Laminated Object Manufacturing in 3D Printing
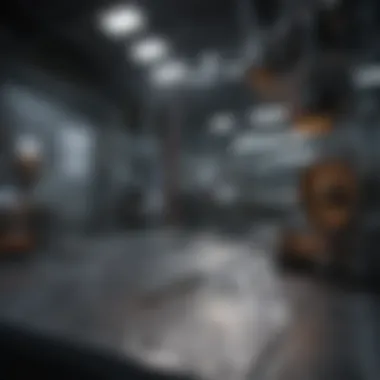
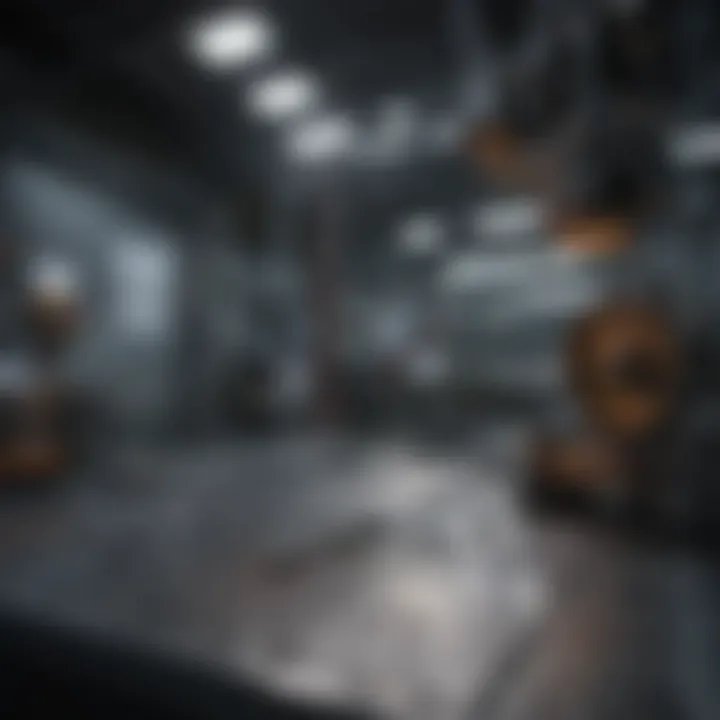
Article Overview
Summary of Key Findings
Laminated Object Manufacturing (LOM) stands out in the realm of 3D printing because of its unique approach to building objects layer by layer. The fundamental mechanism involves the layering of adhesive-coated sheets, which are progressively cut and bonded to create a final product. This method contrasts with other 3D printing techniques, like Fused Deposition Modeling (FDM) and Selective Laser Sintering (SLS), which use different materials and methods to form objects.
The primary materials used in LOM include paper, plastic, metal, and ceramic sheets. These materials easily integrate into several applications, providing versatility across industries such as automotive, aerospace, and education. The most significant advantage of LOM is its ability to produce large-scale prototypes efficiently. Moreover, the accessibility of inexpensive materials lowers costs, making it ideal for both educational purposes and small-scale manufacturing.
Research Objectives
The purpose of this analysis is to thoroughly explore the mechanisms and applications of LOM within the larger context of 3D printing technologies. By identifying the advantages and potential limitations, the research aims to shed light on how this method fits into modern manufacturing practices. Aimed at researchers and professionals, this article seeks to enhance understanding of LOM's capabilities, its place in industry evolution, and future prospects.
Key Results and Discussions
Main Findings
The findings indicate that LOM is particularly advantageous for the rapid prototyping of functional parts. Compared to traditional methods, LOM is less time-consuming and can produce detailed designs without extensive machinery. The integration of various materials adds to its potential, enabling customization and innovation in product development. The technology also allows for the use of sustainable materials, addressing increasing environmental concerns in manufacturing.
Implications of Findings
The implications of these findings are significant, particularly for industries looking to optimize production processes. The ability to create prototypes quickly reduces time-to-market, allotting companies greater flexibility. LOM's cost-effectiveness encourages wider adoption, potentially reshaping how products are conceptualized and developed. Given its scalable nature, small businesses and educational institutions particularly benefit from this technology, facilitating hands-on learning and experimentation.
"Laminated Object Manufacturing presents a unique fusion of efficiency and versatility, making it an important player in the 3D printing landscape."
