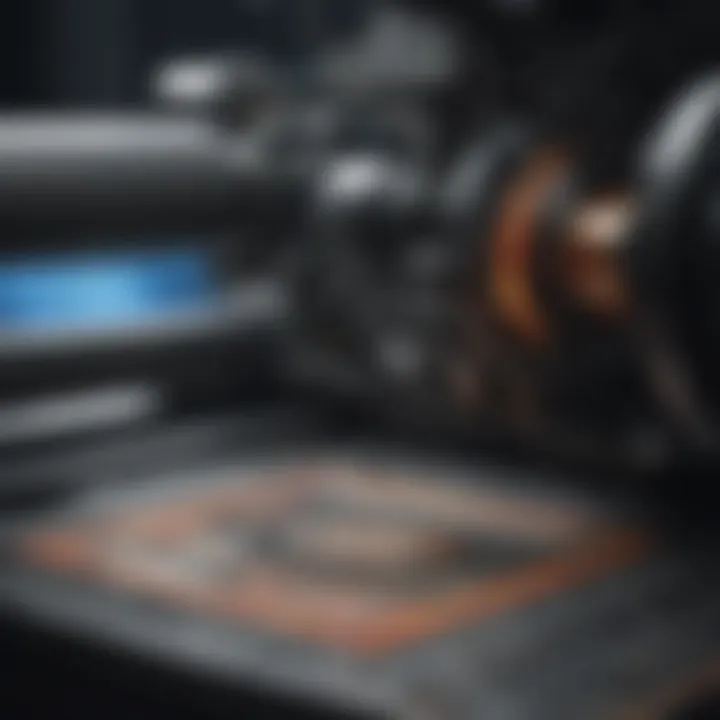
- Infrared Drying: Uses infrared light to heat and evaporate solvents from the ink. This is a popular and effective method.
- Hot Air Drying: Circulated hot air can be used to accelerate drying times, a necessity in high-speed printing environments.
- UV Drying: Utilizes ultraviolet light to cure the ink, making it suitable for certain types of inks that require rapid setting.
Each of these techniques has its benefits and drawbacks. The choice depends on the specific application and desired print quality. Faster drying times can lead to increased productivity but may affect the final outcome in terms of color vibrancy.
"The mechanics of gravure printing not only define its operational efficiency but also its print quality. Each step from cylinder design to ink transfer and drying plays a significant role in overall production success."
Understanding these mechanics is critical for anyone involved in gravure printing, as they directly correlate with the quality of the final product.
Materials in Gravure Printing
In gravure printing, the selection of materials significantly impacts the quality and efficiency of the printing process. The two key components to understand in this context are inks and substrates. Each plays a pivotal role in ensuring that the printed material achieves the desired visual appeal and durability, which are vital in numerous applications ranging from packaging to decorative prints.
Types of Inks Used
Gravure printing utilizes a variety of inks that are formulated specifically for the intaglio process. These inks are usually solvent-based, water-based, or sometimes a combination of both. Solvent-based inks are favored for their quick-drying properties and vibrancy. They provide strong adhesion to various substrates, which is crucial for maintaining print integrity over time.
On the other hand, water-based inks are gaining popularity due to their environmentally friendly characteristics. They generate fewer volatile organic compounds (VOCs), enhancing workplace safety and aligning better with sustainability practices.
Some types of inks commonly used in gravure printing include:
- Polyamide inks: Known for their excellent adhesion and resistance to heat.
- Nitrocellulose inks: These offer good color saturation and can dry quickly, making them suitable for high-speed production environments.
- Varnishes and lacquers: Often applied on top of printed substrates to provide an additional layer of protection and gloss.
The choice of ink depends on the specific requirements of the printing task, such as the surface finish, drying time, and intended use of the product.
Substrates and Their Properties
The substrate acts as the foundation upon which inks are applied during gravure printing. Substrates can vary widely and include paper, plastics, and metallic films. Each substrate comes with its own set of properties that can influence printing performance.
- Paper: Widely used for publications and packaging. Its weight, texture, and finish can significantly alter the final output. Higher-quality papers tend to absorb inks better, leading to sharper prints.
- Flexible Films: Common in food packaging, these substrates offer excellent barrier properties against moisture and gases. Their flexibility allows for creative packaging solutions, but they also require specialized inks for adhesion.
