Exploring Remote Laser Cutting: Technology and Future
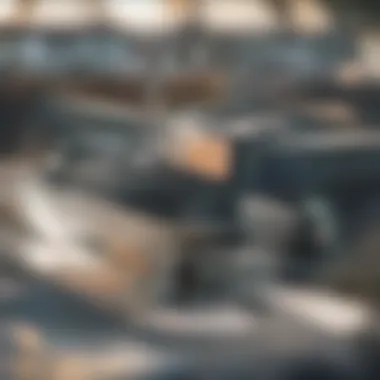
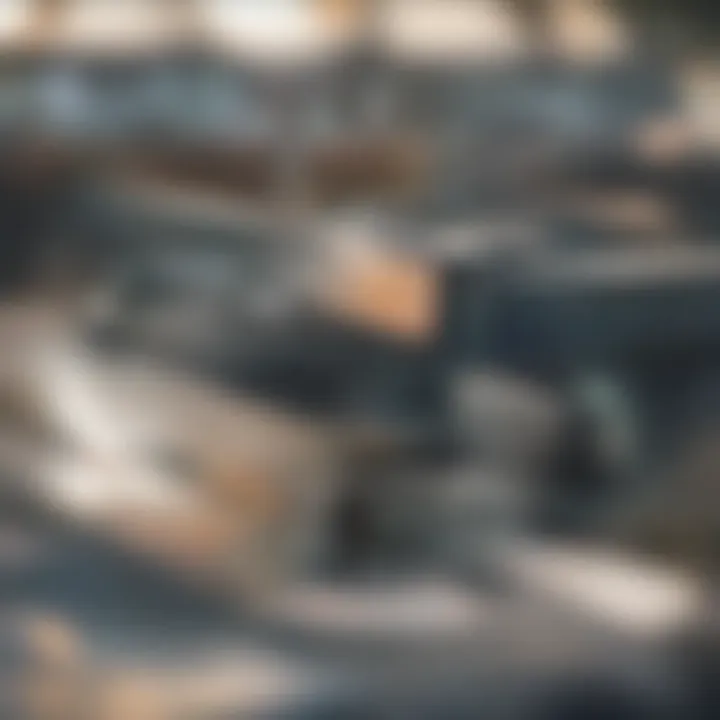
Intro
The landscape of manufacturing and industrial processes is evolving with technological advancements. One notable innovation is remote laser cutting, a process that is increasing in both efficacy and precision. This article explores remote laser cutting, detailing its technology, applications, and future. By understanding the principles behind this method, its various uses, and the landscape surrounding it, one can appreciate its impact on modern production techniques.
Article Overview
Summary of Key Findings
Remote laser cutting operates on the principles of high-speed laser technology. It offers several advantages over conventional cutting methods, which include increased speed, reduced waste, and improved accuracy. Industries such as automotive, aerospace, and electronics are adopting this technology due to its versatility and efficiency.
Research Objectives
The objective of this article is to
- examine the underlying technology of remote laser cutting,
- highlight its practical applications in various industries,
- assess safety measures and economic considerations,
- forecast future trends and developments in the field of laser cutting.
Key Results and Discussions
Main Findings
Remote laser cutting technology significantly enhances productivity. It minimizes heat-affected zones, thus preserving material integrity. This method enables precise cuts, regardless of material thickness. Companies leveraging remote laser cutting have reported notable reductions in operational costs due to decreased material usage and lower labor requirements.
Implications of Findings
The implications of the findings are particularly relevant for sectors seeking efficiency. With less waste generated in the cutting process, companies can meet environmental standards more readily. Additionally, the reduced need for secondary finishing processes typically required in traditional cutting can result in quicker turnaround times. Overall, the shift towards remote laser cutting signals a transformative change in manufacturing practices.
"Remote laser cutting technology not only enhances precision but also aligns well with sustainability objectives."
Understanding Remote Laser Cutting
Remote laser cutting has become a fundamental aspect of modern manufacturing. It utilizes high-precision lasers for cutting materials, offering distinct benefits over traditional methods. In this section, we delve into the definition, basic principles, and historical context of remote laser cutting technology, illuminating its relevance in various industrial applications.
Definition and Basic Principles
Remote laser cutting involves using a focused laser beam to cut through materials without direct contact. This technology operates by directing a laser beam through an optical system, ensuring precision and speed. The term "remote" indicates that the cutting process occurs at a distance from the laser source, enhancing flexibility and efficiency.
