Inline Milk Filters: Importance and Innovations
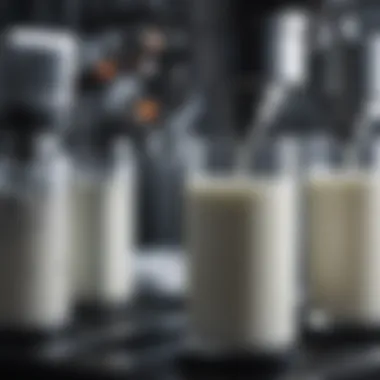
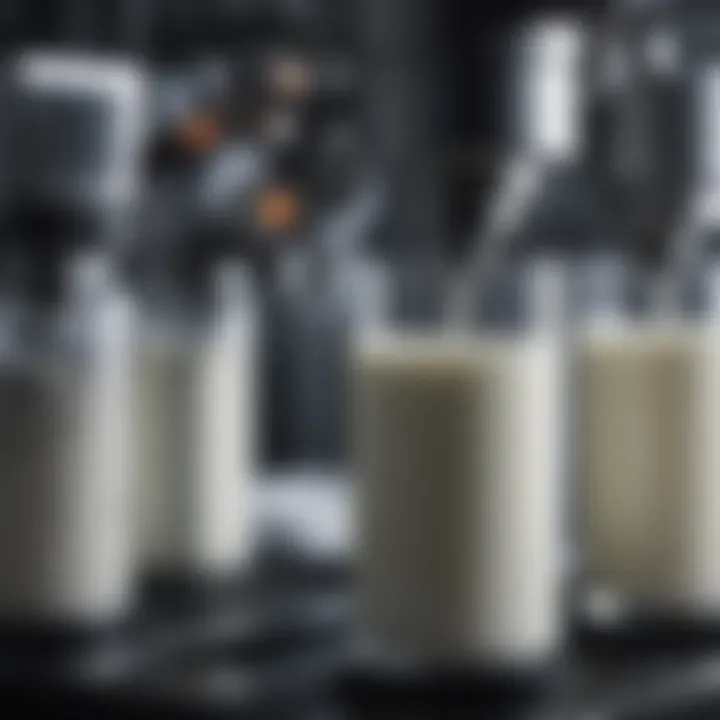
Intro
In the swiftly evolving domain of dairy processing, the significance of inline milk filters stands tall. These systems are not merely accessories to the production line but are pivotal elements that ensure product quality and safety. As regulations tighten and consumer awareness heightens regarding food quality, the role of these filters becomes all the more crucial.
Inline milk filters are designed to remove contaminants that may compromise the integrity of milk, which could range from physical impurities to bacteria. The operation of these filters is often overlooked, yet their influence on quality control in the dairy sector is profound. By employing various filtration mechanisms, they can effectively capture impurities, thus presenting a cleaner, safer product to the consumer.
This article seeks to navigate through the intricate landscape of inline milk filters, exploring their mechanisms, benefits, types, and much more. Through this exploration, we aim to equip academic minds and industry practitioners with a thorough understanding of this essential technology.
Article Overview
Summary of Key Findings
Several vital conclusions emerge from our investigation into inline milk filtering technology:
- Operational Mechanisms: Understanding how various filters work, including depth filters, membrane filters, and others, highlights their particular roles in safeguarding milk quality.
- Regulatory Compliance: The prevailing laws that govern dairy processing emphasize the need for stringent filtration measures to ensure public health.
- Maintenance: Proper upkeep of these filters is fundamental to sustaining their efficacy and prolonging their lifespan, underscoring the need for thorough training of personnel.
- Technological Advancements: The advent of smart technologies and automation has revolutionized how inline filtration can be monitored and managed, paving the way for better efficiency and effectiveness.
Research Objectives
The primary objectives driving this research include:
- To unravel the technical specifications and operational intricacies of different types of inline milk filters.
- To assess the impact of filtration technology on overall dairy quality control processes.
- To illuminate the challenges faced in maintenance and compliance with regulations.
- To explore future trends that could shape the evolution of filtration technology in the dairy industry.
Foreword to Inline Milk Filters
The dairy industry often walks a fine line between quality assurance and operational efficiency. Inline milk filters play a pivotal role in this balancing act. They are not just pieces of equipment; they represent a commitment to delivering quality products while ensuring safety and compliance with industry standards. Their relevance extends beyond just filtering; they enhance the overall integrity of the dairy processing system.
Definition and Purpose
In simple terms, inline milk filters are designed to remove impurities from milk during processing. These impurities can range from dirt and bacteria to fats and proteins that might impact the milk’s quality. The primary purpose of these filters is to ensure that the milk remains safe for consumption and meets regulatory standards.
