Innovative Six Sigma Projects in Manufacturing
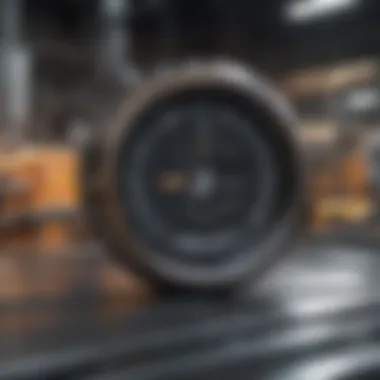
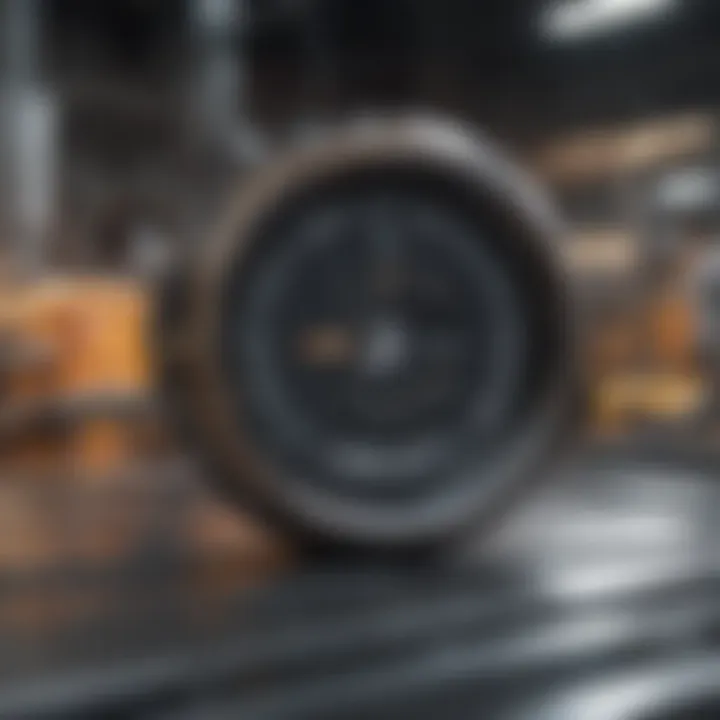
Intro
The manufacturing sector is increasingly turning to Six Sigma methodologies to improve efficiency and maintain quality control. It is not merely a trend; it is a necessity in a competitive global market. This article seeks to explore notable examples of Six Sigma projects implemented within the manufacturing domain. By examining these cases, we can uncover the systematic approaches, tools, and results that defined their success. Each case study presented here offers insight into the applicability of Six Sigma practices in real-world manufacturing settings, emphasizing their impact on operational performance.
Article Overview
Summary of Key Findings
Six Sigma projects in manufacturing have consistently resulted in significant improvements in quality and efficiency. They often employ data-driven strategies to analyze and resolve process gaps. Projects examined in this article demonstrate various facets of Six Sigma, showcasing its flexibility in addressing different challenges. From reducing defects in production lines to enhancing process cycle times, the outcomes reveal substantive benefits such as cost savings and increased customer satisfaction.
Research Objectives
The primary aim is to dissect several exemplary Six Sigma projects to provide a clearer understanding of their methodologies and results. Each case will illustrate critical components such as objectives, processes undertaken, and final outcomes. This exploration seeks to guide students, researchers, and professionals by presenting the strategic value of Six Sigma in manufacturing settings.
Key Results and Discussions
Main Findings
Through the investigation of multiple Six Sigma projects, several main findings emerge:
- Enhanced Efficiency: Projects successfully streamlined operations, leading to reduced cycle times.
- Quality Improvement: Significant reductions in defect rates were recorded, improving final product quality.
- Cost Reductions: Implementation of Six Sigma tools resulted in measurable cost savings through waste reduction.
Implications of Findings
The findings showcase that Six Sigma is a viable tool for manufacturers aiming to optimize their operations. Adoption of such methodologies not only improves immediate operational results but also builds a foundation for continuous improvement. Therefore, understanding Six Sigma techniques can be vital in achieving long-term competitiveness in the manufacturing landscape.