To summarize, LOM has established itself as a valuable technology in 3D printing. Understanding its mechanisms, materials, and applications provides a comprehensive view of its potential and positions it as a significant tool for future manufacturing advancements.
Prelude to Laminated Object Manufacturing
Laminated Object Manufacturing (LOM) is an intriguing facet of 3D printing technology that holds significant value in various manufacturing processes. The importance of LOM arises not only from its distinct method of creating three-dimensional objects but also from its advantages in terms of cost, speed, and flexibility. By understanding the mechanisms behind LOM, one can appreciate its role in modern manufacturing landscapes.
Overview of 3D Printing Technologies
3D printing encompasses a variety of technologies aimed at generating objects layer by layer from digital models. Each method utilizes specific techniques and materials to achieve desired outcomes. Notable 3D printing technologies include:
- Fused Deposition Modeling (FDM): This technique melts a thermoplastic filament and extrudes it through a nozzle, building up layers in the process.
- Stereolithography (SLA): Involves curing liquid resin with ultraviolet light to form solid structures.
- Selective Laser Sintering (SLS): Uses lasers to fuse powdered materials together, creating durable parts.
Understanding these technologies provides a broader context for comparing LOM with other methods.
Defining Laminated Object Manufacturing
Laminated Object Manufacturing is defined as a layer-based additive manufacturing method that constructs a part by stacking layers of adhesive-coated paper, plastic, or metal sheets. Each sheet is cut to shape using a laser cutter before being bonded together through heat and pressure. The process involves several key steps:
- Layer Preparation: The sheets are cut to precise dimensions as per the CAD model.
- Layer Bonding: Layers are bonded together using a combination of heating and pressing.
- Finishing: After layering, the object may undergo further finishing processes, such as sanding or coating, to enhance appearance and properties.
LOM's ability to produce components quickly and efficiently makes it suitable for prototypes and end-use parts, particularly in fields like engineering and manufacturing.
"Laminated Object Manufacturing offers unique benefits that align closely with the needs of rapid prototyping and low-volume production."
In summary, the introduction of Laminated Object Manufacturing in this article aims to clarify its importance within the broader context of 3D printing technologies. The distinction of this method highlights its practical applications and design flexibility, setting the stage for a more in-depth examination of its mechanisms and advantages.
Historical Context of Liquid Object Manufacturing
The development of Laminated Object Manufacturing (LOM) is not just a story of technological advancement; it is a reflection of broader trends in manufacturing and design. Understanding the historical context is crucial for grasping how LOM evolved and its relevance in modern applications. The origins of tools and systems in 3D printing fed into the rise of LOM, marking a paradigm shift in production methodologies.
Origins of Reality Printing
Reality printing has its roots in the exploration of layering processes. The late 20th century saw a surge in computer technologies, which spurred interest in new possibilities for material manipulation. The initial forays into 3D printing included Stereolithography and Fused Deposition Modeling. These early technologies opened the door for Laminated Object Manufacturing to develop as a unique method.
The concept of layering materials can be traced back to the 1980s. During this time, researchers explored how to create solid objects from digital designs by adding materials layer by layer. This was groundbreaking. The early experiments laid critical groundwork, allowing the eventual adoption of LOM as a viable choice for both prototyping and production.
Evolution of LOM Technology
The evolution of LOM technology parallels the advancements in computer-aided design (CAD) and manufacturing. Initially developed in the early 1990s, LOM began gaining traction with industries focused on rapid prototyping. The method utilizes thin layers of material, which are bonded together using heat and pressure. Over time, several key improvements contributed to its progress:
- Material Diversity: The types of laminates used expanded beyond paper. Today, options include plastics and composites, increasing LOM's versatility.
- Precision Improvements: Early implementations faced challenges regarding accuracy. Advances in software and machinery have increased the precision of layered assemblies.
- Increased Speed: Initial methods were relatively slow. Today’s LOM printers can produce parts faster than their predecessors, answering the demands of competitive markets.
In the past decade, LOM has seen increased interest due to its ability to produce larger parts while maintaining relatively low costs. The continual refinement of technologies means LOM could be integral in new manufacturing ecosystems. As industries evolve, LOM’s historical roots and changes illustrate the ongoing quest for efficient and effective production methods.
"Understanding the historical progression of 3D printing technologies is vital for appreciating the capabilities and limitations of Laminated Object Manufacturing today."
