Exploring the Yamazumi Process Modeling Tool for Workflow Design
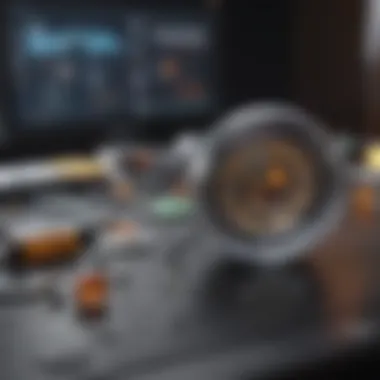
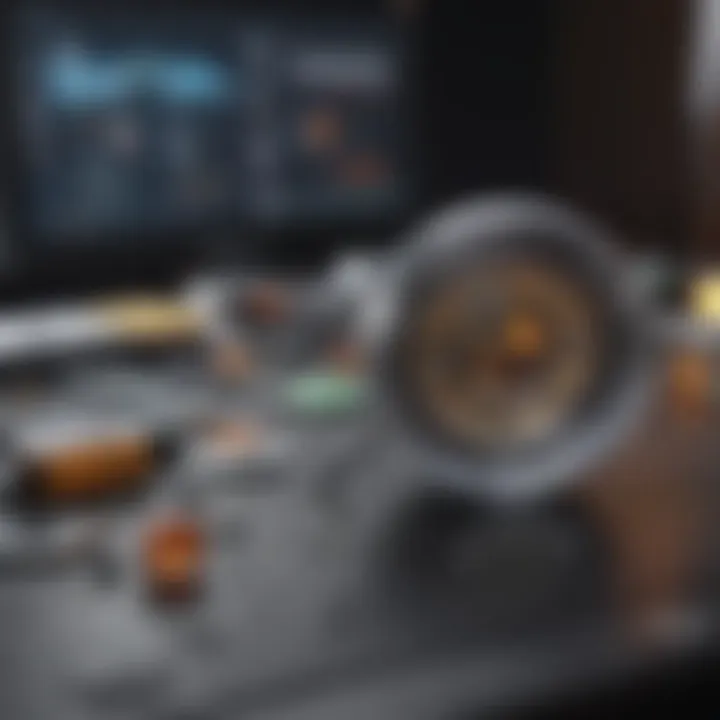
Intro
In the modern landscape of business and education, the demand for efficient workflow design has become paramount. Organizations are constantly seeking tools that allow them to visualize and analyze their processes for better decision-making. Among these tools is the Yamazumi Process Modeling Tool, which stands out due to its unique approach to workflow visualization. This model isn't just another digital tool to throw into the mix; it represents a shift towards achieving greater efficiency and clarity in various operational settings.
Effectively designing workflows involves understanding the flow of tasks, critical resource allocation, and ultimately, enhancing productivity. The Yamazumi model provides a structured way to display these elements, which can often seem tangled and complex, in a comprehensive and simple manner. By employing this tool, organizations can identify bottlenecks, streamline operations, and foster better communication among team members.
With this exploration, we will navigate through the essential elements of the Yamazumi Process Modeling Tool, highlighting its practical applications, key benefits, and future implications for various sectors. As we delve into this narrative, it will become clear how this tool can serve as a guiding light in navigating the intricacies of workflow design.
Prelude to the Yamazumi Process Modeling Tool
The Yamazumi Process Modeling Tool has carved out a critical niche in the world of workflow design and efficiency optimization. As industries face increasingly complex processes, the need for effective tools to visualize and streamline operations becomes paramount. This section shines a spotlight on the significance of the Yamazumi tool, setting the stage for a deeper exploration into its principles, benefits, and applications in various domains.
Definition and Origin
The term "Yamazumi" originates from Japan, translating to "to pile up" or "to stack up." It finds its roots in Lean manufacturing principles, aiming to enhance productivity by providing a clear visual representation of work processes. The tool facilitates a deeper understanding of workflows by stacking tasks and analyzing their durations. This approach enables users to identify inefficiencies and areas for improvement, fostering a more streamlined process. By visualizing workflow in a stacked format, the Yamazumi tool encourages teams to engage in continuous assessment and optimization of their processes.