"Six Sigma is not just a methodology; it is a culture change that drives enduring improvements in efficiency and quality."
Integrating the lessons learned from these projects can lead to fostering a culture of excellence in production environments. Overall, exploring these examples can serve as both inspiration and practical guidance for implementing Six Sigma strategies in diverse manufacturing contexts.
Understanding Six Sigma
Six Sigma plays a crucial role in manufacturing. It establishes a structured approach to enhance production while minimizing defects. Its significance arises from the need for continual improvement in an ever-competitive manufacturing landscape. By embracing its principles, companies can streamline their processes and deliver higher quality products to their customers.
Historical Context
The origins of Six Sigma date back to the 1980s. It was developed by engineers at Motorola. The aim was to enhance process quality and efficiency. Over time, the methodology evolved. Businesses began adopting it beyond Motorola, particularly in manufacturing settings. This widespread adoption was driven by its effectiveness in reducing defects and improving overall performance.
Key Principles of Six Sigma
Six Sigma is built on key principles. These include a strong focus on the customer, data-driven decision-making, and a commitment to continuous improvement. Understanding these principles is essential for implementing Six Sigma. It enables teams to identify problem areas and implement changes effectively. Successful application of these principles leads to better quality, higher customer satisfaction, and significant cost savings.
DMAIC Methodology Defined
The DMAIC methodology is central to Six Sigma projects. It stands for Define, Measure, Analyze, Improve, and Control. Each step plays a specific role in driving improvements in manufacturing processes.
Define
The Define phase outlines the problem to solve. Key characteristics include identifying the project goals and customer requirements. Define is beneficial as it sets a clear direction for the project. It helps ensure that all stakeholders align on objectives from the start. This unique feature of clarity helps avoid confusion in later stages of the project.
Measure
The Measure phase involves collecting relevant data. Data collection is crucial to understand current process performance. This phase helps establish baselines for comparison. A strong focus on metrics makes Measure a vital step. The unique feature of this stage is its reliance on quantifiable data, which adds objectivity. This approach can reveal areas needing attention but also may require large amounts of data.
Analyze
Analysis is where the team examines the data collected. The goal is to find root causes of defects or inefficiencies. This phase uses statistical tools to interpret data. This analytical focus sets Analyze apart from other steps. It enables teams to make informed decisions based on factual evidence. However, this stage can sometimes be complex, requiring specific expertise.
Improve
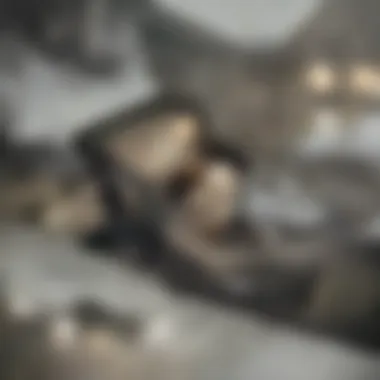
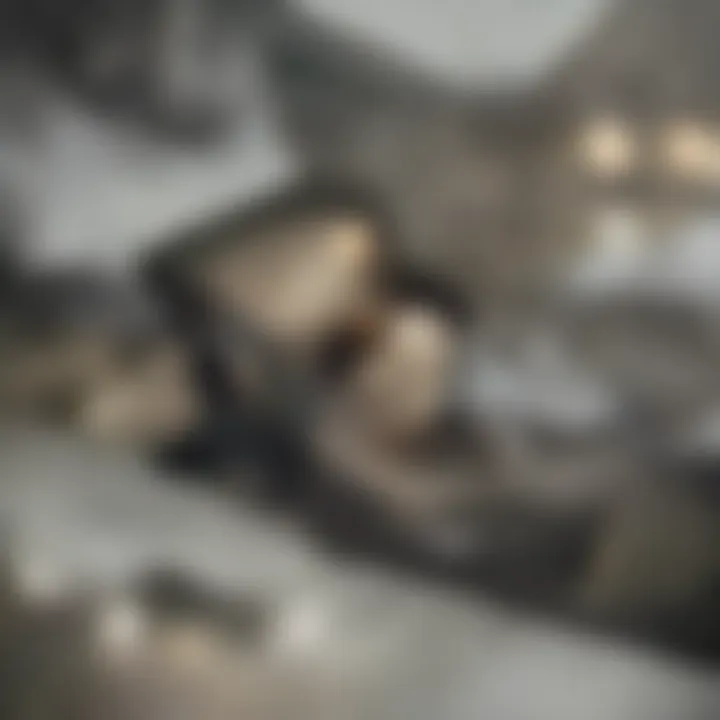
In the Improve phase, solutions are developed and tested. This step transforms analysis into actionable plans. The key characteristic of Improve lies in its experimental nature. It encourages innovative thinking to address identified issues. This unique feature can lead to breakthrough improvements. However, it may also introduce risks if changes are not carefully monitored.