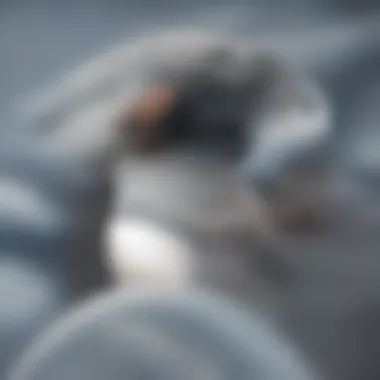
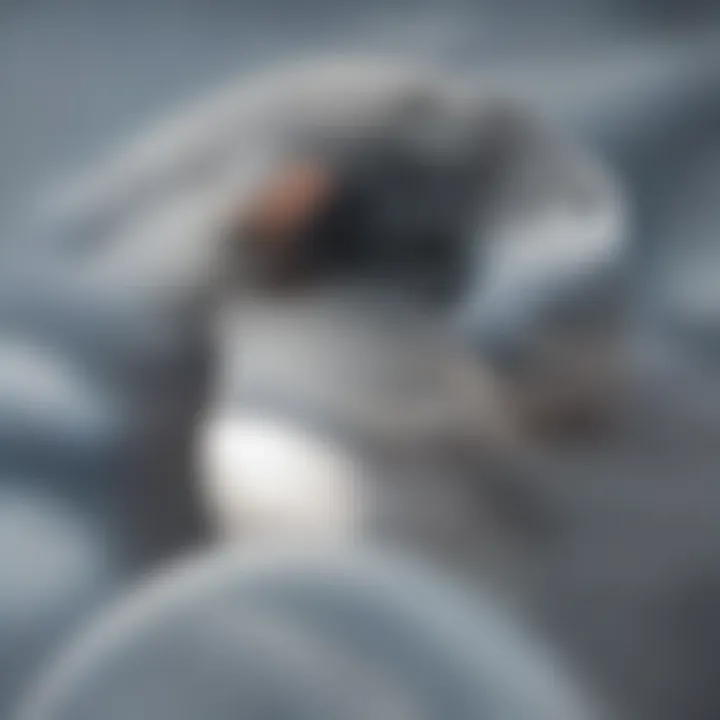
In summary, Laminated Object Manufacturing has roots deeply embedded in the evolution of 3D printing technology. Understanding its origins helps clarify the unique attributes of this method. As LOM continues to evolve, its historical significance remains a guiding force in its applications and advancements.
Mechanisms of Laminated Object Manufacturing
The mechanisms of Laminated Object Manufacturing (LOM) are central to understanding how this additive manufacturing technique operates. LOM stands out due to its unique approach of layering materials such as paper, plastic, or metal. This section examines the core principles, layering techniques, and binding methods utilized in LOM. Comprehending these mechanisms is crucial because they directly influence the quality, efficiency, and cost-effectiveness of the production process.
Core Principles of LOM
The core principle of Laminated Object Manufacturing is quite straightforward. LOM begins with the accumulation of thin layers of material, which are then combined to create a three-dimensional object. Each layer is bonded to the previous one using heat and pressure, or adhesives. Unlike other 3D printing methods, LOM does not rely on melting or sintering.
The significant aspect of LOM is its ability to produce parts quickly and inexpensively. The process typically involves the following steps:
- Slicing of the CAD model into thin layers.
- Layer positioning on a build platform.
- Application of heat or adhesives to bond layers together.
- Removal of unneeded material once bonding is complete.
This sequence contributes to LOM's cost-effectiveness, making it a preferred option in various industries.
Layering Techniques in LOM
Layering is fundamental in LOM, allowing for optimal use of raw materials. The most common layering technique used is the addition of sheets or rolls of laminates. These sheets are cut precisely in accordance with the sliced CAD files. This technique ensures minimal waste as the excess material can often be reused or recycled. Each layer is typically between 100 to 500 micrometers in thickness, depending on the desired resolution and material used.
Another notable method is the use of non-destructive processes to support complex geometries. This reduces the need for additional support structures, which is common in other 3D printing processes. The quality of the finished product can also be influenced by the choice of laminate materials; some offer better adhesion properties, while others may provide enhanced surface finishes.
Binding Methods Utilized
Binding is a crucial aspect of Laminated Object Manufacturing, determining the strength and durability of the finalized object. The two primary methods include thermal bonding and adhesive bonding.