The filtering process is crucial for maintaining the taste, texture, and nutritional value of milk. So, every time milk flows through an inline filter, it’s getting a clean slate. This process means that consumers enjoy a product that’s not only safe but also of premium quality.
With advancements in technology, the definition of inline milk filters has expanded to include various filtration methods that focus on different aspects of milk quality. For instance, microfiltration is primarily aimed at removing larger particles, while ultrafiltration targets smaller molecules. The purpose remains the same—to maintain the integrity of dairy products by eliminating unwanted elements.
Historical Context
The journey of inline milk filters traces back several decades. Initially, the dairy industry relied on basic filtration methods that were not efficient enough to keep pace with rising quality standards. Filters were often made of coarse materials that struggled to capture smaller particles. This limitation prompted a change in the way filtration was viewed within dairy processing.
As knowledge of microbiology and food safety evolved, so did the filtration techniques. In the 1970s, the industry began seeing the introduction of more sophisticated filtration systems like membrane filters. These were capable of dealing with micro and sub-micro particles effectively. The historical progression from simple filters to advanced inline systems illustrates a growing acknowledgment of both consumer expectations and regulatory demands.
Furthermore, as the market expanded and diversified, the historical emphasis on quality assurance led to innovations aimed at improving filter designs and materials. With each passing decade, inline milk filters have evolved into a refined technology, integrating materials science to address both durability and performance. The history of inline milk filters is not merely about technology but speaks to an evolving understanding of consumer safety and product quality.
In essence, understanding inline milk filters gives us insight into the backbone of dairy processing. It reveals a journey marked by necessity—a commitment to improvement that continues to shape how milk is filtered and perceived today.
Mechanism of Inline Milk Filters
The mechanism behind inline milk filters plays a crucial role in maintaining the quality of dairy products. As we're all aware, milk is a perishable product that requires careful processing to ensure safety and quality. Filters in this context are a protective barrier, ensuring that unwanted particles don't make their way into the final product. Inline milk filters increase efficiency, improve shelf life, and ultimately enhance consumer trust in dairy products.
Filtration Process Explained
The filtration process involves several key steps aimed at purifying the milk. Firstly, milk is pumped through the filter, where various contaminants such as bacteria, dirt, and even larger fat particles are captured in the filtration media. These media types vary between filter specifications and are engineered to cater to specific dairy processing needs. In essence, this technique acts similarly across a range of filtration systems, yet the materials used—such as polymer or ceramic—can greatly influence outcomes.
Notably, inline filtration provides a continuous approach, meaning that the system works efficiently without the need for batch processing. This is vital as it allows for higher throughput and minimized downtime during processing. Thus, the filtration process isn’t just a physical barrier; it’s an integral part of production that influences overall dairy quality.
Types of Filtration Techniques
Diving deeper, the discussion on filtration techniques is essential as it relates closely to how inline milk filters function. There are three primary filtration techniques commonly used in the industry—microfiltration, ultrafiltration, and nanofiltration. Each has its unique properties and serves different purposes within the filtration spectrum.
Microfiltration
Microfiltration serves as a basic yet effective method to remove larger impurities. It generally operates at a porosity rate ranging from 0.1 to 10 microns, which allows it to catch bacteria and some larger fat globules. This technique is widely recognized because it strikes an excellent balance between efficiency and cost. Because it can reduce contamination while allowing desired permeates to pass through, it’s a popular choice among many dairy operations.
However, it's worth mentioning that microfiltration may not be sufficient for tasks requiring finer separations, like breaking down smaller viruses. Thus, while its ability to enhance product clarity is undeniable, it often works best in conjunction with other techniques in comprehensive filtration setups.