Purpose and Importance in Process Design
The primary aim of the Yamazumi Process Modeling Tool is to reduce waste and increase efficiency within organizations. In a world where time is money, this tool serves a vital purpose in not only maximizing productivity but also streamlining resource allocation. Having the ability to visually assess workflows allows teams to identify bottlenecks or redundancies quickly, which can be dealt with in a timely manner.
Investing in a well-structured process design is akin to laying down the concrete foundation before building a skyscraper. Deficiencies in the initial design can lead to significant problems down the line. The Yamazumi tool stands out by offering precise insights, driving the conversation around workflow optimization in different sectors, such as manufacturing, healthcare, and service industries.
"A stitch in time saves nine." This adage encapsulates the essence of employing tools like Yamazumi. Identifying and addressing inefficiencies at their roots leads to monumental long-term benefits.
The importance of the Yamazumi tool stretches beyond its immediate benefits. It also fosters a culture of continuous improvement and proactive management, ensuring that teams are always looking for ways to enhance their workflows. As we delve deeper into the intricacies of the Yamazumi tool in subsequent sections, we will uncover how its application translates into tangible advantages for businesses.
Fundamental Principles of the Yamazumi Method
The Yamazumi Method serves as a foundational approach to process modeling, emphasizing clarity and efficiency in workflow design. This approach is not merely a set of techniques; it embodies a philosophy of continuous improvement and straightforward visualization. By focusing on core concepts, practitioners are better equipped to analyze workflows within various settings, thereby enhancing overall productivity. In this section, we will explore critical concepts behind the Yamazumi method and how these ideas translate into effective visual representations of processes.
Core Concepts
At the heart of the Yamazumi Method lie several core concepts that shape its application across different industries. Understanding these elements is crucial for harnessing the tool's full potential.
- Workload Balancing: The Yamazumi Process places significant emphasis on balancing workloads effectively among different tasks. When workloads are unevenly distributed, bottlenecks often arise, slowing down operations. By applying the Yamazumi technique, one can pinpoint areas that require adjustment, ensuring a smoother workflow.
- Cycle Time Analysis: Another essential concept involves the analysis of cycle times for each task or process step. By measuring how long tasks take to complete, organizations can identify inefficient practices. This facet of the method enables teams to streamline processes, leading to reduced cycle times and enhanced operational efficiency.
- Kaizen Philosophy: The Yamazumi Method also aligns closely with the Kaizen principle of continuous improvement. Regular assessments of processes, followed by incremental enhancements, reflect a commitment to achieving not just efficiency but also quality in outcome. This philosophy encourages a proactive approach to optimizing workflows, addressing inefficiencies before they become significant problems.
- Collaboration and Communication: Effective communication is intrinsic to the Yamazumi approach. Various stakeholders in a process must be on the same page to successfully identify issues and implement changes. The method encourages collaborative problem-solving, enabling teams to share insights and come up with innovative solutions.
Visual Representation of Processes
Visual representation stands as one of the defining features of the Yamazumi Method. The technique transforms complex workflows into simple visual formats. This simplification plays an important role in understanding how processes operate and identifying areas for improvement. Below are some critical aspects of this visual approach:
- Clarity through Visualization: The Yamazumi chart, often depicted in a bar graph format, displays work steps alongside cycle times and resources used. This clarity aids teams in rapidly assessing performance across tasks, making it easier to detect discrepancies between expected and actual outcomes.
- Identify Bottlenecks Effortlessly: One of the primary advantages of visual representation is its ability to highlight bottlenecks quickly. When cycle times are represented graphically, it becomes plain as day where delays are occurring. This helps teams prioritize solutions effectively.