- Thermal Bonding: This involves heating the layers slightly before bonding them. The heat melts a small amount of the laminate material, causing it to fuse with the subsequent layer when pressure is applied. This creates a strong bond, essential for maintaining structural integrity.
- Adhesive Bonding: In this method, specific adhesives are applied between the layers. This can allow for greater flexibility in material choice, making LOM versatile for various applications. However, the effectiveness of adhesive bonding is heavily dependent on the type of adhesive used and the environmental conditions.
The choice of binding method can influence the mechanical properties of the final product, including its tensile strength and thermal stability.
"Understanding the mechanisms behind Laminated Object Manufacturing not only aids in the choice of materials and techniques but also offers insight into optimizing production processes for specific applications."
In summary, the mechanisms of Laminated Object Manufacturing emphasize the significance of layering and binding. Grasping these mechanisms is essential for engineers and researchers seeking to innovate in the domain of additive manufacturing.
Materials Used in Laminated Object Manufacturing
Understanding the materials used in Laminated Object Manufacturing (LOM) is crucial for grasping its advantages and potential applications. The choice of materials can significantly influence not just the quality of the final product but also the efficiency of the manufacturing process itself. In LOM, materials primarily take the form of laminates, which are layers that can be cut and stacked to create three-dimensional structures. This process allows for flexibility in design and functionality.
The benefits of selecting appropriate materials are manifold. First, they can impact the mechanical strength of the finished object. Some materials lend themselves to better durability and resistance to stress, making them ideal for engineering applications. Additionally, certain laminates can be easily manipulated, promoting faster production times and reducing waste. Lastly, the availability of different materials allows for customization, enabling manufacturers to tailor products for specific industries.
Types of Laminates Available
Laminated Object Manufacturing utilizes a variety of laminate materials. Each type has unique properties that can suit different applications. Common types of laminates include:
- Paper-Based Laminates: Often used for prototype creations due to low cost and ease of handling. They provide a reasonable balance between strength and flexibility.
- Plastic Laminates: These materials, like polyvinyl chloride (PVC) or polystyrene, offer better durability and can be used in more functional applications.
- Metal Laminates: Suitable for applications where strength and heat resistance are critical. Metal composites can be combined with other materials to enhance performance.
Other specialized composites exist as well, which can incorporate features such as electrical conductivity or thermal resistance. The choice among these types often depends on the intended use and environmental considerations.
Comparative Analysis of Material Properties
When considering materials for LOM, it's essential to evaluate their properties in relation to one another. Each material type brings distinct characteristics:
- Strength and Durability: Metal laminates outstrip paper and most plastics in terms of tensile strength. They are well-suited for structural components.
- Cost Efficiency: Paper laminates are among the most cost-effective choices, making them ideal for rapid prototyping and low-budget projects.
- Thermal and Electrical Properties: Plastics may not tolerate high temperatures well compared to metals but could be suitable where thermal insulation is a factor.
The choice of material ultimately impacts both performance during usage and the expense of production.
"Selecting the right materials in Laminated Object Manufacturing can mean the difference between a successful product and a failed prototype."
In summary, the careful consideration of material types in Laminated Object Manufacturing not only supports the structural integrity and functional requirements of the final product but also enhances efficiency and cost-effectiveness throughout the manufacturing process.
Comparison of Laminated Object Manufacturing with Other 3D Printing Techniques
Laminated Object Manufacturing (LOM) is one of many 3D printing techniques available today. Understanding how it compares to other methods provides valuable insights into its strengths and weaknesses. This section examines the most popular 3D printing techniques relative to LOM. Key elements to consider include material usage, production speed, cost, and overall application scope. Each comparison highlights the unique attributes of LOM and a clearer understanding of its position within the 3D printing landscape.
LOM vs. Fused Deposition Modeling
Fused Deposition Modeling (FDM) is a technique that creates objects by extruding melted thermoplastic filament through a heated nozzle, layer by layer. This method is known for its simplicity and affordability. While both LOM and FDM use layer-by-layer construction, they differ in processes and materials. LOM utilizes sheets of material that are adhered together, while FDM relies on melted filament.