The basic principles of remote laser cutting are grounded in photonics. The laser beam's intensity and focus drive the cutting process, allowing the laser to melt or vaporize materials. This technique is capable of cutting different materials, such as metals, plastics, and composites, making it highly versatile. High-power laser types, such as fiber lasers, CO2 lasers, and disk lasers, contribute to the technology's effectiveness.
History of Laser Cutting Technologies
The evolution of laser cutting can be traced back to the early 1960s, when lasers were first invented. The first commercial use of lasers for cutting materials appeared in the 1970s. Over the decades, advancements in laser technology have significantly improved cutting capabilities.
Initially, laser cutting was limited to specific applications, mainly in research and development. As technology progressed, the introduction of higher power lasers and improved optical systems began to dominate the industry. By the late 1980s and early 1990s, remote laser cutting systems emerged, providing new opportunities for manufacturers.
Today, remote laser cutting plays a crucial role in industries such as aerospace, automotive, and electronics, thanks to its ability to deliver precise cuts with minimal secondary operations. Its history reflects a continual push for innovation, leading to enhanced capabilities and broadening its applications.
Laser cutting technology has revolutionized the way materials are processed, allowing for complex designs that were previously unattainable.
As we now shift focus to key components that underpin remote laser cutting systems, it is essential to understand how each element contributes to the overall efficiency and effectiveness of the cutting process.
Key Components of Remote Laser Cutting Systems
Remote laser cutting systems consist of several critical components that work in unison to achieve precise and efficient material processing. Understanding these elements is essential for anyone involved in the technology's application and development. These components include laser source types, optical delivery systems, and control systems and software. Each plays a pivotal role in determining the overall functionality, adaptability, and performance of the cutting process.
Laser Source Types
Laser cutting technology begins with the selection of the laser source. The choice of laser type directly influences the cutting capability, speed, and quality. Common laser types used include fiber lasers, CO2 lasers, and solid-state lasers.
- Fiber Lasers: These lasers are known for their high efficiency and excellent beam quality. They are often preferred in industries requiring precise cuts with minimal heat-affected zones.
- CO2 Lasers: Renowned for their versatility, CO2 lasers excel in cutting a wide range of materials, including plastics and wood. However, these lasers typically demand more power to achieve comparable performance to fiber lasers.
- Solid-State Lasers: These are less commonly used but can be effective for specific applications, offering certain advantages in terms of robustness and maintenance.
The impact of the laser source extends beyond cutting performance. It also influences energy consumption, operational costs, and the types of materials that can be effectively processed. An informed selection of the laser source is vital for achieving desired outcomes in various manufacturing scenarios.
Optical Delivery Systems
Once the laser source is established, an optical delivery system becomes crucial. This system directs the laser beam to the workpiece and determines the focus and quality of the beam during cutting operations. Optical systems generally comprise mirrors, lenses, and fiber optic cables.
- Mirrors: These are often used to redirect the laser beam efficiently within the system. The alignment and quality of mirrors can significantly affect the energy loss and overall effectiveness of the cutting process.
- Lenses: Focus lenses are utilized to concentrate the laser beam onto the material surface. Different lens configurations can change the spot size, impacting the cut quality and thickness capabilities.
- Fiber Optics: These enable flexible delivery of laser beams, allowing for more complex cutting paths and configurations. Fiber optics typically enhance the system's adaptability and ease of integration into various cutting setups.
Each component in the optical delivery system needs to be meticulously calibrated to ensure maximum performance. Proper maintenance and alignment are integral to sustaining high-quality cutting results over time.
Control Systems and Software
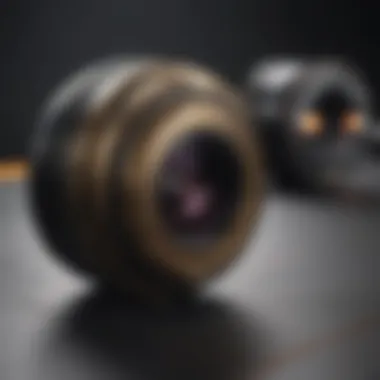
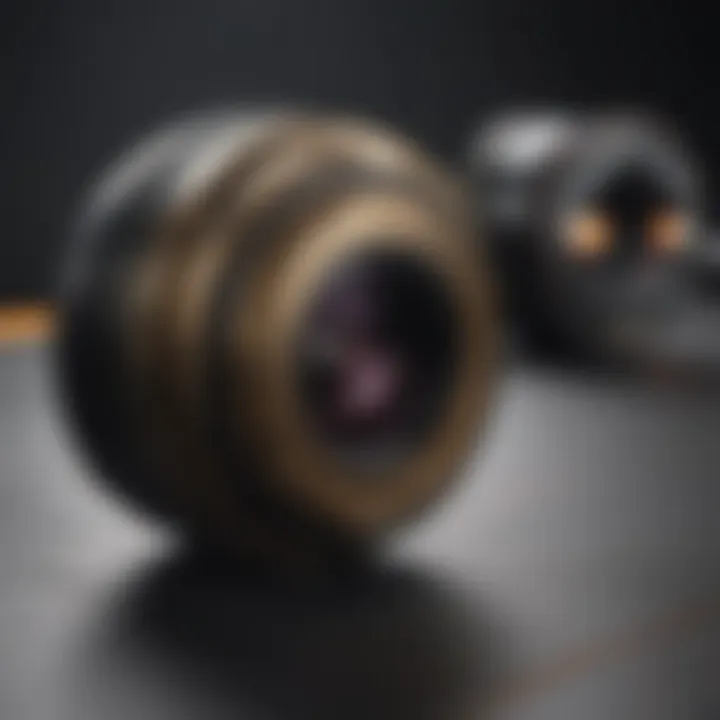
The final key component in a remote laser cutting system is its control system and software. These determine how the entire operation runs, orchestrating the interaction between hardware and maintaining precision.