Control
Control reinforces the improvements made. This phase ensures that the changes are sustainable. By establishing control mechanisms, teams can maintain gains over time. The key characteristic of Control is its emphasis on monitoring processes continuously. Its unique aspect is the focus on preventing slippage into old habits. However, it may demand ongoing efforts to ensure compliance from all stakeholders.
Understanding the DMAIC methodology is vital for applying Six Sigma effectively in any manufacturing context. Each phase contributes to a structured approach that enhances quality and efficiency.
Importance of Six Sigma in Manufacturing
Six Sigma is a systematic approach primarily used in manufacturing to improve processes, reduce defects, and ensure quality. Its significance in manufacturing is profound, as it shapes operations by focusing on efficiency and customer satisfaction. This methodology implements quantitative measurements, aiming to enhance product quality while simultaneously reducing costs.
Quality Assurance
Quality assurance is essential in manufacturing. Six Sigma provides a structured framework that encourages companies to assess their processes rigorously. By employing the DMAIC methodology, manufacturers can identify problem areas and enforce standards. Regular monitoring and measurement feature prominently in this approach, which helps guarantee that products meet quality specifications consistently. For example, a project aimed at defect reduction in automotive parts might involve frequent inspections and feedback loops, which cultivate a culture of attentiveness to quality. Ultimately, associations between high-quality products and brand loyalty become clear.
Cost Reduction
Cost reduction through Six Sigma not only focuses on cutting expenses but also emphasizes reducing waste. Many manufactuers apply this strategy to streamline operations and minimize resource consumption. Six Sigma fosters an environment where employees entertain novel ideas for process improvement. When implemented correctly, a company can see notable decreases in production costs and increased profitability. This points to the importance of Six Sigma as a tool not just for quality but also for financial health.
Process Optimization
Process optimization involves refining workflows for better performance. Implementing Six Sigma leads to a deep analysis of current processes. It allows organizations to evaluate bottlenecks and inefficiencies systematically. For instance, in pharmaceutical manufacturing, applying Six Sigma tools can result in significant cycle time reductions. By using data-driven decisions, firms can assess how to eliminate unnecessary steps and improve throughput. A pivotal takeaway is that optimizing a process not only improves manufacturing efficiency but can also enhance workforce satisfaction, leading to improved retention and morale.
Adopting Six Sigma means committing to continuous improvement, ultimately leading to more reliable products and satisfied customers.
Examples of Six Sigma Projects
The practical applications of Six Sigma in manufacturing reflect its capacity to enhance efficiency and quality control. Six Sigma projects serve as case studies that highlight the various ways this methodology meets specific challenges present in production environments. These examples not only demonstrate the effectiveness of Six Sigma but also provide insights into best practices, common pitfalls, and strategic recommendations.
Project One: Defect Reduction in Automotive Parts
Project Objectives
The objective of this project was to reduce the rate of defects in automotive parts. Defect reduction is crucial in the automotive industry due to the high standards of safety and reliability that consumers expect. A primary characteristic of this objective is its alignment with industry regulations, which demand stringent quality control measures. The unique feature of this project was its focus on specific defect types based on historical data. Addressing defect rates directly contributes to improving overall production quality and cost-effectiveness.
Methodology
The methodology employed in this project involved the DMAIC framework, specifically analyzing the defects through statistical tools. The use of root cause analysis was a key characteristic of the approach, facilitating a data-driven journey to identifying inefficiencies. A notable feature was the involvement of cross-functional teams, which allowed for diverse perspectives on the manufacturing process. The advantages of this methodology include systematic data analysis and the potential for sustained improvements, although it may require a commitment of resources and time.