Key Differences:
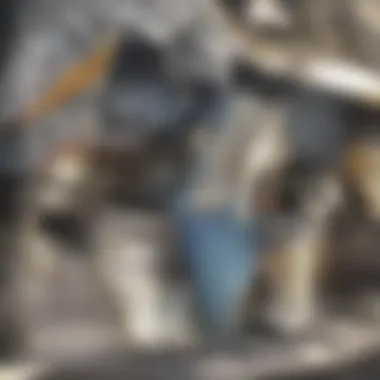
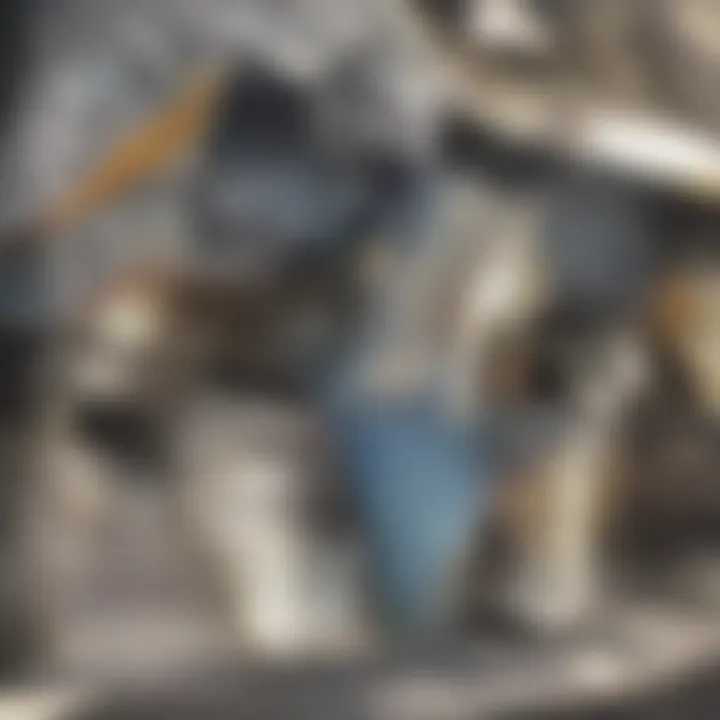
- Material Variety: LOM can work with a wider range of sheets, including paper, plastic, and metal. In contrast, FDM is limited mainly to thermoplastics like PLA and ABS.
- Production Speed: Generally, LOM can provide faster production times than FDM, especially for larger parts. The sheet-based method can be more efficient in terms of material consumption and layering.
LOM vs. Stereolithography
Stereolithography (SLA) employs a laser to cure liquid resin into hardened plastic. This method yields high precision and excellent surface finish, making it suitable for detailed prototypes. However, LOM presents advantages in terms of material costs and the range of materials compatible.
Key Differences:
- Surface Finish: SLA prints often have a superior surface finish compared to LOM, which may require additional post-processing.
- Material Costs: LOM can have lower material costs and less waste due to its layering process. SLA uses expensive resins, which can raise the overall cost of production.
LOM vs. Selective Laser Sintering
Selective Laser Sintering (SLS) functions by using a laser to fuse powdered material into solid parts. While SLS is known for its capability to create complex geometries, it requires significant equipment investment and can be slower for larger builds.
Key Differences:
- Complexity of Designs: SLS can produce more complex designs compared to LOM, which might struggle with intricate details due to its layering technique.
- Material Scope: While LOM’s sheet materials are diverse, SLS can work with various powders, including metals and polymers, providing a broader material application potential.
Closure of Comparison
The comparison of Laminated Object Manufacturing with other 3D printing methods reveals both strengths and weaknesses. Each method has its unique applications. LOM's advantages in speed and cost-efficiency make it a compelling choice for certain sectors, while FDM, SLA, and SLS each have their specific advantages depending on the required outcome. Understanding these differences is vital for industries considering the optimal technology for their needs.
Advantages of Laminated Object Manufacturing
Laminated Object Manufacturing (LOM) presents several advantages that make it a compelling choice for various applications in 3D printing technology. Its unique mechanisms and material utilization provide benefits that cannot be easily overlooked. Understanding these advantages is essential for researchers and professionals who are looking to leverage LOM in their respective fields.
Cost Effectiveness
One of the most significant advantages of LOM is its cost-effectiveness. The process primarily utilizes inexpensive materials like paper, plastic, or metal laminates, which are readily available. This affordability makes it possible to produce complex geometries at a fraction of the cost compared to other 3D printing techniques such as Stereolithography or Selective Laser Sintering. Additionally, the method generates minimal waste, meaning companies can further reduce their overall production costs. The lower expenditure on materials, coupled with a reduction in waste, enhances the economic viability of projects and prototypes developed through LOM.