Modern control systems leverage advanced programming to provide real-time monitoring and adaptive feedback mechanisms. Features often included are:
- User Interface: Intuitive designs allow operators to adjust settings easily, select cutting parameters, and monitor performance metrics.
- Path Planning Software: This enables optimal cutting sequences and minimizes waste. Advanced algorithms can analyze patterns, helping to reduce cycle times.
- Safety Lockouts and Protocols: Integrated safety measures are essential to protect equipment and personnel, ensuring operations are conducted within safe parameters.
The software serves as the brain of the operation and can significantly influence the speed, efficiency, and accuracy of cuts. Continuous advancements in software capabilities further enhance the potential of remote laser cutting systems.
"The success of a remote laser cutting system is not solely reliant on its individual components, but rather how well they integrate and function together."
In summary, understanding the key components of remote laser cutting systemsโlaser sources, optical delivery systems, and control systemsโis crucial for professionals. These elements combined create a robust, efficient, and versatile cutting solution suitable for a wide range of applications in various industries.
Operational Mechanism of Remote Laser Cutting
Understanding the operational mechanism of remote laser cutting is essential for grasping how this technology has become pivotal in various industries. This aspect encompasses the processes and principles that enable the cutting of materials with high precision using a focused laser beam. It is crucial to recognize the advantages such an approach brings over traditional methods. Generally, remote laser cutting enhances efficiency, quality, and adaptability in material processing.
Process Overview
The operational mechanism begins with the generation of a high-intensity laser beam. The laser source, which can be a fiber laser or a CO2 laser, emits a beam that is directed towards the material via optical delivery systems. This approach allows the beam to be manipulated and focused over considerable distances without significant loss of energy.
In the process, it is important to maintain optimal parameters such as power, speed, and focus for effective cutting. The system relies on numerical control and specialized software that ensure high accuracy in positioning the laser. The material to be cut is usually moved under the focused beam, allowing the laser to penetrate the surface and sever the material effectively. This method offers a clean cut with minimal heat-affected zones, reducing post-processing needs.
Material Interaction with Laser Beam
The interaction between the laser beam and the material is fundamental to the effectiveness of remote laser cutting. When the highly concentrated light strikes the material, several physical phenomena occur.
Thermal Effect: The laser induces heat, leading to thermal expansion. For metals, this can cause melting, while for polymers, vaporization often occurs. Different materials respond uniquely to laser energy, affecting cutting speed and precision.
Absorption and Reflection: Different materials also have varied absorption coefficients under laser light. For optimal cutting results, materials with a high absorption rate to the laser wavelength are preferred.
Kerf Formation: As the laser penetrates the material, it generates a kerf, which is the width of the cut. Factors such as the laser's focus, power, and the type of material will influence kerf width and quality.
In summary, the operational mechanism of remote laser cutting combines advanced technology with precise control systems to yield efficient, high-quality outcomes in material processing. It is a method tailored for industries seeking high precision and reduced operational costs.
Comparative Analysis with Traditional Cutting Methods
The comparative analysis of remote laser cutting with traditional cutting methods is a crucial topic in this context. Understanding the advantages and limitations of both approaches allows industries to make informed decisions in the selection of cutting technologies. Traditional methods, such as mechanical cutting or water jet cutting, have long been staples in manufacturing. Their methods, however, may not always meet the growing demands for precision, efficiency, and adaptability in todayโs fast-paced environment. Remote laser cutting offers several distinct benefits, which often make it a more appealing choice for various applications.