Results Achieved
Outcomes included a significant reduction in defect rates, which directly translated to lower warranty claims and enhanced customer satisfaction. The success of the initiative showcased the importance of continuous monitoring. A crucial aspect of these results was the establishment of a lasting quality culture within the organization. Despite the benefits, challenges remained, such as maintaining the focus on quality over time.
Project Two: Streamlining Production Line in Electronics
Project Objectives
This project's objective was to streamline the production line to enhance throughput without sacrificing quality. Efficiency in production lines is vital in the highly competitive electronics market. A key characteristic of this objective included the focus on reducing cycle times. The unique feature of this project was the implementation of lean principles alongside Six Sigma methodologies, creating a comprehensive approach to production optimization.
Methodology
The methodology involved mapping the production process to identify bottlenecks. This project utilized value stream mapping as a significant part of its approach. This method's advantages are clear visualization and clarity in identifying inefficiencies in the production phase. However, its execution required thorough training for employees who were unfamiliar with these tools, which can create initial resistance.
Results Achieved
Results of the project included a marked improvement in lead times and a significant increase in production capacity. Achieving this objective reflected the ability to respond faster to market demands. Additionally, there was a noticeable boost in staff morale as workflows became smoother. Challenges persisted, particularly in sustaining momentum once initial improvements were observed.
Project Three: Reducing Cycle Time in Pharmaceutical Manufacturing
Project Objectives
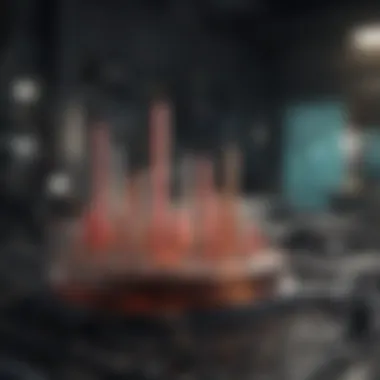
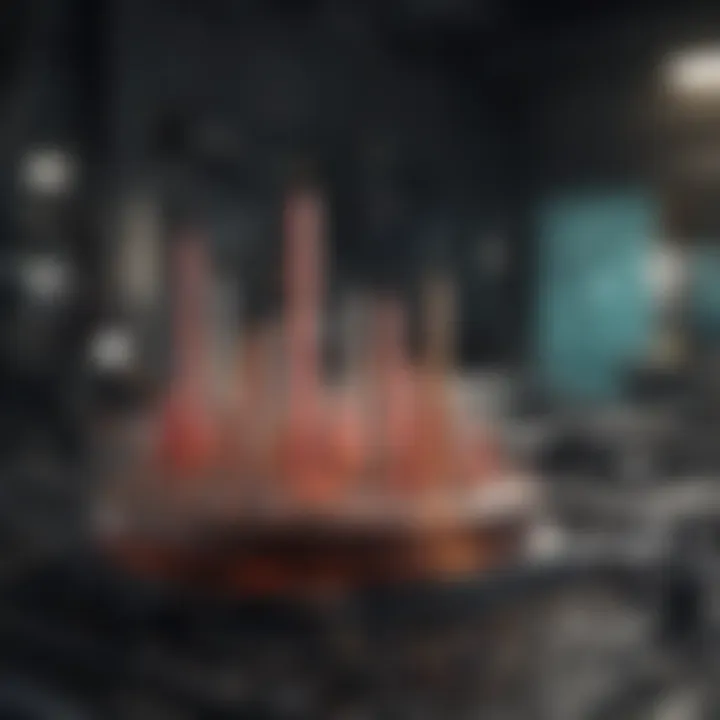
The focus here was on reducing cycle times in pharmaceutical manufacturing to expedite product delivery. Timeliness is critical in this sector, where market dynamics can change rapidly. The key characteristic of these objectives is their direct impact on profitability and market competitiveness. The project's unique aspect was the integration of regulatory requirements which must be adhered to closely, adding complexity.
Methodology
The methodology employed included extensive time studies and process simulation techniques. Detailed analysis provided insight into process flows and timings. A defining feature of this methodology is the reliance on advanced technology tools and simulations, enabling precise adjustments to the process. However, initial costs associated with technology adoption must be managed while aligning with budget constraints.