Speed of Production
Another important aspect of LOM is its speed of production. The layering method allows for rapid fabrication of objects, which is especially beneficial in fast-paced industries like engineering and automotive sectors. Rather than waiting on slow curing processes, the layers are bonded together quickly, resulting in shorter turnaround times. The efficiency associated with LOM enables teams to iterate on designs or test new concepts with remarkable swiftness. In industries where time is often equated to profit, this aspect of LOM cannot be understated.
Quality and Precision
Quality and precision are critical considerations in manufacturing, and LOM delivers on both fronts. The process allows for intricate designs and fine details that achieve a high level of accuracy. Using high-resolution printers ensures that each layer aligns perfectly, which is crucial for parts requiring tight tolerances. Additionally, LOM creates parts that, once finished, are structurally sound and can be further processed or finished, addding to their practical applications. This level of precision meets the high standards of industries like aerospace or medical device manufacturing, where even minor deviations can lead to significant failures.
"Cost-effectiveness, speed and quality make LOM a competitive choice for 3D manufacturing applications across various sectors."
Applications of Laminated Object Manufacturing
Laminated Object Manufacturing (LOM) has a distinct role in the realm of 3D printing, serving diverse industries. Understanding its applications provides insight into its strengths and potential. The pressing need for rapid prototyping, customization, and efficient production processes highlights the relevance of LOM. By integrating various layers during the fabrication process, industries can achieve intricate designs and specifications that meet their specific requirements.
Prototyping in Engineering and Design
Prototyping is one of the most notable applications of LOM. In the engineering sector, professionals use LOM to create models that mimic the attributes of final products. This process allows for testing and validation before full-scale production. The technique's ability to build intricate prototypes efficiently leads to reduced time in product development cycles. Additionally, LOM supports the creation of functional prototypes, meaning early-phase testing can include actual performance assessments.
Advantages of using LOM for prototyping include:
- Cost-effectiveness: Producing prototypes with LOM is generally cheaper due to less material waste.
- Speed: The layering technique allows for quicker assembly of models compared to conventional methods.
- Precision: High levels of accuracy can be achieved, which is crucial for engineering applications.
LOM is especially useful in designing parts that require complex geometries, particularly in fields like automotive and aerospace engineering.
Medical Devices and Customization
The medical sector reaps substantial benefits from LOM technology. The ability to customize medical devices significantly improves patient care and outcomes. For example, LOM can produce patient-specific molds and models for surgical planning. Surgeons can work with more accurate replicas of a patient’s anatomy, leading to more precise interventions.
Customization in medical devices through LOM also means that smaller production runs are possible without incurring high upfront costs. This ability opens doors for personalized medical solutions that cater to individual patient needs, enhancing the overall effectiveness of treatments.
Notable applications in medical devices include:
- Custom orthopedic implants
- Prosthetic limbs
- Surgical instruments designed with patients in mind
The enhancements in medical practices underscore LOM’s potential for future integration in this sector.
Aerospace and Automotive Industries
The aerospace and automotive industries are major beneficiaries of Laminated Object Manufacturing applications. With stringent regulations and high-performance requirements, these sectors need manufacturing processes that lead to lightweight yet strong components. LOM meets this demand efficiently.