- Facilitates Training: New employees or team members can grasp complex processes more efficiently through visual aids. The straightforward layout of a Yamazumi chart simplifies the learning curve, fostering quicker integration into teams.
- Historical Data Capture: As teams create Yamazumi charts, they can also capture historical performance data over time. This aspect allows for longitudinal analysis and fosters insights into how changes in practices affect efficiency.
In summary, the Fundamental Principles of the Yamazumi Method offer a robust framework for analyzing processes. It brings together concepts of workload balancing, cycle time analysis, and collaborative problem-solving into a cohesive approach. By prioritizing visual representation, the method enhances both understanding and communication across teams, paving the way for more streamlined and effective workflows. As organizations increasingly seek to optimize their operations, adopting the principles of the Yamazumi Method becomes more relevant than ever.
"The aim of the Yamazumi Process is to create not just a visual map of processes, but a living document that illustrates how efficiency and improvement can become part of everyday work."
Implementation Strategies in Various Industries
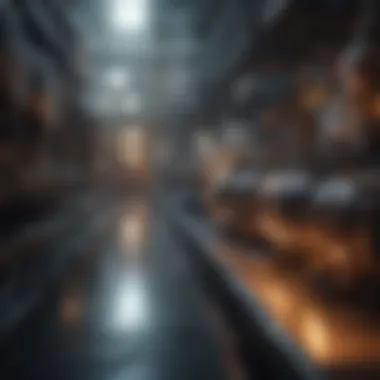
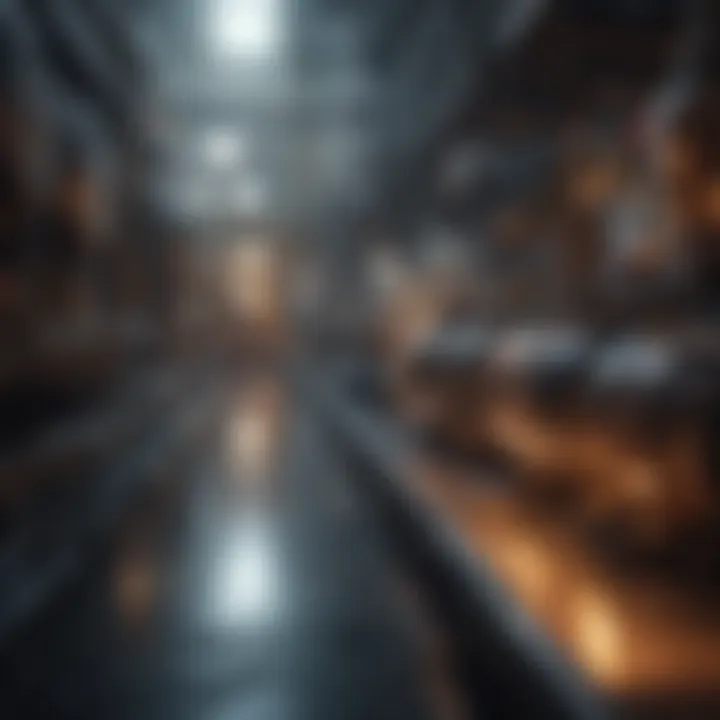
The effective application of the Yamazumi Process Modeling Tool goes beyond mere observation; it's about integrating this framework into real-world scenarios across different sectors. With distinct workflows and unique challenges present in each industry, implementation strategies must be meticulously tailored. This ensures the tool's strengths are maximized while addressing potential hurdles.
Key elements to consider when diving into these strategies include industry-specific requirements, the need for personnel training, and an understanding of cultural nuances related to workflow practices. Each sector has its way of operating, and what works in one may not necessarily apply in another, making adaptability essential.
Manufacturing Sector
In the manufacturing industry, the Yamazumi tool shines brightly by visualizing operations that are often complicated and fast-paced. Implementation in this realm focuses heavily on identifying workflow bottlenecks.