Results Achieved
The results achieved focused on a significant decrease in overall cycle time and a subsequent increase in the number of batches produced. These outcomes contributed to improved market responsiveness. Importantly, the results highlighted areas for future enhancements, showcasing the iterative nature of Six Sigma. However, constant vigilance was necessary to maintain these gains.
Project Four: Enhancing Supply Chain Efficiency
Project Objectives
The primary objective was to improve supply chain efficiency by reducing lead times and optimizing supplier performance. In today's global economy, supply chains are prone to complexities which require robust management. A defining characteristic of this objective involves real-time tracking of materials. The unique feature of this project was the implementation of digital tools to facilitate better communication across the supply chain.
Methodology
The methodology combined Six Sigma with advanced analytics to become data-centric. Predictive models assessed supplier performance, which helped in identifying the best supply partners. The advantages of this method include enhanced decision-making capabilities, although interpretation of data requires skilled personnel to parse insights correctly.
Results Achieved
The results indicated reduced operational costs and improved service levels, directly influencing customer satisfaction. Highlighting this success was the reduction of delays in the supply chain. However, maintaining supplier relationships requires ongoing effort and open lines of communication.
Project Five: Inventory Management Optimization
Project Objectives
This project aimed to optimize inventory management to reduce holding costs and improve turnover ratios. In manufacturing, effective inventory management can lead to significant cost savings. A key objective here was achieving a just-in-time inventory approach, which minimizes stock levels while meeting demand. The uniqueness of this project lay in the incorporation of IoT devices and real-time data monitoring.
Methodology
The methodology included sophisticated forecasting techniques to predict inventory needs accurately. The incorporation of statistical tools enabled better alignment between supply and demand. This approach's primary characteristic is agility, allowing timelier responses to market changes. Naturally, this methodology faced challenges relating to data accuracy and forecasting reliability.
Results Achieved
Results of the inventory project included a noticeable decrease in carrying costs and enhanced cash flow. This project allowed the company to move more quickly in adapting to market demands, enhancing competitive advantage. Though successful, it required continual adjustments to stay aligned with market conditions.
Project Six: Improving Customer Satisfaction in Manufacturing
Project Objectives
This project's goal was to improve customer satisfaction scores through enhancement of product quality and service delivery. Customer satisfaction is a critical measure of business performance. A hallmark characteristic involved soliciting direct feedback from customers. The unique element of the objectives was integrating customer-centric approaches into existing processes to ensure responsiveness.
Methodology
The methodology used voice of the customer techniques to gather insights, which informed subsequent improvements. The project employed survey methodologies and focus groups to ensure diverse perspectives were captured. Key advantages include a deeper understanding of customer needs but also the risk of bias if feedback is not representative.
Results Achieved
Achieved results included increased customer satisfaction ratings and a positive reputation within the market. Increased loyalty led to greater repeat business. Despite achieving goals, ongoing efforts to adapt to changing consumer preferences need to be a continual focus for sustained success.
Challenges in Implementing Six Sigma in Manufacturing
Implementing Six Sigma in manufacturing is not without hurdles. The challenges encountered can significantly impact the effectiveness of Six Sigma projects. Understanding these challenges is crucial as it allows for strategies to mitigate their effects. Three main areas often cause difficulties: resistance to change, skill gaps in the workforce, and resource allocation issues. Addressing these concerns can lead to successful Six Sigma integration and ultimately enhance manufacturing processes.
Resistance to Change
Resistance to change is a common barrier in many organizations, and manufacturing is no exception. Employees often feel threatened by new processes or methodologies. This sentiment arises from the fear of their roles being altered or automated. Management must actively work to cultivate a culture that embraces change.
Organizations should conduct training and workshops to ease employees into the new methodologies. When employees understand the benefits of Six Sigma, such as improved efficiency and quality, they may be more willing to accept the changes.