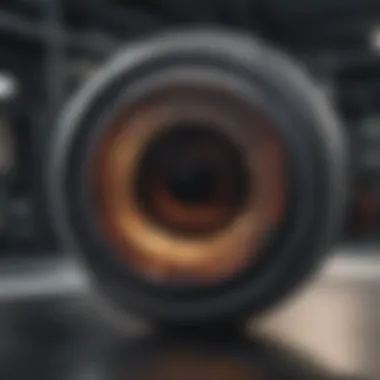
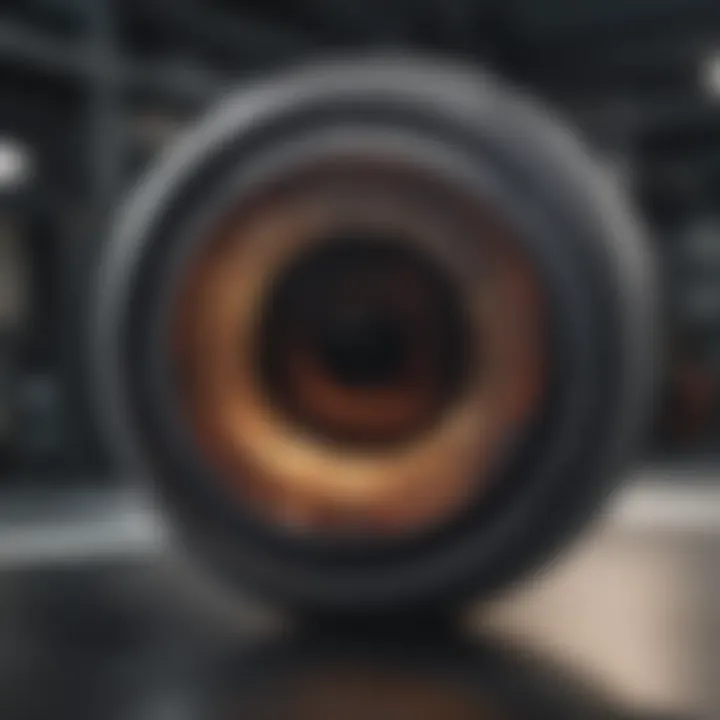
In aerospace, LOM aids in the production of parts for aircraft, where weight considerations are critically important. By effectively utilizing composite materials, manufacturers can create robust components that also minimize weight. This approach contributes to fuel efficiency and overall performance.
For the automotive industry, LOM supports rapid tooling and the provision of prototypes that reflect real-world applications. Companies can test designs, enhance their products, and accelerate market entry without towering costs associated with traditional methods.
Key advantages include:
- Material Efficiency: Less waste in the production process, promoting sustainability.
- Flexibility in Design: LOM allows for modifications in designs without starting from scratch.
- Speed in Production: Quicker turnaround times for highly specialized parts.
It's clear that LOM is positioned favorably within high-demand sectors, indicating its potential for ongoing development and adoption.
Challenges and Limitations of Laminated Object Manufacturing
Laminated Object Manufacturing (LOM) holds promise within the 3D printing landscape, yet it is not devoid of challenges. Understanding these limitations is crucial for researchers and practitioners. Identifying the barriers can lead to potential advancements or alternative approaches in manufacturing technology. Efforts to address these challenges could improve LOM’s competitiveness in various applications.
Material Limitations
One of the significant challenges in LOM is the limitations concerning available materials. The technology predominantly relies on laminates, typically paper or plastic sheets, which may restrict versatility. Although there are innovations in using different types of sheets, such as metal or ceramic, these materials are not widely adopted. This can limit applications in sectors that require specific material properties, such as high strength or thermal resistance.
Furthermore, variations in material thickness can affect production quality. A lack of consistency may result in defects, affecting the final product's integrity. As diverse applications demand different material capabilities, expanding the range of compatible materials is vital for the long-term success of LOM.
Mechanical Properties of LOM Products
Another challenge lies in the mechanical properties of produced parts. Items created through Laminated Object Manufacturing often demonstrate lower strength compared to those produced using techniques like Stereolithography or Fused Deposition Modeling. This is due to the layered approach of LOM, which can create weak bonds between layers if not properly managed. As such, LOM products may not be suitable for load-bearing applications where structural integrity is paramount.
Generally, products can exhibit reduced impact resistance and rigidity. These mechanical properties may not meet the standards required in fields such as aerospace or automotive manufacturing, where material performance is critical. Understanding these limitations allows designers to make informed decisions when selecting LOM for specific applications.
Scalability Issues
Scalability is a prevalent concern for Laminated Object Manufacturing. While the technology is well-suited for prototyping, transitioning from small-scale production to large-scale manufacturing poses challenges. The current equipment can lead to bottlenecks in production as setup times can be lengthy, and the need for precision increases with the size of the part being manufactured.
Moreover, the economic feasibility of scaling LOM operations remains questionable. The cost of cutting and stacking multiple sheets can escalate, especially when considering the potential material waste generated. Manufacturers must weigh these factors against the benefits of using LOM to ensure sustainable production.