Ultrafiltration
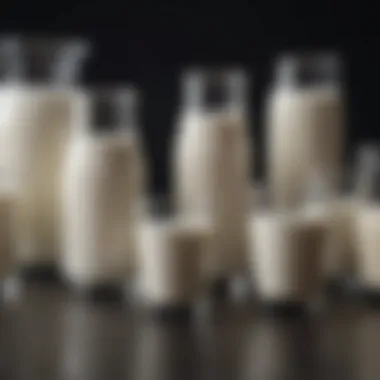
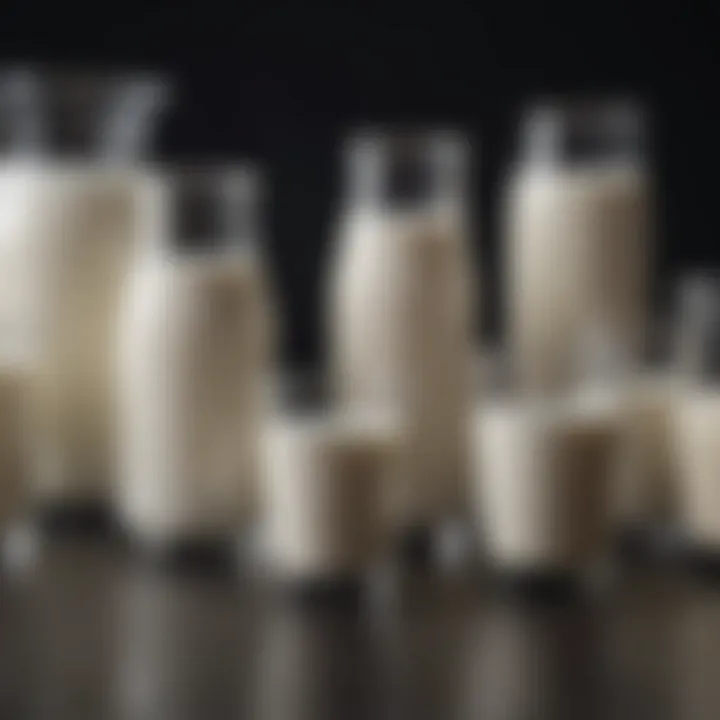
When one looks at ultrafiltration, it becomes clear that this is a more advanced method, positioned to handle smaller particles than microfiltration, specifically within the range of 1 to 100 nanometers. This means it can effectively separate unwanted particles such as lactose and certain proteins. In terms of benefits, ultrafiltration not only contributes to improved milk quality but can also concentrate valuable components for further processing, like whey protein.
What sets ultrafiltration apart is its capability to retain fat content while filtering out water and other undesired solutes. This preservation of quality attributes is increasingly valuable in today’s market where nutritional content is paramount. Though it achieves excellent results, the downside can include higher operational costs and the need for more sophisticated machinery.
Nanofiltration
Finally, we arrive at nanofiltration, a technique that operates at a molecular level—typically around 1 nanometer. This precision allows the removal of even smaller particles, including small salts and low-molecular-weight organics. It is particularly beneficial in producing dairy products with specific formulations, where controlling the mineral content is crucial.
Nanofiltration is noteworthy for its capacity to combine the benefits of both reverse osmosis and ultrafiltration, making its use quite effective in a range of applications. One drawback, however, is the higher energy and maintenance costs, which some may find prohibitive. Yet, the uniqueness of this type often offers long-term benefits by reducing waste and improving overall dairy processing quality.
"Each type of filtration technique brings something unique to the table, and understanding their differences is essential for optimizing milk processing."
Types of Inline Milk Filters
Understanding the variety of inline milk filters is crucial for ensuring the highest quality in milk processing. Each filter type has particular strengths and weaknesses, tailored to diverse operational requirements, thereby influencing the overall safety and purity of the final dairy products. Selecting the right filter type becomes vital not only for quality control but also for optimizing performance and efficiency in production.
Ceramic Filters
Ceramic filters have a long-standing reputation in the dairy industry due to their remarkable durability and effectiveness in removing particulates and microorganisms. These filters are typically made from natural clay materials, providing a porous structure that allows for effective filtration without sacrificing essential minerals in the milk.
- Benefits:
- High resistance to corrosive substances, making them suitable for various cleaning agents.
- Ability to withstand high temperatures, reducing concerns over thermal degradation.
- Minimal environmental impact as they can be cleaned and reused multiple times.
One notable characteristic of ceramic filters is their mechanism of filtration. The fine pores can capture bacteria and larger particles while allowing liquid milk to pass through seamlessly. However, they do require more maintenance compared to other filter types, as clogging can occur, necessitating routine cleaning procedures to maintain their efficiency.
Polymeric Filters
Polymeric filters are increasingly popular due to their versatility and a range of applications in inline milk filtration. Made from synthetic materials, these filters can be engineered to provide specific pore sizes, which is essential for targeting certain contaminants during the filtration process.
- Advantages:
- Lightweight and flexible, making installation easier in various setups.
- Cost-effective compared to some traditional ceramic filters.
- Often exhibit high throughput rates, which means they can process large volumes of milk quickly.
Despite their many benefits, polymeric filters may have drawbacks, such as limited thermal stability. They can degrade under high temperatures, which might present a challenge in certain dairy processing environments. Hence, careful consideration of operational conditions is essential when opting for polymeric filters.
Metallic Filters
Metallic filters, often constructed from stainless steel, are a robust option for inline milk filtration. These filters are highly resistant to damage, corrosion and can withstand high-pressure conditions during processing.