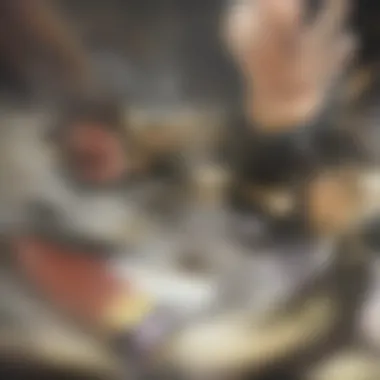
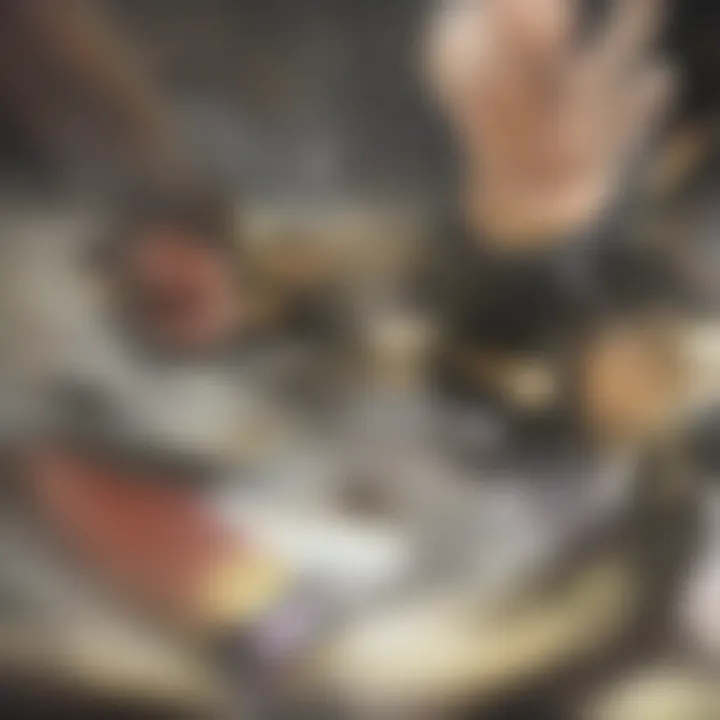
Key strategies include:
- Transparent Communication: Clearly explaining the reasons behind Six Sigma implementation fosters trust.
- Engagement in Decision-Making: Involving employees in the process creates a sense of ownership.
- Providing Support: Ongoing support reassures employees that they are not alone during the transition.
"Without addressing resistance to change, Six Sigma initiatives may falter before they truly begin."
Skill Gaps in Workforce
Having a skilled workforce is vital for the successful execution of Six Sigma projects. However, gaps in skills can hinder implementation. Many employees may not possess the necessary training in Six Sigma principles, data analysis, or process improvement techniques. To overcome this issue, companies should invest in training and development programs.
These programs should focus on:
- Basic Six Sigma Training: Ensure all relevant employees have an understanding of Six Sigma fundamentals.
- Advanced Techniques: Offer specialized training on data collection and statistical analysis.
- Regular Workshops: Continuous learning opportunities help keep skills fresh and applicable.
Encouraging a learning culture not only enhances skills but also boosts morale, fostering an environment primed for Six Sigma success.
Resource Allocation Issues
Resource allocation also poses a significant challenge. Projects may stall if there are insufficient time, money, or personnel assigned to Six Sigma initiatives. Companies often prioritize short-term goals, neglecting the long-term investments needed for Six Sigma projects to flourish.
To resolve resource allocation issues, organizations need to:
- Commit Leadership Support: Management must emphasize the importance of Six Sigma and allocate necessary resources.
- Define Clear Objectives: Setting clear goals ensures that the right resources are directed toward achieving them.
- Monitor Progress: Regular assessments help to keep projects on track and adjust resource needs as necessary.
By addressing these resource-related challenges proactively, companies can create a more favorable environment for Six Sigma initiatives.
Future of Six Sigma in Manufacturing
The future of Six Sigma in manufacturing is a critical topic as it highlights the ongoing evolution and potential impacts of this methodology. As the global manufacturing landscape becomes increasingly complex and competitive, the relevance of Six Sigma remains high. It provides a framework for enhancing operational efficiency while ensuring quality. Factors such as technological advancements, sustainability concerns, and new methodologies will shape the next generation of Six Sigma projects.
One notable advantage of focusing on the future of Six Sigma is its adaptability to emerging technologies and industry demands. This adaptability makes Six Sigma not just a tool for problem-solving but also a strategic asset in achieving long-term objectives. Companies embracing Six Sigma can leverage new tools to gather real-time data, analyze processes, and implement improvements more effectively.