- Assessment of Existing Processes: Start with mapping out current workflows. Knowing where the time and resources are spent provides a clear baseline.
- Data-Driven Decisions: By employing the Yamazumi tool, managers can pinpoint inefficient operations. For example, if a specific assembly line consistently shows delays, visual data can spark discussions about redesigning the layout or reassigning tasks.
- Continuous Monitoring: Manufacturing doesn’t stand still—it evolves with technology and market demand. Using the Yamazumi method helps teams stay on their toes, regularly evaluating processes to ensure they still meet efficiency standards.
Healthcare Applications
The healthcare sector, with its intricate balance of patient care and administrative tasks, presents a unique landscape for the Yamazumi Process Modeling Tool.
- Streamlining Patient Flow: This tool can visibly break down patient admissions, treatment schedules, and discharge processes to eliminate redundancies.
- Resource Allocation: Properly visualized workflows can guide hospitals in task assignment and can reassure a more effective use of personnel and medical resources. For instance, it aids in recognizing when one department is overloaded while another remains underutilized.
- Training Opportunities: With an easy-to-understand visual representation, new staff can quickly grasp operational standards, reducing the onboarding time and enhancing overall efficiency.
Service Industry Adaptations
In service-oriented sectors, where customer experience is king, applying the Yamazumi tool can significantly enhance operational effectiveness.
- Mapping Customer Journeys: This involves visualizing every touchpoint a customer has with the business to ensure smooth interactions. Whether it’s a retail setting or a consulting service, every interaction can be analyzed for improvements.
- Identifying Service Gaps: Examining workflows helps in spotting areas where services may falter or take too long. For example, if a fast-food chain discovers delays in order processing, adjustments can be made to the staffing levels during peak hours.
- Feedback Integration: The clearer the process is shown, the easier it is to integrate customer feedback. A service-based company can tweak its offerings based on client interactions highlighted through the Yamazumi tool.
Efficient workflows are the backbone of industry success. When implemented correctly, tools like Yamazumi foster an environment of clarity, organization, and continuous improvement.
Benefits of the Yamazumi Tool
The Yamazumi Process Modeling Tool offers a unique set of advantages that significantly enhance workflow design across different sectors. By focusing on efficient visualization and streamlined operations, the tool provides critical insights that lead to the identification of opportunities for improvement. Understanding these benefits allows organizations to make informed decisions about adopting this methodology to elevate their processes.
Enhanced Process Visualization
A primary benefit of the Yamazumi tool is its ability to visualize complex processes in a clear and engaging manner. Unlike traditional methods, the Yamazumi approach employs bar charts to represent tasks and their durations visually. This method allows teams to perceive workflows at a glance, identifying where time is spent and opportunities for enhancement.
- Visual Clarity: Tasks can be seen side by side, making it easier to compare durations and overlap efficiently. This gives stakeholders a clearer picture without getting bogged down in dense reports or spreadsheets.
- Quick Understanding: New team members or external observers can rapidly grasp the workflow without lengthy explanations. It’s like having a roadmap that shows not just the destination but the best paths to take.
A striking aspect of this method is how it breaks task durations into manageable segments. This presents a holistic perspective on productivity and helps to unlock hidden inefficiencies that often go unnoticed in traditional models. In moving from text descriptions to visual representation, the tool fosters a more intuitive understanding of processes.
Facilitation of Bottleneck Identification
Bottlenecks are the thorn in the side of any process. They slow things down, create frustration, and often lead to missed deadlines. The Yamazumi tool makes it supremely easy to spot these trouble areas. When presented graphically, bottlenecks become glaringly obvious, indicated by long bars in the visual representation of workflows.
- Real-Time Analysis: Users can immediately see which tasks take longer than expected, prompting timely conversations about efficiency. This allows teams to pinpoint issues before they escalate.
- Targeted Solutions: Once a bottleneck is identified, organizations can design targeted interventions to alleviate these pain points. This may involve reallocating resources or redesigning certain aspects of the workflow.