Efficiency and Precision
Remote laser cutting stands out in terms of efficiency and precision. The technology enables a higher cutting speed compared to traditional methods. The remote process involves using a focused laser beam that moves rapidly over the material, allowing for intricate designs and tight tolerances to be achieved. This cutting method minimizes the heat-affected zone, thus maintaining the integrity of the material.
Moreover, remote laser cutting systems can operate continuously with little downtime. They require less frequent maintenance compared to conventional cutting tools, where blade sharpening and replacing parts are regular tasks.
Rapid adjustments and programming capabilities mean that changes to designs can be implemented quickly, enhancing the overall workflow. This is particularly beneficial in industries where customization is key, such as in aerospace and medical device manufacturing.
Cost Considerations
When it comes to cost, the analysis must consider both initial investment and long-term operational costs. Remote laser cutting systems typically require a higher upfront investment, largely due to the advanced technology and equipment involved. However, the long-term savings can often offset this initial expense.
- Reduced Material Waste: Laser cutting is highly precise, which leads to less material wastage. With traditional methods, miscuts or errors can result in significant loss of material, leading to higher costs.
- Lower Energy Consumption: While the initial cost of the machinery might be high, remote laser cutting machines are often more energy-efficient in operation. This efficiency can result in lower utility bills over time.
- Labor Efficiency: The automation capabilities of laser cutting systems reduce the need for extensive manual labor, thus lowering labor costs in the long run.
In summary, while traditional cutting methods like mechanical cutting have their advantages, remote laser cutting presents a compelling case for industries seeking improved efficiency and long-term cost benefits.
"The choice between remote laser cutting and traditional methods can significantly affect operational efficiency and cost management."
Applications of Remote Laser Cutting
Remote laser cutting demonstrates significant promise across various industries. By leveraging advanced technology, companies enhance their production capabilities. The integration of remote laser cutting represents a pivotal shift in how materials are processed. This section examines the primary applications of this method, detailing its benefits and considerations.
Manufacturing Industry
In the manufacturing sector, remote laser cutting is celebrated for its ability to deliver precision and efficiency. Unlike traditional cutting methods, remote laser systems can process complex geometries without the need for physical contact with the material. This advantage not only minimizes wear and tear on tools but also reduces production downtime.
The use of remote lasers allows manufacturers to achieve faster cutting speeds while maintaining high-quality edges. Parts can be produced in a shorter timeframe, resulting in lower operational costs. Companies like Trumpf and Cincinnati Incorporated have incorporated this technology into their production lines, demonstrating increased throughput and reduced scrap rates.
"Remote laser cutting introduces a new dimension to manufacturing efficiency."
Aerospace and Automotive Sectors
The aerospace and automotive sectors benefit significantly from remote laser cutting due to the stringent quality standards required in these industries. Remote laser technology offers unparalleled accuracy, which is vital when working on components like engine parts or airframe structures. For example, remote laser cutting can produce lightweight yet robust components that meet the demanding specifications in these fields.
Additionally, the flexibility of remote laser systems allows for rapid prototyping. Engineers can quickly iterate designs, leading to faster development cycles. The aerospace company Boeing has explored remote laser cutting techniques to enhance production of aircraft parts, showcasing the benefits of rapid manufacturing without compromising precision.
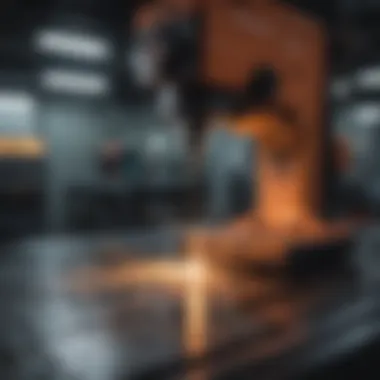
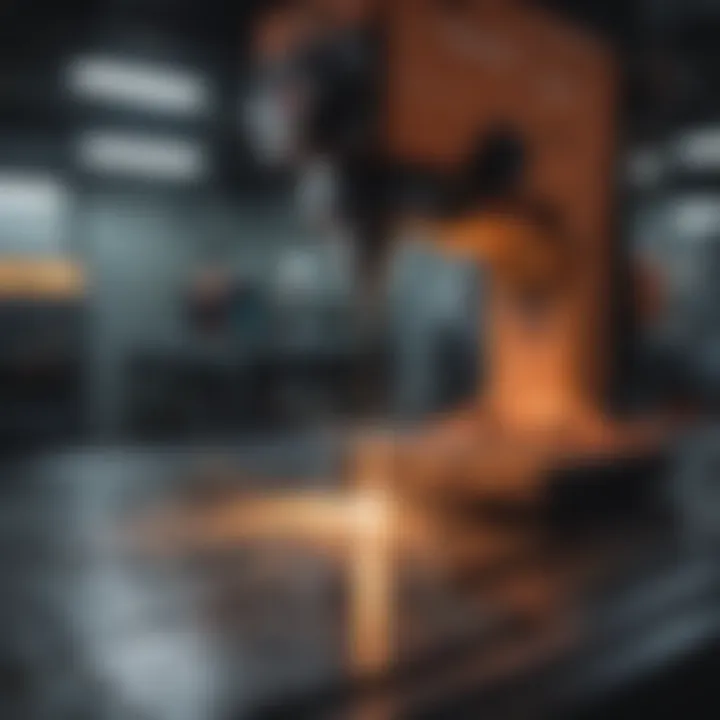
Medical Devices and Components
The medical devices industry prioritizes precision, especially when it comes to manufacturing implants and surgical instruments. Remote laser cutting fulfills these needs effectively, providing clean cuts and the ability to work with a variety of materials, including polymers and metals. The sterilization process of medical devices often starts with laser cutting, ensuring that contamination is minimized.