- Key Features:
- Excellent durability and long service life under demanding operational conditions.
- The ability to withstand high temperatures without warping or degrading.
- Simple to clean and often suitable for automated cleaning systems.
The inherent strength of metallic filters allows them to handle significant physical stress, making them an ideal choice for large-scale dairy operations. However, they can be more costly upfront compared to ceramic and polymeric options, which typically factors into a company’s decision-making process when selecting the right inline milk filter.
In summary, the choice of inline milk filter should reflect each dairy operation's specific needs, weighing factors like cost, maintenance, and filtration effectiveness to ensure optimal milk quality.
Material Science Behind Filters
The role of material science in the creation and efficacy of inline milk filters cannot be overstated. It directly impacts not only the effectiveness of filtration methods but also the durability and overall reliability of the filters used within the dairy industry. Understanding the materials behind these filters lays the groundwork for appreciating their diverse capabilities. Different materials exhibit varied properties, which affect how they interact with milk and any contaminants therein. This insight becomes vital for researchers, educators, and industry professionals aiming for precision in dairy processing.
Common Materials Used
When it comes to inline milk filtration, several materials stand as the pillars of quality and efficiency. Here’s a detailed breakdown:
- Ceramics: Known for their exceptional hardness, ceramic filters are adept at resisting wear and tear. They are particularly effective at eliminating bacteria while being relatively easy to clean. Their longevity is impressive, making them a popular choice in many dairy operations.
- Polymers: These synthetic materials, like polyethersulfone (PES) and polyvinylidene fluoride (PVDF), offer outstanding flexibility and can be manufactured to have precise pore sizes. This means that they can be tailored to specific filtration needs, such as targeting particular contaminants.
- Metals: Filters made from stainless steel are favored for their sturdiness and resistance to corrosion. They provide excellent structural integrity and can withstand high pressures, making them suitable for demanding applications.
By selecting the right material, dairy processors can greatly enhance the filtration process, ensuring cleaner, safer milk for consumption.
Durability and Performance Metrics
To maintain a high standard of quality in milk processing, assessing the durability and performance of inline milk filters is crucial. Different materials exhibit unique metrics, influencing their longevity and effectiveness in the field.
Some important performance metrics include:
- Mechanical Strength: The capacity of a filter to resist pressure without failing is a primary consideration. Filters need to handle various operational stresses while maintaining structural integrity.
- Chemical Resistance: Exposure to different cleaning agents is common in dairy environments. Filters must endure regular sanitization without degrading.
- Filtration Efficiency: This refers to the filter’s ability to remove particles and microbes from the milk. High efficiency is essential to meet safety regulations and ensure product quality.
- Life Cycle Cost: Understanding both the initial investment and the long-term maintenance is crucial. A filter that requires frequent replacing may not be cost-effective, even if it performs well in the short term.
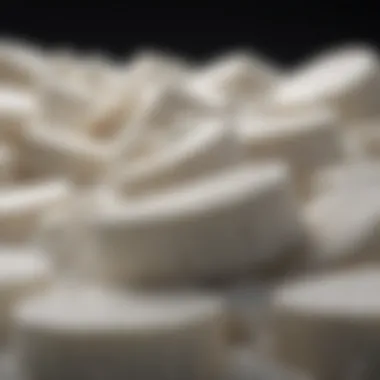
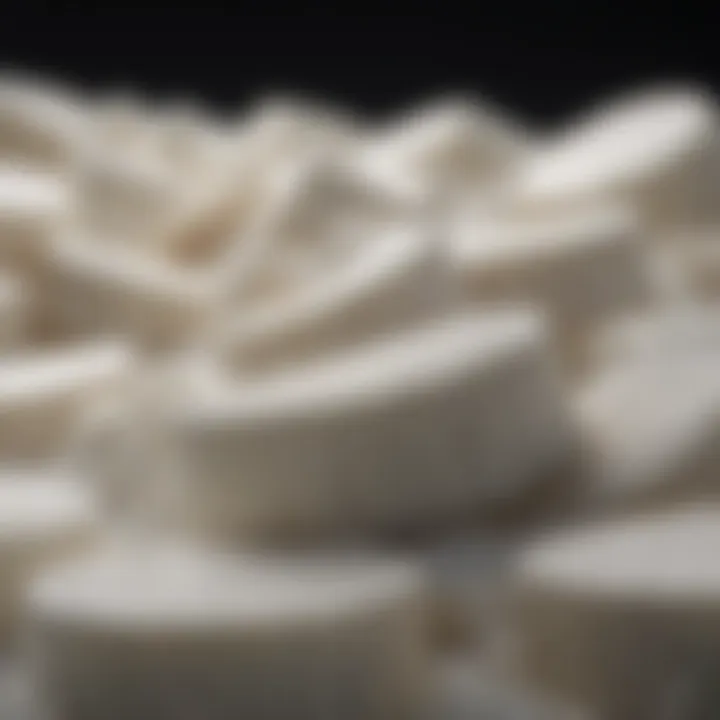
"The choice of material for inline milk filters can vastly influence their performance and longevity, shaping the landscape of dairy safety and quality."