By illuminating these hindrances, the Yamazumi tool offers a proactive approach to optimization. It shifts the focus from simply completing tasks to ensuring that each step in the process contributes to overall productivity.
Supporting Continuous Improvement
Continuous improvement is a philosophy that many organizations strive to embody, yet achieving it can often seem daunting. The Yamazumi method nurtures this mindset by empowering teams to regularly refine their processes.
- Iterative Updates: As workflows evolve, teams can continuously update and modify their workflow visualizations. This creates a living document that reflects current operations as they adapt and change, ensuring nothing falls through the cracks.
- Feedback Loops: The ability to visualize both processes and outcomes encourages feedback discussions among stakeholders. It’s easier to analyze what’s working and what’s not when you can see it visually.
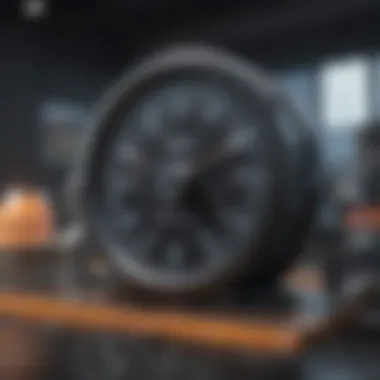
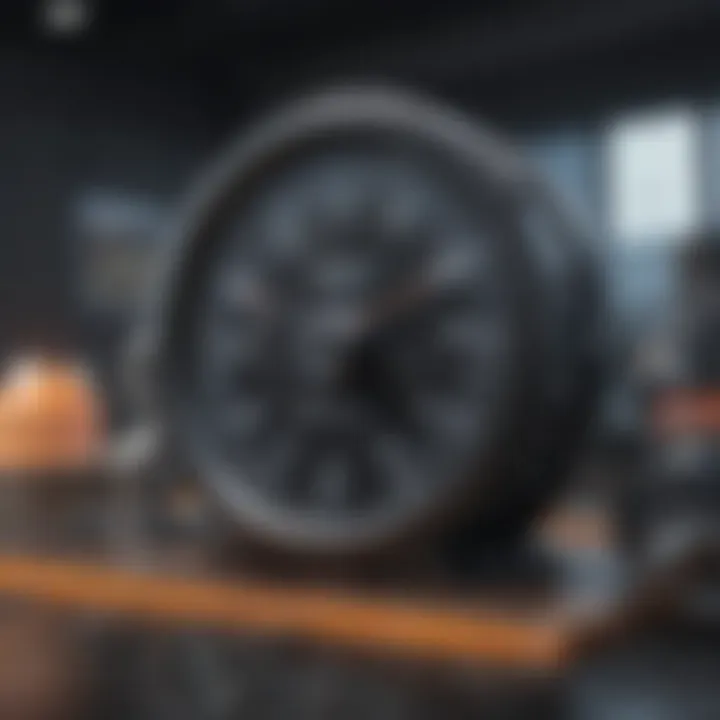
Managers can lean on the Yamazumi tool for actionable insights rather than relying on memory or outdated reports. This means organizations can foster a culture of improvement where everyone feels encouraged to contribute to process enhancements.
"The Yamazumi tool is like a lens that magnifies a business's workflow, revealing potential tweaks that can lead to significant advantages."
In summary, the benefits of the Yamazumi tool—enhanced visualization, simplification of bottleneck identification, and strong support for continuous improvement—make it an indispensable resource for organizations aiming to refine their processes. By skillfully leveraging these benefits, practitioners can cultivate a workflow that not only meets demands but excels in efficiency and clarity.
Challenges and Limitations
The Yamazumi Process Modeling Tool, while effective and beneficial, is not without its challenges and limitations. Understanding these drawbacks is crucial for anyone looking to implement the tool effectively in their organization. The goal here is to shine a light on specific elements that may present difficulties, as well as considerations when using the tool for process modeling.