Remote laser cutting offers high repeatability in production, which is critical for maintaining the integrity of medical components. Manufacturers such as Medtronic have adopted this technology, recognizing its advantages in ensuring uniformity and compliance with health regulations.
Advantages of Remote Laser Cutting
The implementation of remote laser cutting technology offers several advantages that are crucial for modern manufacturing processes. Understanding these benefits can help industries leverage the innovation to enhance productivity and optimize resource utilization. The advantages include enhanced material processing and reduced waste and energy consumption, each contributing to the overall efficiency of the cutting process.
Enhanced Material Processing
Remote laser cutting technology improves the precision and speed of material processing. With the aid of focused laser beams, it can achieve intricate cuts with an accuracy that is often unattainable with traditional methods. This precise cutting capability translates to the ability to work with a variety of materials, including metals, plastics, and composites, without the need for extensive setup changes. The adaptability to various thicknesses and materials makes remote laser cutting particularly valuable in industries that require customized solutions.
Moreover, the heat-affected zone in remote laser cutting is minimized, preserving the integrity of surrounding material. This is especially important in applications like aerospace and electronics, where even minor distortions can compromise the functionality of components. Consequently, the enhanced material processing capabilities of remote laser cutting not only deliver superior quality but also reduce the necessity for post-processing operations, which can be time-consuming and costly.
Reduced Waste and Energy Consumption
Another significant advantage of remote laser cutting is its contribution to sustainability in manufacturing. Traditional cutting methods often generate excessive waste and require more energy due to the inefficiencies in cutting processes. In contrast, remote laser cutting is designed to minimize waste by providing cleaner cuts and maximizing material usage.
This technology also facilitates greater energy efficiency. The focused laser beam requires less energy compared to mechanical cutting methods, where motors and moving parts tend to consume more power. Combined with reduced heat generation, remote laser cutting helps in decreasing the overall carbon footprint of manufacturing operations. Companies are increasingly recognizing that adopting such technologies not only meets regulatory requirements but also appeals to environmentally conscious consumers.
The shift towards more sustainable manufacturing practices is a key driver of innovation in remote laser cutting technology.
Safety and Regulatory Considerations
Safety and regulatory considerations are essential in the domain of remote laser cutting. As the technology advances, the complexity and risks associated with its operation increase. Ensuring a high standard of safety practices not only protects operators but also enhances the overall efficiency of the cutting process. Regulatory compliance is also necessary for maintaining industry standards and avoiding potential legal issues.
In this section, we will focus on two critical aspects of safety and regulatory considerations in remote laser cutting: operational safety protocols and compliance with industry standards.
Operational Safety Protocols
Operational safety protocols form the backbone of a successful remote laser cutting operation. These protocols are designed to mitigate risks and ensure that the work environment is safe for all employees involved in the process. Some important elements of operational safety include:
- Training and Certification: Proper training programs for all operators are essential. This includes understanding the machine functions, emergency procedures, and the health impacts of laser exposure.
- Protective Equipment: Operators should wear appropriate personal protective equipment (PPE), including safety goggles designed to shield against laser light, gloves, and other necessary gear.
- Establishing Safety Zones: Clearly defined safety zones around the cutting area help to ensure only authorized personnel are present during operation.
- Emergency Protocols: Incase of accidents or equipment failures, clear emergency procedures must be established. Regular drills can enhance preparedness among all employees.