By focusing on durability and efficiency, producers can optimize their filtration systems, leading to better milk quality and operational success.
Regulatory Standards and Compliance
The importance of regulatory standards and compliance in the domain of dairy processing cannot be overstated. These frameworks are not just bureaucratic checkpoints; they play a pivotal role in safeguarding public health, ensuring product integrity, and maintaining consumer trust. For inline milk filters, compliance with these standards ensures that the filtering processes are reliable and that the end product meets safety regulations without compromising quality. Understanding these regulations involves grasping their context, applicability, and the benefits they bring to the production line.
Food Safety Regulations
Food safety regulations are crucial in the dairy industry, shaping the operational landscape for inline milk filtering. Such regulations encompass a wide array of guidelines that aim to minimize foodborne hazards, ensuring that the milk reaching consumers has been treated with utmost care. In the United States, for example, the Food and Drug Administration (FDA) sets stringent standards that govern every aspect of dairy processing. These include parameters for hygiene, equipment sanitation, and regular inspections.
Compliance with food safety regulations involves rigorous testing frequently. Not only does it help ensure that harmful bacteria and contaminants are filtered out effectively, but it also fosters a culture of accountability. If a processing plant fails a safety inspection, it can lead to significant penalties, including fines and even closure. A recent study indicated that 60% of dairy processors have faced compliance challenges at one point, emphasizing the necessity of understanding and adhering to these rules.
"Compliance is not just about following rules; it's about building trust with consumers and ensuring the integrity of products."
An important aspect of these regulations is their adaptability. As technological advancements in filtration arise, regulatory bodies continuously reassess and update guidelines to reflect new findings and innovations. In short, maintaining compliance with food safety regulations is not just a legal obligation but a strategic imperative for any dairy processor leveraging inline milk filters.
Industry Best Practices
Beyond compliance, adhering to industry best practices enhances the effectiveness of inline milk filters and guarantees the overall quality of dairy products. These practices are often established through collaborative efforts among industry leaders, research institutions, and regulatory bodies. They serve as benchmarks for operational excellence and are often tailored to meet specific challenges faced by dairy processors.
One key best practice involves the regular calibration and validation of filtration equipment. Ensuring that the filters function efficiently can be the difference between producing high-quality milk and creating batches that may not pass safety standards. Additionally, proper training for staff on the operation and maintenance of inline milk filters is essential. Employees should be aware of the critical role these filters play and how to troubleshoot common issues that may arise.
Incorporating preventive maintenance schedules also falls under industry best practices. These schedules can drastically reduce downtime and improve the reliability of the filtering systems. Factors such as routine inspections, cleaning protocols, and equipment upgrades should be part of the daily operations. Following these recommended practices not only enhances compliance with food safety laws but also contributes positively to the overall reliability and efficiency of milk processing operations.
Quality Control in Dairy Processing
Quality control in dairy processing is not just a detail; it's the backbone of producing safe, high-quality dairy products. In this fast-paced industry, where consumers are increasingly discerning, ensuring that milk and other dairy products meet stringent quality and safety standards is paramount. Inline milk filters play a pivotal role in this framework, acting as the frontline defense against contaminants and ensuring consistency in product quality. By removing impurities and pathogens from raw milk, these filters not only contribute to the health of consumers but also preserve the integrity of dairy operations.
Impact on Milk Quality
The impact of inline milk filters on milk quality cannot be overstated. These filters eliminate harmful particles, bacteria, and, in some cases, even spores that may spoil milk or lead to foodborne illnesses. When we talk about milk quality, we're diving into various aspects:
- Safety: Milk that's been filtered properly minimizes health risks for consumers. This preventative measure can reduce illnesses related to contaminated milk, thereby boosting consumer confidence.
- Taste and Preservation: Contaminants can significantly affect the taste of milk. By filtering out unwanted substances, inline milk filters help maintain the pure taste that consumers expect. Moreover, reduced microbial loads enhance shelf life, ensuring that milk stays fresh longer.
- Nutritional Value: Clean milk isn't just safer; it's also healthier. Preserving milk's natural nutrients becomes more achievable with effective filtration. High-quality filters help retain the essential vitamins and minerals that are vital for health.