- Metallic Foils: Typically used for premium packaging and decorative prints. They create an eye-catching shine but demand more precise ink formulations to maintain adhesion and prevent smudging.
"The materials used in gravure printing not only define the visual aspects of the final product but also determine its practical applications in various industries."
Understanding these materials can provide significant insights for students and professionals alike, advancing their knowledge of gravure printing’s intricacies.
Applications of Gravure Printing
Gravure printing finds its place across various industries and settings, showcasing its flexibility and reliability. Understanding its applications is crucial for grasping how this printing method influences our daily lives. The significance of gravure printing lies in its efficiency and high-quality output, making it ideal for large-scale production across multiple sectors, particularly in packaging, publishing, and decorative printing. Each application reveals different benefits and considerations that highlight why gravure is a preferred choice for many companies.
Packaging Industry
The packaging industry is where gravure printing truly excels. Its ability to produce vibrant, eye-catching designs helps products stand out on store shelves. The process accommodates a wide range of substrates, including films, paper, and foil. This versatility is a major advantage for packaging manufacturers. Gravure also supports long runs, which is essential for brands looking to maintain consistency and quality across numerous packages.
Key advantages in packaging include:
- Color Fidelity: Gravure prints reproduce colors accurately, ensuring brand colors remain true throughout the production.
- Cohesion and Flexibility: The inks adhere well to different substrates, providing durability and a polished finish.
- Cost Efficiency: Although setup costs are high, the ability to produce large quantities quickly reduces the price per unit, benefitting mass production.
"Gravure printing is vital in creating packaging materials that cater not only to aesthetics but also functionality and sustainability."
Publishing and Print Media
In the realm of publishing, gravure printing plays a pivotal role in producing high-quality magazines, catalogs, and books. The method allows for continuous rolls of paper to be printed, which can save time in large publications. Moreover, gravure is capable of intricate imagery and fine details, making it well-suited for art-focused projects. Here, the longevity of prints is significant, as gravure results in less fading over time, supporting enduring collections.
Advantages in publishing and print media include:
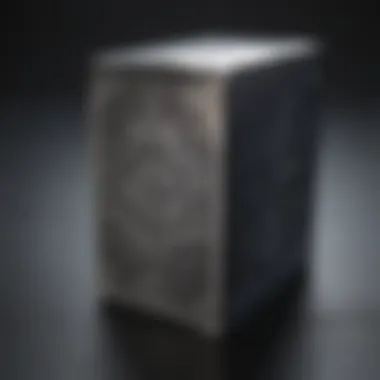
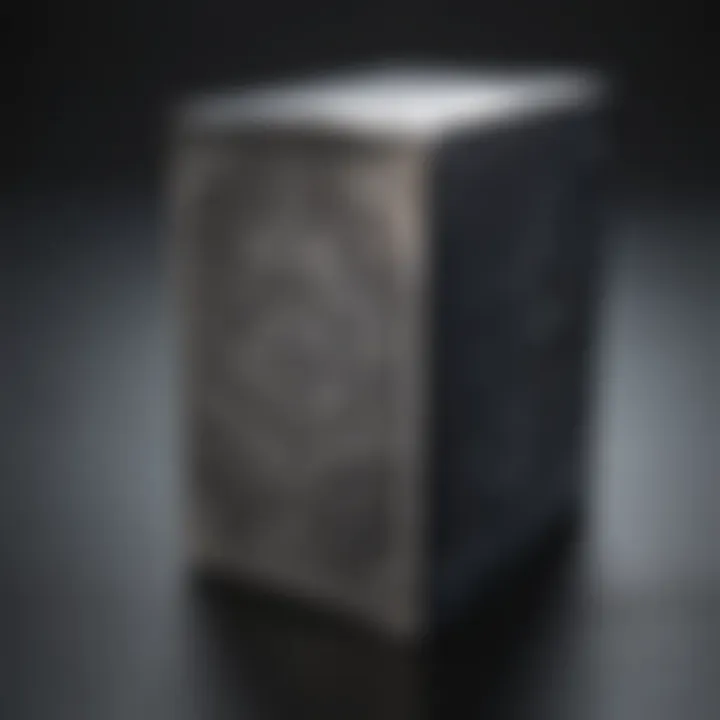
- High Resolution: The print quality is sharp, capturing minute details that appeal to readers.