Regular audits and reviews of these protocols should be conducted to adapt and improve them as technology and workplaces evolve. By adhering to these guidelines, companies can reduce the risk of accidents and enhance the safety of the operational environment.
Compliance with Industry Standards
Compliance with industry standards is vital in maintaining credibility and ensuring that remote laser cutting operations are safe and effective. Organizations must adhere to various regulations set by authorities. This includes:
- ANSI Standards: The American National Standards Institute sets safety standards specific to laser operations. Compliance with these standards ensures that companies implement best practices and suitable engineering controls.
- ISO Certifications: The International Organization for Standardization publishes guidelines that help maintain quality and safety in industrial practices. Achieving ISO certification can enhance a company's reputation in the marketplace.
- Local Regulations: Depending on the region, local regulations might impose specific requirements regarding the use of lasers in manufacturing processes. Companies must be aware of and comply with these rules to avoid penalties.
Maintaining compliance not only helps in building a company's reputation but also safeguards employees and the surrounding environment. In the rapidly changing landscape of technology, staying informed on both operational safety protocols and industry regulations is crucial for successful remote laser cutting operations.
Challenges and Limitations
When discussing remote laser cutting, it is vital to examine the associated challenges and limitations. Understanding these aspects can provide clarity on the efficiency and utility of this technology in modern applications. Despite its advancements, remote laser cutting faces several hurdles that can hinder its widespread adoption and effectiveness.
Material Limitations
One primary challenge in remote laser cutting pertains to material limitations. Not all materials are suitable for laser cutting, and this can restrict its applicability. While metals such as steel and aluminum respond well to laser technology, materials like certain plastics, composites, and reflective metals can present significant obstacles. For instance, reflective materials like copper can disrupt the cutting process, often leading to reduced efficiency or even damage to the laser source.
Moreover, some materials may require specific wavelength lasers for effective cutting, resulting in added costs and complexity. This is particularly important in high-precision applications where the type of material directly influences the laser's performance.
To summarize, the types of materials that can be cut using remote laser technology influence the technology's versatility and overall utility.
Technological Barriers
Technology itself can also pose barriers to the effectiveness of remote laser cutting. First, the initial investment for a high-quality remote laser cutting system can be prohibitively high for many businesses, especially smaller enterprises. This creates an entry barrier that may deter potential users from adopting the technology, thus slowing down its growth in various sectors.
Furthermore, the complexity of remote laser cutting systems requires specialized training. Operators need to be well-versed not only in operating the machinery but also in troubleshooting potential issues that might arise during the cutting process. This demand for skilled personnel can be a limiting factor for companies looking to maximize their benefits from this technology.
Additionally, maintenance and repair of high-tech laser equipment can be costly and require significant downtime. Continuous advancements in technology may lead to obsolescence of components, further necessitating costly upgrades to keep pace.
In summary, while remote laser cutting holds great promise, the material limitations and technological barriers can significantly hinder its universal application. These challenges require careful consideration by businesses contemplating the transition to this cutting-edge technology.
"A comprehensive understanding of these limitations is essential for industries aiming to leverage remote laser cutting effectively."
Overall, addressing these challenges is crucial for enhancing the efficiency and effectiveness of remote laser cutting. This understanding paves the way for potential solutions that can bridge the gaps and propel the technology forward.
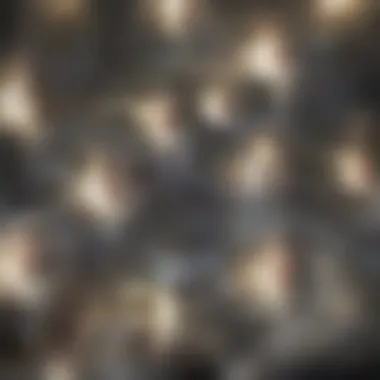
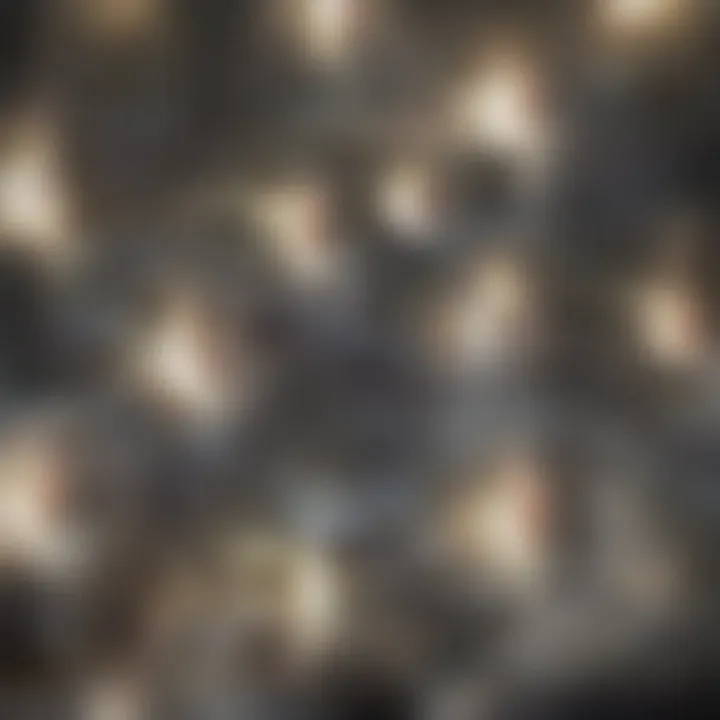
Economic Impact of Remote Laser Cutting
The economic impact of remote laser cutting is profound, shaping new paradigms in manufacturing and production efficiency. This technology not only enhances operational capabilities but also creates significant economic benefits. Understanding its impact helps industries evaluate adoption, foster innovation, and remain competitive in a rapidly evolving marketplace.