- Regulatory Compliance: Each dairy processor must adhere to rigorous health regulations. Utilizing efficient inline filters is critical in meeting these legal standards, thus avoiding potential fines or shutdowns.
One remarkable case can be observed in large dairy operations, where significant investments in advanced filtration systems have led to a 30% reduction in bacterial counts, subsequently lowering production costs associated with spoilage. This statistic provides practical evidence of how critical quality control is to business sustainability.
Monitoring and Testing Procedures
Effective monitoring and testing procedures form the framework for ensuring the reliability of inline milk filters and, consequently, milk quality. Implementing robust monitoring systems is essential for any dairy processor committed to excellence. Key procedures and best practices include:
- Regular Filter Integrity Tests: Routine checks help determine if filters are functioning as they should. Any changes in filter performance can indicate build-up or blockage, necessitating immediate attention.
- Quality Assurance Sampling: Collecting samples at different stages of the processing line can identify issues earlier, allowing for corrective actions before the product reaches consumers.
- Data Logging: Utilizing data loggers provides essential insights into the performance of filtration systems and other equipment over time. This practice aids not only in immediate troubleshooting but also in long-term optimizations.
- Calibration of Equipment: Ensuring that all testing and monitoring equipment is accurately calibrated can prevent false readings, which can mislead about the health and safety of the product.
"In dairy processing, a stitch in time saves nine. Close monitoring and proactive testing can mitigate the risks of contamination before they balloon into more significant issues."
To wrap things up, quality control stands as a cornerstone of the dairy industry, crucial for maintaining standards and trusting relationships with consumers. Inline milk filters are integral to this process, emphasizing the overlapping nature of technology and tradition in modern dairy operations. Optimizing quality through these measures not only fulfills regulatory requirements but also aligns with consumer expectations for premium dairy products.
Maintenance and Troubleshooting
Maintenance and troubleshooting are the linchpins of successful inline milk filtration systems. These processes don't just keep the filters working; they ensure optimal performance and safeguard the integrity of the milk being processed. Regular maintenance minimizes the risk of unexpected breakdowns, which can lead to costly downtimes and potential product contamination. In an industry where quality control is non-negotiable, all stakeholders must take these tasks to heart.
Routine Maintenance Practices
Establishing a workable routine for maintaining inline milk filters is paramount. Here are several key practices that can help maintain peak performance:
- Regular Cleaning: Depending on the type of filtration system, regular cleaning intervals should be scheduled. For instance, ceramic filters might require a thorough wash every few weeks, while polymeric filters may need less frequent maintenance.
- Visual Inspections: Conducting periodic visual inspections can help spot anomalies. Look for signs of wear, discoloration, or kinks in hoses that might signal underlying problems.
- Calibration Checks: Keeping your system calibrated ensures that the filter operates within the correct parameters. Regularly check the flow rates and validate them against the manufacturer's specifications.
- Replacement Schedules: Filters have a lifespan, and adhering to a planned replacement schedule is critical. Make note of each filter's usage and anticipated life to avoid unexpected failures.
- Documentation: Keep detailed records of all maintenance activities. This helps in identifying patterns that could reveal recurring issues.
These practices not only enhance the longevity of the filters but also contribute to maintaining the overall quality of milk production.
Common Issues and Solutions
Despite the best preventive measures, issues may arise in the operation of inline milk filters. Recognizing these problems early is key to timely intervention. Below are some common issues, along with their corresponding solutions:
- Reduced Flow Rate: A noticeable drop in flow could indicate clogging or fouling of the filter. To remedy this, first increase the backpressure during cleaning. If that doesn't work, the filter might need replacing.
- Leakage: Detecting leaks in the system is crucial. Often, this can be addressed by simply tightening the fittings. If the leak persists, check the condition of seals and gaskets for wear and replace them if necessary.
- Temperature Fluctuations: If the milk temperature is inconsistent, verify the functionality of heat exchangers. In some cases, system recalibration may be needed.
- Unpleasant Odors (When Cleaning): If cleaning yields foul odors, that could signal rancid residues in the system. A more intense cleaning solution might be warranted, along with a thorough rinse to remove any lingering odors.
"Proper maintenance isn't just about fixing things when they break; it's about ensuring that everything runs like a well-oiled machine."