- Rapid Production: The efficiency of the gravure process speeds up the production timeline, allowing publishers to meet tight deadlines.
- Versatile Transition: Gravure easily accommodates both color and black-and-white printing, catering to a wide array of publishing needs.
Decorative Printing
Gravure printing serves an essential role in decorative applications, including wallpaper, wrapping paper, and various textile printing. Its capacity for vibrant colors and intricate designs makes it ideal for creating visually appealing products. Decorative printing relies on the ability to print different textures and patterns, which gravure does with finesse. Moreover, gravure prints are often more durable against wear and tear, which is critical for items that experience frequent handling.
Considerations for decorative printing include:
- Artistic Flexibility: Designers appreciate the freedom to experiment with rich colors and patterns.
- Durability: Finished products withstand fading better than many conventional printing methods.
- Customization: Gravure offers tailored solutions to meet specific design requests and size requirements.
In summary, the applications of gravure printing across these industries are extensive and impactful. Its advantages lend themselves well to meeting the demands of today's market, particularly where quality and efficiency intersect.
Advantages of Gravure Printing
Gravure printing, a sophisticated intaglio technique, holds distinct advantages that contribute to its prevalence in various industries. Understanding these advantages is crucial for professionals navigating the complexity of printing options available today. The strengths of gravure printing can be categorized into three main areas: quality and precision, high-speed production, and cost-effectiveness for large runs.
Quality and Precision
One of the standout features of gravure printing is its ability to produce exceptionally high-quality images and text. The engravings on the gravure cylinder create a unique texture that transfers ink in a manner that is both rich and detailed. This precision is essential for applications where image quality is paramount, such as in high-end packaging and fine publications.
The ink transfer mechanism allows for even saturation across the printed area, reducing issues such as ink pooling or uneven application. The result is consistent color reproduction and sharp images that can endure scrutiny. Industry professionals often cite gravure’s accuracy in reproducing intricate designs as a key reason for its continued use.
High-Speed Production
Gravure printing is known for its remarkable speed. The setup allows for rapid printing with minimal downtime. This high-speed capability is critical in large-scale production environments where efficiency is essential. The continuous roll-to-roll format aids in maintaining a fast output, allowing printers to maximize their productivity.
Additionally, gravure printing requires less frequent changes of plates compared to other printing methods. This leads to extended print runs without significant interruptions, creating a seamless workflow that is very appealing to manufacturers. As a result, gravure is often the go-to choice for printing applications where time is a pressing concern.
Cost-Effectiveness for Large Runs
When it comes to large-volume print jobs, gravure printing offers significant cost advantages. While the initial costs of setup, such as cylinder engraving, can be relatively high, these expenses are offset by the lower per-unit cost over extensive production runs.
The scalability of gravure printing means that as the volume increases, the cost per item diminishes. This scalability makes it particularly attractive for industries like packaging, where large quantities of printed materials are required. Professionals in the field understand that for long-run projects, gravure printing becomes not only feasible but also economical.
"Gravure printing represents a blend of quality, speed, and value—three attributes that are essential for competitive industries."
Challenges in Gravure Printing
Gravure printing, despite its many advantages, faces several challenges that can impact its adoption and efficiency. Understanding these challenges is crucial for professionals who are considering this printing method. The two primary obstacles are the initial setup costs and environmental concerns. Addressing these issues allows industries to weigh the benefits against potential drawbacks and make informed decisions.
Initial Setup Costs
The initial setup costs associated with gravure printing can be significant. This method requires specialized equipment, such as engraved cylinders, which can be expensive to produce. The process of creating these cylinders involves intricate design work and precise engraving techniques, demanding skilled labor and advanced technology. Furthermore, the machinery required for printing and drying can also add to these upfront investments.
While gravure printing is known for its efficiency in high-volume production, the expense related to initial setup may deter smaller companies or those just entering the market. It is vital for businesses to conduct cost-benefit analyses to determine the return on investment for gravure printing, considering their specific production needs and market goals.
"In gravure, the cost of the cylinder printing is the most prohibitive factor when considering its use for short-run jobs."