Cost-Benefit Analysis
A cost-benefit analysis is crucial in assessing the adoption of remote laser cutting technology. Organizations must examine various factors under this analysis.
- Initial Investment: The upfront cost of acquiring laser cutting equipment can be high. Companies must consider the expense of the laser source, delivery systems, and accessories.
- Operational Costs: While initial investments are considerable, ongoing expenses may be lower compared to traditional cutting methods. Remote laser cutting can result in reduced energy consumption and lower material wastage, leading to ongoing cost savings.
- Labor Savings: Many industries face labor shortages. Remote laser cutting systems can often be automated, reducing the need for specialized skilled labor. This automation presents labor cost savings and helps mitigate the effects of labor shortages.
- Material Utilization: One of the significant benefits lies in material efficiency. Remote laser cutting typically yields less scrap than other cutting technologies, enhancing overall resource utilization and reducing material costs.
- Long-Term Value: Over time, increases in productivity and reductions in turnaround times can substantially outweigh initial investments. This enhanced efficiency can positively influence pricing strategies and market competitiveness.
Ultimately, the key question remains: Is the investment worth the benefits? By quantifying these impacts, organizations can make informed decisions reflecting their long-term goals and financial health.
Return on Investment Considerations
Return on Investment (ROI) in remote laser cutting involves analyzing the financial returns generated from this technology relative to its costs. A few key considerations include:
- Short-Term Gains: Companies might observe quicker production rates immediately after tech adoption. Quicker production can translate directly to increased revenues.
- Production Scalability: Companies can expand production capabilities without significant added costs. This scalability promotes growth and pushes a company's bottom line higher.
- Market Adaptability: Being agile in responding to market demands can attract new customers and retain existing ones. Improved turnaround times enhance customer satisfaction and loyalty.
- Maintenance Costs: Evaluating maintenance expenses helps determine ongoing costs associated with remote laser cutting systems. While initial investments are vital, understanding maintenance can improve budget forecasts.
- Risk Mitigation: As remote laser cutting becomes more common, businesses adopting this technology may benefit from reduced risks associated with operating older, less efficient systems. Avoiding technology obsolescence can preserve market share and bolster profitability.
Environmental Considerations
The growing emphasis on environmental sustainability within manufacturing processes necessitates a thorough exploration of the Environmental Considerations relevant to remote laser cutting technology. This section elucidates the imperative nature of integrating sustainability into modern manufacturing practices. The need to reduce carbon footprints and enhance resource efficiency aligns closely with current global goals aimed at maintaining ecological balance. Therefore, understanding the environmental impacts of remote laser cutting becomes crucial for companies aiming to adopt greener technologies.
Sustainability in Manufacturing
Sustainability in manufacturing is increasingly recognized as a core business strategy. Remote laser cutting contributes to this sustainability push in several key ways. First, the technology minimizes waste through precise cutting techniques that require less material, thus cutting down on scrap rates. By optimizing material usage, manufacturers can effectively lower the cost of raw materials and reduce the burden on landfills.
Moreover, the energy efficiency of remote laser cutting processes serves as another pillar of sustainability. Compared to traditional cutting methods, remote laser systems are designed to utilize energy more effectively. This efficiency not only lessens energy consumption during operations but also reduces greenhouse gas emissions. With stricter regulations on emissions, manufacturers engaged in remote laser cutting can position themselves as eco-conscious, appealing to a market that increasingly values environmental responsibility.