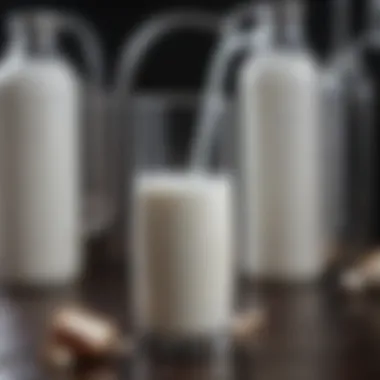
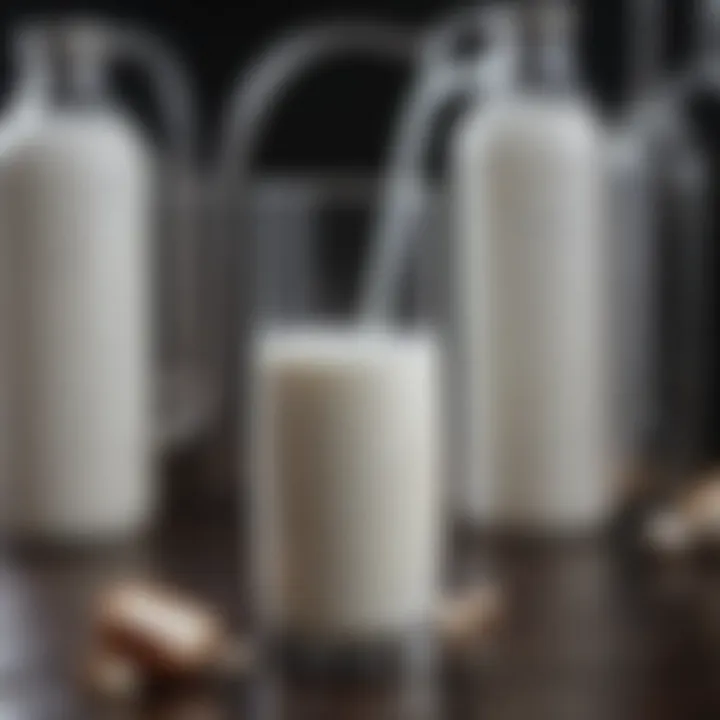
- Unusual Noises: Any strange sounds might indicate mechanical issues within the pump or filter housing. It’s advisable to shut down the system and conduct a comprehensive inspection before proceeding with repairs.
By being proactive and adopting systematic troubleshooting approaches, one can alleviate many common issues before they escalate, leading to smoother operations and contributing to the high standards of dairy production.
Technological Advancements
Technological advancements play a pivotal role in the evolution of inline milk filters, significantly influencing operational efficiencies and product quality in the dairy industry. The integration of innovative filtration solutions directly correlates to improved safety standards, enhanced product shelf life, and superior quality of milk. As dairy processing becomes increasingly sophisticated, so too is the need for updated filtration systems that can meet the rigorous demands of modern markets.
Innovations in Filtration Technology
The advancement in filtration technology has transformed how dairy manufacturers approach cleanliness and efficiency. One notable innovation is the use of smart filtration systems equipped with sensors that monitor the filtration process in real-time. For instance, these sensors can detect fluctuations in flow rates or pressure drops, signaling potential issues before they escalate. This proactive approach helps maintain optimal operation conditions.
Another trend worth mentioning is the development of membrane filtration technology, which has gained ground for its effectiveness in removing contaminants. Different types of membranes, such as ceramic and polymeric, are tailored for specific filtration tasks. These membranes can achieve higher flow rates while ensuring that harmful bacteria and particles are filtered out efficiently.
"The continuous improvement in filtration technology is not just about efficiency, it's about setting new benchmarks in food safety and quality."
With these innovations, dairy processors increasingly leverage automation and advanced materials, reducing manual intervention and the risk of human error. These technological strides do more than streamline processing; they also present opportunities for sustainability, as many systems optimize water usage and reduce waste, contributing to a more eco-friendly practice.
Integration with Modern Dairy Equipment
The symbiotic relationship between inline milk filters and modern dairy equipment enhances the overall productivity of processing plants. Modern equipment such as high-efficiency pasteurizers and homogenizers works hand-in-hand with advanced filtration systems to ensure a seamless production workflow. For instance, inline filters integrated with pasteurization units can maintain milk purity, effectively trapping unwanted particles while allowing for smooth processing.
Moreover, the architecture of current dairy processing lines typically includes modular designs that allow for easy integration of various components. This means that adding or upgrading an inline milk filter can be as simple as plugging and playing, without the need for extensive system overhauls.
In addition, cloud-based monitoring solutions can now connect inline milk filters to centralized control systems, offering operators a bird's-eye view of numerous processes at once. This advancement ensures that processing units operate within predefined parameters, maximizing efficiency while minimizing waste.
Ultimately, the advancement and integration of inline milk filters with modern machinery are not just about quick fixes but fostering a culture of continuous improvement in dairy processing. As the industry progresses, these technological innovations will be critical in shaping a future where efficiency and quality coexist seamlessly.