Environmental Concerns
Environmental considerations pose another critical challenge for gravure printing. Traditional inks in this process often contain volatile organic compounds (VOCs), which can cause air pollution and health hazards. As sustainability becomes a priority for many industries, companies must navigate regulations and consumer demands for greener practices.
Moreover, the disposal of printing waste, including inks and used materials, can contribute to a more extensive environmental footprint. This reality has led many gravure printing operations to seek eco-friendly alternatives and invest in cleaner technologies. However, transitioning to sustainable practices may require additional investment, which can further complicate the initial setup costs.
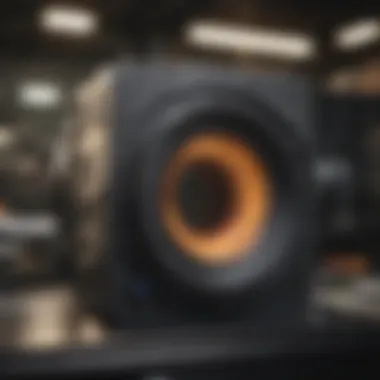
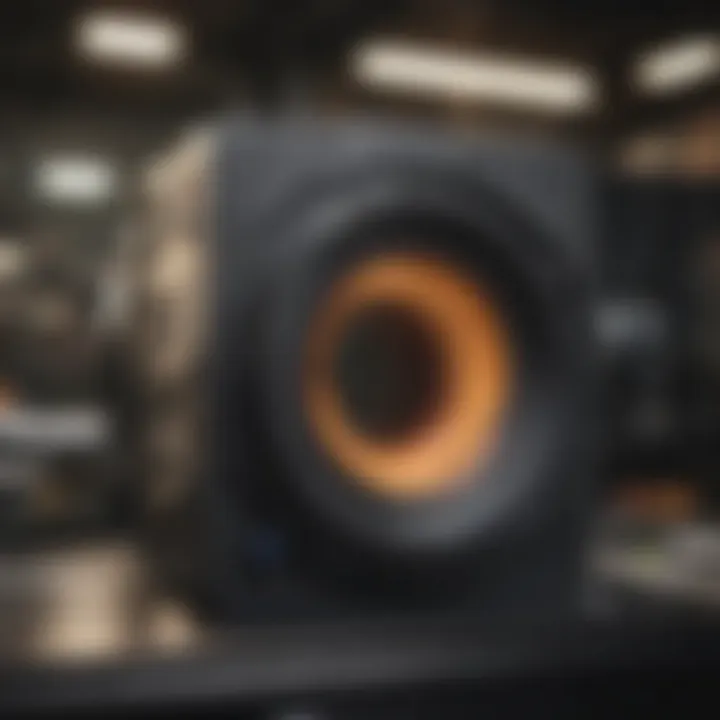
In summary, addressing the challenges of initial setup costs and environmental concerns is essential for making gravure printing a viable option. Recognizing these issues enables industry stakeholders to strategize effectively and enhance the overall sustainability of their operations.
Technological Advancements in Gravure Printing
Technological advancements in gravure printing play a pivotal role in enhancing the efficiency, quality, and sustainability of this printing method. These innovations are essential for keeping pace with industry demands. Today's gravure printing operations benefit greatly from upgraded techniques and equipment, contributing to both productivity and reduced environmental impact.
Digital Gravure Technology
Digital gravure technology has revolutionized the traditional gravure methods by integrating digital processes into pre-press operations. This technology enhances flexibility, allowing for on-demand printing. This means printers can produce smaller runs without significant setup costs. The process involves digital engraving of the image directly onto the cylinder. Moreover, color variations can be easily adapted without the need for multiple cylinders. This technology also impacts turnaround times favorably, as designs can be modified quickly and efficiently. The implementation of digital gravure also reduces waste, as there is less excess material generated compared to conventional methods.
"Digital gravure technology is reshaping how we think about printing production, minimizing waste and maximizing efficiency."
Automation in the Printing Process
Automation in the printing process further enhances the gravure printing landscape. Automated systems help streamline operations, reducing manual intervention. This advancement leads to quicker setups and consistent print quality. Modern gravure presses are often equipped with sophisticated software that aids in monitoring and adjusting the printing parameters in real-time. Automation can also help in maintaining color consistency throughout the print run. This technology boosts productivity significantly. By minimizing human error, it results in fewer defects and higher overall quality. In addition, operational costs are lower when machines perform tasks reliably and consistently. With these advancements, gravure printing stands to benefit significantly, catering better to client needs.