Waste Reduction Strategies
Addressing waste reduction is central to implementing remote laser cutting in a sustainable manner. The precision of the technology allows for tighter tolerances during cutting, which directly contributes to less material waste. Unused materials can be recycled or repurposed, enhancing the overall sustainability profile of operations.
Some effective waste reduction strategies associated with remote laser cutting include:
- Integrating Design for Manufacturing (DFM): Utilizing software that enables designers to create parts that are optimized for laser cutting can help in further reducing waste during production.
- Establishing a Circular Economy: Encouraging the recycling of cut materials and investing in systems that allow for reclaimed resources to re-enter the production chain.
- Monitoring and Analytics: Implementing real-time monitoring systems can provide insights into material usage and waste generation. This data enables companies to refine their processes continuously, enhancing efficiency and reducing waste over time.
"The embrace of sustainability in manufacturing signifies not just compliance with regulations but a profound commitment to future generations." - Industry Analyst
Future Trends in Remote Laser Cutting
The landscape of remote laser cutting technology is continuously evolving. As industries adopt advanced manufacturing techniques, it becomes essential to explore the future trends within this field. Understanding these trends allows businesses and researchers to prepare and adapt to the shifting demands in productivity, efficiency, and environmental responsibility.
Advancements in Laser Technology
Recent years have seen a significant advancement in laser technology. Developments in laser sources, particularly fiber, fiber beam, and multi-kilowatt lasers, enhance cutting precision and speed. Fiber lasers, in particular, are notable because they offer improved efficiency and reduced operational costs. This shift indicates a move towards compact and powerful systems that can handle various materials with less energy.
Moreover, the shift to high-power lasers means that thicker materials can be cut more effectively. As technology progresses, these lasers are expected to incorporate more sophisticated software for greater control during operations. This will enable more complex cuts and shapes with minimal operator intervention.
Another area of advancement is the integration of adaptive optics. This tech enables real-time adjustments to focus the laser beam on different material surface qualities, which enhances cutting accuracy. Furthermore, the continuous development of ultrafast lasers allows for even thinner kerfs and less thermal impact on adjacent materials.
Integration with Industry 4.
The integration of remote laser cutting with Industry 4.0 marks another substantial trend in the sector. This concept revolves around the digitization of manufacturing, creating smart factories that leverage data for enhanced operational efficiency.
The Internet of Things (IoT) plays a crucial role here. By embedding sensors within laser cutting machinery, manufacturers can collect real-time data on equipment performance and material behavior. This data can be analyzed to predict maintenance needs, reducing downtime and optimizing production schedules.
Furthermore, with the rising trends of automation and artificial intelligence, operators can expect increasingly autonomous remote laser cutting solutions. These systems can learn from previous operations to make adjustments that improve cutting quality and speed.
Incorporating cloud-based solutions also permits remote monitoring of operations. Users can manage and analyze production metrics from any location, providing unprecedented flexibility and control.
"Remote laser cutting technology is meeting the demands of tomorrow by integrating with smart manufacturing processes."
Concluding Thoughts
Remote laser cutting is emerging as a vital technology in modern manufacturing. Its significance stems from several pivotal elements that enhance industrial processes. This section will articulate the importance of these aspects and synthesize how they contribute to the broader context of manufacturing advancements.
Summary of Key Points
The exploration of remote laser cutting technology reveals several key points:
- Enhanced Precision: The technology allows for accurate cuts with minimal material wastage, which directly impacts operational efficiency and product quality.
- Versatility in Applications: From aerospace to medical devices, the range of materials and industries benefiting from this technology continues to grow, demonstrating its flexibility and appeal.
- Safety and Compliance: Ensuring safety standards are met is paramount. Remote laser cutting minimizes risks associated with traditional cutting methods, enhancing protection for operators.
- Economic Viability: An effective cost-benefit analysis shows that the initial investment can lead to significant savings over time, making it an attractive option for many businesses.
- Environmental Benefits: The process contributes to sustainability in manufacturing by reducing waste and energy consumption.
"The integration of remote laser cutting in various sectors signals a shift towards smarter, more efficient technologies in manufacturing."
Final Reflections on Remote Laser Cutting
Reflecting on remote laser cutting provides insight into its evolving role in manufacturing. As industries face growing demands for precision and efficiency, remote laser cutting emerges as a substantial solution. Its ability to adapt with advancements in technology, including Industry 4.0 integration, positions it favorably for the future.
Moreover, the ongoing research and development in laser technology can further enhance its capabilities. Staying updated with these trends is essential for industry stakeholders who aim to remain competitive.