Potential Misinterpretation of Data
One of the more significant challenges associated with the Yamazumi tool is the potential for misinterpretation of the data it generates. The visualization aspects, while designed to simplify complexity, can sometimes lead users to draw misleading conclusions. For instance, an overreliance on graphical representations might obscure underlying issues that aren’t directly visible in the charts. If a user misinterprets the data due to a lack of clarity about the inputs or variables, they could make decisions based on flawed insights.
To mitigate this risk, it is vital to approach data interpretation with caution. Here are a few considerations to keep in mind:
- Cross-check Data: Always compare visual outcomes with raw data. This helps ensure the interpretations made from the Yamazumi tool are aligned with factual information.
- Involve Multiple Stakeholders: Involve diverse teams in the analysis process. Different perspectives can illuminate aspects that may be overlooked by a single user.
- Enhance Training: Offering thorough training for team members on how to use the tool effectively reduces the chances of misinterpretation of the processed data.
In the end, clear communication about data results can go a long way in ensuring the right decisions are made from the information presented.
Dependence on User Expertise
Another challenge lies in the dependence on user expertise. The effectiveness of the Yamazumi tool largely hinges on the user’s familiarity with both the methodology and the specific context it is applied to. In many workplaces, employees may not possess the specialized knowledge required to maximize the benefits of the tool. As a result, this could lead to underutilization or misuse.
Consider the following factors concerning user expertise:
- Skill Levels Vary: Different members within a team may have varying levels of comfort and proficiency with process modeling, which complicates collaborative usage.
- Training Needs: Continuous education and training programs around the use of Yamazumi must be prioritized. This not only equips team members with the necessary skills but fosters confidence in their ability to interpret and apply the tool effectively.
- Ongoing Support: Establishing a mentorship program or having a Yamazumi expert available for guidance can provide needed support while teams navigate through their learning curves.
Comparative Analysis with Other Process Modeling Tools
In the dynamic field of process management, the choice of modeling tools is critical. Understanding how the Yamazumi Process Modeling Tool compares with other methodologies can significantly influence the effectiveness and efficiency of workflow design. A comparative analysis serves not only to highlight the unique attributes of the Yamazumi method but also to provide a broader context for decision-makers in various sectors. By pinpointing the strengths and shortcomings of various tools, professionals can make informed decisions that align with their operational needs.
Yamazumi vs. Flowchart Methods
Flowcharts have been a staple in process modeling for decades. They offer a straightforward way to visualize processes using standardized symbols that represent steps and decisions. However, where flowcharts excel in simplicity, they often lack depth in illustrating complex interactions among tasks.
When juxtaposed with the Yamazumi tool, it's evident that Yamazumi provides richer contextual insights. While flowcharts portray tasks linearly, Yamazumi focuses on resource allocation and workload balancing. This approach not only facilitates better comprehension of a process but also highlights potential workflow bottlenecks.
- Key Differences:
- Visualization Depth: Yamazumi offers layered insights into workflow intricacies, unlike flowcharts.
- Resource Allocation: The tool emphasizes task distribution and workload management, which can lead to higher productivity.
- Data Analysis: With Yamazumi, users can utilize data to inform decisions, while flowcharts typically remain static representations.
In practice, individuals using Yamazumi often report not just an understanding of the steps involved, but also the impact of resource utilization on overall output. The Yamazumi method can be particularly beneficial in industries needing agility, making it a tool for future-ready organizations.
Decision Trees and Their Limitations
Moving on to decision trees, currently popular among organizations for mapping options and decisions, they certainly carry weight. Yet, they fall into a trap of oversimplifying complexities. Decision trees outline choices based on binary outcomes, which often results in ignoring nuanced scenarios. In situations requiring higher granularity—like those encountered in resource management—this can lead to missed opportunities or misinformed choices.