Sustainability in Gravure Printing
In today's printing industry, sustainability has become a crucial factor. The gravure printing process, known for its efficiency and quality, also faces scrutiny regarding its environmental impact. Understanding sustainability in gravure printing involves exploring eco-friendly alternatives and recycling practices. This section reveals the significance of these elements and how they contribute to a more sustainable future for the industry.
Eco-Friendly Inks and Materials
The choice of ink and materials plays a vital role in the sustainability of gravure printing. Traditionally, many inks contained harmful solvents and volatile organic compounds, which could create environmental and health hazards. However, there has been a shift toward eco-friendly inks. These inks are made from renewable resources or natural pigments, reducing the carbon footprint. For instance, water-based inks are gaining popularity.
Using bio-based inks can also result in less waste during production. They are often biodegradable and minimize the impact on the environment. This shift not only addresses environmental concerns but also appeals to eco-conscious consumers. Manufacturers that adopt these inks typically experience positive feedback and enhanced brand reputation.
Recycling of Materials
Recycling materials in gravure printing is essential for sustainability. The gravure process generates waste, but many companies are now implementing systems to reduce this. One significant focus is on recycling printing plates and substrates. For example, companies can reuse printing cylinders or recover materials to create new products.
Additionally, recycling paper-based substrates can close the loop in the production cycle. It not only conserves resources but also reduces energy consumption in manufacturing new materials. Many printing companies are now looking for certifications that demonstrate their commitment to recycling and sustainability.
"The gravure printing industry is gradually realizing that sustainability is not just a trend; it's a necessity."
By embracing sustainability, the gravure printing sector can enhance its image and contribute positively to the environment. With the continuous advancement of technology, and a focus on sustainable practices, gravure printing can evolve into a responsible choice in the printing landscape. Efforts in eco-friendly inks and material recycling are steps toward balancing the needs of businesses with environmental care.
Future Trends in Gravure Printing
Gravure printing, an established technique in the printing industry, faces a dynamic landscape. Understanding these future trends helps stakeholders to adapt and thrive. This section highlights a few significant trends that emerge in the industry, focusing on market growth projections and innovative applications that are beginning to take shape.
Market Growth Predictions
The gravure printing market is expected to see notable growth over the coming years. Industry analysts indicate that factors such as increasing demand for packaging solutions and a rise in online shopping will drive this expansion. Both retail packaging and food packaging sectors are integrating gravure printing due to its ability to produce vibrant and high-quality images.
According to market research, the global gravure printing market is anticipated to grow at a compound annual growth rate (CAGR) of around 3.5% to 5% over the next decade. This growth is underpinned by several elements:
- Technological Advancements: Improvements in printing technology are enhancing quality and reducing waste.
- Sustainability Initiatives: Manufacturers are focusing on eco-friendly materials and processes that appeal to environmentally conscious consumers.
- Diversification of Applications: Beyond traditional uses, gravure printing is finding applications in fields like textile design and wall coverings, further pushing demand.
In sum, the market for gravure printing is set to expand, with companies responding to trends like sustainability and technological innovation.
Innovative Applications Emerging
As the gravure printing industry evolves, it embraces innovative applications that challenge traditional uses. Today, gravure printing serves a variety of sectors. Here are some emerging applications worth noting:
- Flexible Packaging: This trend is gaining momentum in food and beverage industries. Gravure allows for complex designs and vibrant colors, ensuring products stand out on shelves.
- Labels and Decorative Printing: Custom labels made via gravure printing offer high resolution and detail, making them attractive for branding.
- Pharmaceutical Packaging: Compliance and safety are paramount here. Gravure printing's precision aids in creating packaging that meets regulatory requirements while maintaining aesthetic appeal.
- Textile Printing: Here, gravure opens doors to producing detailed patterns and colors that can define fashion lines.
The shift towards these emerging applications demonstrates the versatility and adaptability of gravure printing. By leveraging technology and responding to market needs, the industry is not just surviving; it is expanding into territories previously unimagined.
"The future of gravure printing lies in its ability to innovate and adapt to consumer demands."