Future Trends in Inline Milk Filtration
The landscape of inline milk filtration is evolving rapidly, driven by technological advancements and increasing demands for sustainability and product quality. Keeping pace with these future trends is crucial for dairy producers, as they not only enhance operational efficiency but also address pressing environmental concerns. As the dairy industry faces challenges such as rising costs, stricter regulations, and consumer demand for healthier products, understanding these trends will prove to be essential for staying competitive in this market.
Sustainability Considerations
Sustainability has become a cornerstone of modern industrial practices, and the dairy sector is no exception. Inline milk filtration plays a significant role in reducing waste and resource consumption in milk processing. For instance, energy-efficient filtration systems help minimize electricity usage during processing, thereby lowering operational costs. Moreover, many advanced filtration technologies focus on reducing water consumption, ensuring that the processes do not exacerbate freshwater strain.
- Waste Reduction: By filtering out impurities efficiently, producers can ensure higher quality milk, thus decreasing the volume of milk that must be discarded.
- Recyclable Materials: Some manufacturers are now producing inline filters using recyclable materials, which contributes to a circular economy in the dairy processing industry. This helps to lower the carbon footprint and aligns with global sustainability goals.
- Environmental Impact: The selection of renewable energy sources to operate filtration systems signifies a shift in prioritizing environmental concerns in the dairy industry.
Sustainability is not merely an option but is gradually becoming a demand for consumers. Those brands that align their practices with sustainable principles often create a stronger connection with eco-conscious customers. This results in increased brand loyalty and can potentially open new markets. But navigating this landscape requires dedication and innovation, emphasizing the need for sustainable development practices within inline milk filtration.
Advances in Material Science
Material science continues to push the boundaries of inline milk filtration. Innovations in this field lead to the development of filters that are not only more effective but also more durable. Choosing the right material is critical, as it ensures longer service life and lower replacement costs, ultimately boosting the bottom line for dairy processors.
Recent innovations include:
- Nanofiber Membranes: These have become a popular choice due to their remarkable filtering capabilities. Their high surface area allows for greater filtration efficiency while maintaining lower energy consumption.
- Biodegradable Materials: With an increasing emphasis on eco-friendly practices, researchers are developing filters from biodegradable plastics. This shift could revolutionize how inline filtration contributes to waste management in dairy processing.
- Smart Materials: Integration of smart technology into filter media allows for real-time monitoring of filtration performance. This capability provides instant feedback, enabling adjustments to be made without interrupting processing activities.
Advances in material science not only focus on enhancing performance but also emphasize safety and compliance with food safety regulations. As standards continue to evolve, the materials used in inline milk filters will adapt, ensuring they meet both industry expectations and consumer needs.
"The future of inline milk filtration lies in sustainability and innovation, where efficiency meets responsibility."
End
The conclusion serves as a vital component in this exploration of inline milk filters, forging the path toward understanding how these mechanisms sustain quality in dairy processing. First and foremost, it summarizes the intricate interconnections between different facets, encapsulating the essence of discussions from filtration mechanisms to technological advancements.
Summary of Key Insights
Inline milk filters play an essential role in the dairy industry. They ensure that the milk reaching consumers remains free from contaminants that could compromise safety and quality. This article has revealed the importance of several key insights:
- Diverse Filtration Techniques: The different types of filtration methods—microfiltration, ultrafiltration, and nanofiltration—each contribute uniquely to ensuring a safe and palatable product.
- Material Significance: The choice of materials such as ceramic, polymeric, and metallic filters is crucial, as different materials offer varied durability and filtration effectiveness.
- Regulatory Compliance: Understanding regulatory standards helps to navigate the often complex landscape that ensures consumer safety and industry accountability.
- Maintenance Importance: Maintaining these filters not only boosts operational efficiency but also prolongs the lifespan of the equipment, reducing long-term costs.
These insights reinforce the value inline milk filters bring to the production cycle, underscoring their role as fundamental to maintaining milk quality.
Final Thoughts and Implications
Moving forward, the developments in inline milk filtration hint at a promising future for the dairy industry. With increasing emphasis on sustainability, the evolution of materials and techniques can lead to safer, more efficient filtration systems.
"Quality must be a constant focus; inline milk filters are crucial in ensuring the integrity of the final product."
Furthermore, the integration of advanced technologies, including automation and real-time monitoring, is set to revolutionize standard practices, making processes not only more reliable but also adaptable to evolving industry needs.
In summary, investments in inline milk filtration technology are not just investments in quality but are intertwined with safety, sustainability, and economic efficiency. Understanding these implications will be key for stakeholders looking to leverage the advancements in dairy technology for better product outcomes.