A comparative analysis reveals several notable limitations of decision trees against the Yamazumi approach:
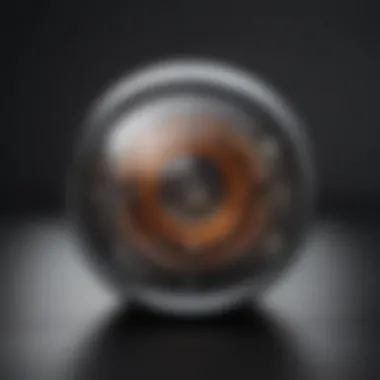
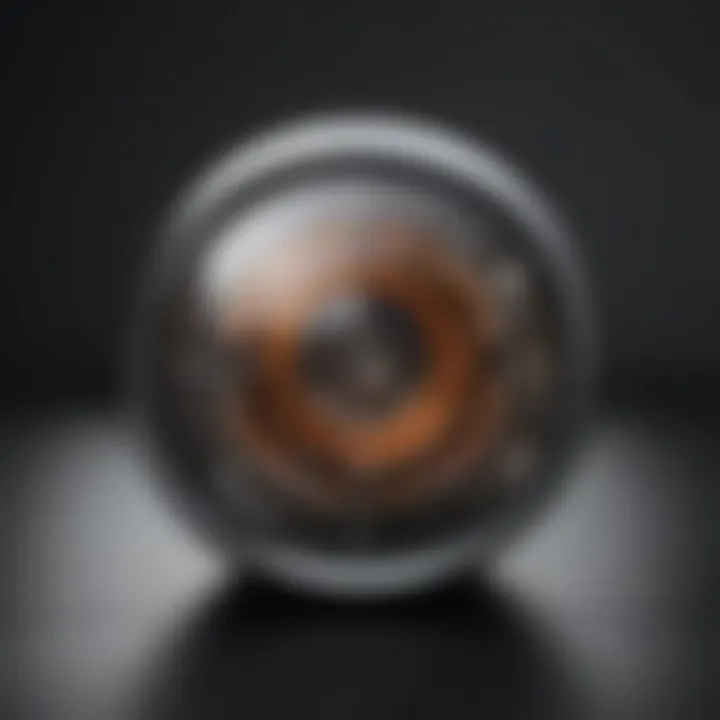
- Complexity Handling: Decision trees may falter under layered processes, unable to effectively show interdependencies.
- Temporal Aspects: Time-based elements in workflows can be difficult to represent in a decision tree layout.
- Quantitative Measures: Yamazumi provides tools for assessing not just yes-or-no decisions but also resource utilization effectiveness.
It’s clear that while decision trees can guide initial decision-making, relying solely on them could hinder a comprehensive understanding of intricate workflows, especially in multi-faceted environments.
"Choosing the right process modeling tool can make the difference between effective optimization and perpetual bottlenecks."
Future Perspectives of the Yamazumi Process Modeling Tool
The Yamazumi Process Modeling Tool holds significant promise for the future, particularly as industries grapple with evolving challenges and opportunities. As organizations seek not only to improve efficiency but also to adapt to rapidly changing environments, the Yamazumi approach becomes increasingly relevant. This section sheds light on the pivotal elements that shape its future potential as it evolves alongside digital advancements and emerging technologies.
Integration with Digital Technologies
In today’s tech-savvy world, integrating digital tools into processes is no longer optional; it's a necessity. The Yamazumi tool is poised to benefit immensely from the digitalization trend. By merging it with various digital technologies, organizations can enhance its capabilities. Consider the potential of cloud-based platforms. These platforms allow teams to access and collaborate on Yamazumi models from anywhere, breaking down geographical barriers and fostering a more dynamic approach to workflow analysis.
Furthermore, the incorporation of real-time data can fundamentally change how organizations utilize the Yamazumi method. Imagine a scenario where live data feeds into the tool, instantly updating workflow visualizations according to current operations. This level of responsiveness could allow for quicker decision-making and more agile adaptations to bottlenecks or inefficiencies.