"Success in the manufacturing sector increasingly relies on agility and quality. Six Sigma provides a pathway to achieving both through data-driven decisions."
Emphasis on Technology Integration
Technological integration plays an essential role in enhancing the effectiveness of Six Sigma processes. Modern manufacturing relies heavily on automation, artificial intelligence, and data analytics. By harnessing these technologies, organizations can achieve higher precision and efficiency in their Six Sigma initiatives.
For instance, the use of real-time data analytics can streamline the DMAIC (Define, Measure, Analyze, Improve, Control) methodology. By having immediate access to process performance data, teams can identify issues sooner and respond quicker. Tools such as predictive analytics can even forecast potential defects before they occur, allowing for proactive measures.
Another crucial aspect is the integration of Internet of Things (IoT) devices within manufacturing systems. These devices can monitor equipment performance continuously, providing valuable insights for Six Sigma projects aimed at reducing downtime and improving quality.
Sustainability Considerations
The future of Six Sigma in manufacturing cannot overlook sustainability. As industries face increasing pressure to operate in environmentally responsible ways, integrating sustainable practices into Six Sigma principles becomes vital. Eco-friendly practices not only cater to regulatory requirements but also enhance corporate reputation and market competitiveness.
Implementing Six Sigma projects with a sustainability focus might involve reducing waste during production, improving energy efficiency, or sourcing materials responsibly. These practices can lead to significant cost savings and more efficient resource use.
Some companies have begun to measure success not only in terms of profit but also in terms of environmental impact. They utilize Six Sigma to develop processes that minimize their ecological footprint, which aligns well with evolving consumer preferences for sustainable products.
Evolving Methodologies
Evolving methodologies in Six Sigma signify the need for continuous improvement and adaptation to meet changing industry needs. Traditional Six Sigma may not suffice on its own amidst rapid technological changes and shifting market demands.
New approaches, such as Lean Six Sigma, combine Lean manufacturing principles with Six Sigma tools. This hybridization allows organizations to focus on waste reduction while maintaining quality control. Another emerging trend is the use of Agile Six Sigma, which emphasizes adaptable project management and responsiveness.
As companies gather more data sources, the integration of advanced analytics will shape how Six Sigma projects are conceived and executed. Analysis will become more comprehensive, factoring in variables that were previously overlooked.
Ending
The conclusion of this article is of high significance, as it encapsulates the core insights regarding the application of Six Sigma in manufacturing projects. By reviewing the demonstrated examples and drawing from each case study, it becomes clear that Six Sigma is not merely a set of tools but a transformative approach that addresses complex challenges within various manufacturing processes. The benefits that arise from implementing Six Sigma methodologies are multifaceted.
Summary of Key Findings
Each project discussed reveals critical themes about the impact of Six Sigma. The reduction of defects in automotive parts not only improved product quality but also significantly lowered operational costs. Streamlining the production line in electronics showed how efficiency gains can translate into better resource utilization. The cycle time reduction in pharmaceutical manufacturing provided a clear indication of how timely production can enhance market responsiveness. Moreover, enhancing supply chain efficiency and optimizing inventory management underscore the necessity for adaptability in manufacturing. Lastly, the focus on customer satisfaction illustrates how Six Sigma reinforces the link between product excellence and customer loyalty. Each of these projects demonstrates that Six Sigma creates clear metrics and structured methodologies to drive continuous improvement.
"Six Sigma is about making informed decisions through data, improving processes, and delivering greater value to customers."
Final Thoughts on Six Sigma Projects in Manufacturing
In closing, Six Sigma stands out as a strategic asset for manufacturers seeking to enhance both quality and efficiency. The importance of these case studies is further augmented when considering the adaptability of Six Sigma principles to various manufacturing sectors. Organizations willing to embrace these methods can achieve significant operational enhancements. Moreover, as industries evolve, ongoing education and adaptation of Six Sigma practices are vital for sustaining competitive advantages. In a landscape marked by rapid technological changes and shifting customer expectations, incorporating Six Sigma can enable manufacturers to maintain relevance and achieve long-term growth.