Future Perspectives of Laminated Object Manufacturing
The future of Laminated Object Manufacturing (LOM) holds vast potential. As industries increasingly seek innovative solutions, LOM is positioned as a key player in additive manufacturing. Its unique approach of layering materials opens doors for advancement in production efficiency and material versatility. Several factors will influence the trajectory of LOM technology, which include technological innovations and growth within various industries.
Technological Innovations on the Horizon
Laminated Object Manufacturing is not static; it is evolving. Current research focuses on enhancing the accuracy and speed of LOM processes. Innovations in laser technology, for example, can improve cutting techniques, allowing for cleaner edges and more intricate designs. Other areas of exploration include the development of new binding agents that increase adhesion between layers and reduce production time. Moreover, the automation of LOM machinery will likely transform how products are created, minimizing human error and efficiency losses.
Additionally, integrating LOM with artificial intelligence (AI) and machine learning may optimize design processes. These technologies can analyze numerous parameters to streamline production workflows. The use of smart sensors will gather real-time data, enabling manufacturers to adjust parameters on-the-fly, further enhancing the precision of the final product.
Potential for Industry Growth
The market for Laminated Object Manufacturing is poised for significant expansion. As more sectors discover its benefits, LOM could become a standard technique in industries like aerospace, automotive, and medical devices. The advantage of producing lightweight yet strong components through LOM can lead to enhanced performance in vehicles and machinery, which is a critical consideration in aerospace applications.
Furthermore, LOM is suitable for creating complex geometries that would be difficult or impossible with traditional manufacturing methods. This capability encourages innovation in product design and customization, particularly in industries focused on bespoke solutions.
In the medical field, the demand for personalized medical devices is rising. LOM can fabricate custom prosthetics or tailored instruments that meet specific patient needs, thus enhancing healthcare outcomes.
In summary, Laminated Object Manufacturing stands at a crucial juncture with technology advancements and heightened industry interest. If current trends continue, it may redefine manufacturing possibilities in the near future.
End and Final Thoughts
The Conclusion and Final Thoughts section serves a vital purpose in consolidating the multifaceted discussions presented throughout the article. It encapsulates critical insights into Laminated Object Manufacturing (LOM) and highlights its significance in the expanding field of 3D printing. This segment synthesizes the knowledge gained, providing clarity and a final perspective on the advantages, applications, and challenges associated with LOM.
Laminated Object Manufacturing stands at a unique intersection of innovation and practicality within the larger realm of additive manufacturing. One key aspect highlighted in this article is LOM's versatility in various industries, from prototyping to aerospace, illustrating its broad applicability.
Moreover, the economic benefits it offers cannot be overstated. As businesses increasingly seek to minimize costs while maintaining quality, LOM presents a competitive edge through cost-effectiveness and rapid production capabilities.
A comprehensive grasp of LOM also encourages awareness of its limitations. Understanding these constraints fosters informed decision-making when selecting manufacturing processes suited for specific applications. Evaluating the trade-offs inherent in LOM, including material limitations and mechanical properties, is essential for both researchers and industry practitioners.
In summation, this conclusion validates the importance of continuous exploration in the LOM domain. By recognizing both its strengths and shortcomings, stakeholders can leverage this technology more effectively in their respective fields.
Summary of Key Points
In reviewing the essential elements discussed in this article, several key points stand out:
- Technological Insight: Laminated Object Manufacturing is an important method of additive manufacturing, characterized by layering adhesive-backed sheets to form 3D objects.
- Industry Application: LOM finds use across diverse sectors, including engineering, medical devices, and the automotive industry.
- Cost Efficiency: One of the standout advantages of LOM is its cost-effectiveness compared to other 3D printing methods.
- Challenges in Material Quality: While LOM offers many benefits, there are limitations regarding material choices and the mechanical properties of finished products.
These points frame a clear understanding of LOM's role in modern manufacturing and can guide future discussions around the topic.
Recommendations for Further Research
To fully unlock the potential of Laminated Object Manufacturing, further research is essential in various domains:
- Exploration of New Materials: Investigating alternative materials that can enhance the performance and quality of LOM products is critical.
- Enhancing Mechanical Properties: Research aimed at improving the mechanical characteristics of LOM-produced objects can broaden its applications.
- Integration with Other Technologies: Combining LOM with other manufacturing techniques could lead to greater efficiency and new opportunities in production methodologies.
- Environmentally Sustainable Practices: Studying methods to incorporate sustainable practices and materials into LOM will benefit both users and the environment.