Some key points to consider regarding integration include:
- Interoperability: Ensuring Yamazumi can work seamlessly with other digital tools like ERP and CRM systems.
- User Interface Enhancements: The user experience can be vastly improved with responsive dashboards, making insights clearer at a glance.
- Predictive Analytics: Linking Yamazumi with data analytics tools can provide insights into potential future bottlenecks based on historical data patterns.
The energy around the future of the Yamazumi tool lies in its adaptability to blend with the digital fabric of workplaces. As organizations invest in technology, those employing the Yamazumi method will likely find themselves with richer, more meaningful data at their fingertips.
Potential for Machine Learning Inclusion
Machine learning is revolutionizing numerous fields and brings a unique perspective to the Yamazumi Process Modeling Tool. Incorporating machine learning algorithms can transform how workflows are analyzed and optimized. For instance, instead of merely visualizing processes, machine learning can uncover hidden patterns within the data that human analysis might miss.
Here are some compelling ways machine learning can amplify the capabilities of the Yamazumi tool:
- Automated Bottleneck Detection: Advanced algorithms could flag inefficiencies in real time, providing not only alerts but also potential solutions based on historical data.
- Enhanced Predictive Capabilities: Using past behavior and performance, the tool could predict future workflow trends or potential issues, allowing preemptive actions to be taken.
- Personalization: By learning from user interaction, the tool could tailor visualizations and suggestions, optimizing experiences for diverse user needs.
In summary, the future perspectives of the Yamazumi Process Modeling Tool are rich with possibilities. By embracing digital technologies and leveraging machine learning, organizations can further enhance their workflow design and optimization strategies. This could ultimately lead to not only improved efficiency but also transformed approaches to continuous improvement in operations.
"A tool is only as powerful as the way in which it is used."
This adage rings true for the Yamazumi Process Modeling Tool as it sits at the intersection of technology and process efficiency, ready to evolve with the times.
Culmination
When considering the depth of the Yamazumi Process Modeling Tool, its relevance in today's dynamic work environments cannot be overstated. This tool stands as a beacon for clarity in workflow design, providing a lens through which complexities can be examined and streamlined. By centering the conversation around how processes can be visualized and analyzed, organizations can draw important insights that lead to improved decision-making and greater efficiency.
Summary of Key Insights
The exploration of the Yamazumi Process Modeling Tool reveals several key insights:
- Visual Clarity: One of the tool's standout features is its ability to succinctly represent processes. In a world where data can often be overwhelming, this clarity aids teams in grasping workflows and identifying potential improvements.
- Bottleneck Identification: A significant advantage lies in its capacity to spotlight disruptions in workflow. By visualizing the flow, stakeholders can pinpoint areas causing delays and tackle them effectively.
- Encouragement of Continuous Improvement: The Yamazumi approach promotes an ongoing culture of optimization. Instead of merely solving problems as they arise, it fosters an environment where processes are revisited and reworked regularly.
These insights not only form the backbone of understanding the tool but also emphasize its applicability across various domains -- be it manufacturing, healthcare, or service industries.
Final Thoughts on Process Optimization
In the end, embracing the Yamazumi Process Modeling Tool can significantly alter the landscape of operational efficiency. As organizations continue to evolve, the need to harness effective process visualization becomes more pressing. Thus, the Yamazumi method stands out, not just as a tool, but as a philosophy aimed at fostering a sharper understanding of workflows.
To truly reap the benefits, organizations must be willing to invest time in understanding how this tool can be integrated into their existing structures. The pursuit of process optimization is not merely a one-time endeavor but rather a sustained commitment to continuous analysis and improvement.
"To optimize is to thrive within the chaos of production. The Yamazumi tool lights the way."
In a world saturated with complexity, tools that offer simplicity and clarity are invaluable. The future will likely see the Yenazumi Process Modeling Tool evolving even further, driven by technological advances and the relentless pursuit of efficiency.