IMC Wire Bonding: Techniques and Applications in Electronics
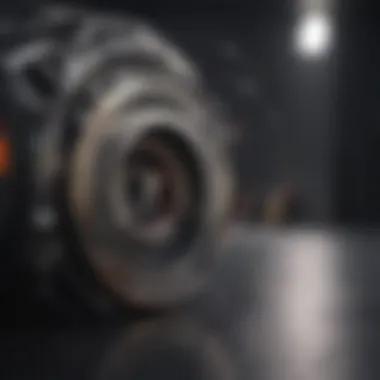
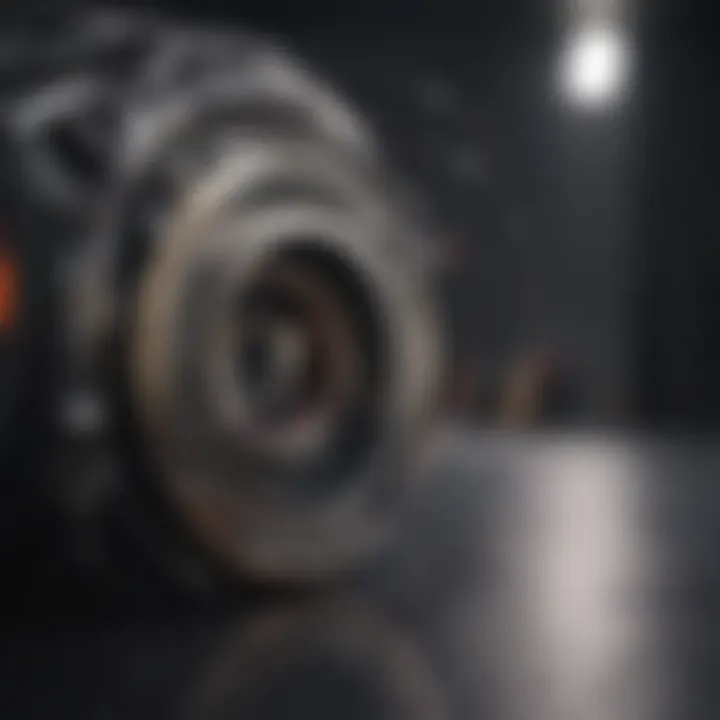
Intro
In the fast-evolving field of electronics, intermetallic compounds (IMC) play a crucial role in wire bonding processes. Specifically, IMC wire bonding has gained prominence in semiconductor packaging. This technique involves several materials and intricate methods that ensure reliable connections between different components on a chip. Examining this topic is essential for those involved in semiconductor design and manufacturing, as it highlights the critical techniques and applications that drive modern electronics.
Article Overview
Understanding IMC wire bonding requires a solid grasp of its foundational aspects. This section provides a summary of the key findings about the methods and materials involved in the bonding process.
Summary of Key Findings
- Bonding Techniques: IMC wire bonding encompasses various techniques, each tailored for specific applications within semiconductor packaging. The most notable methods include ball bonding, wedge bonding, and ribbon bonding. Each possesses unique attributes that can cater to diverse requirements in the manufacturing process.
- Materials Used: The choice of materials in IMC wire bonding is crucial. Common materials include gold, copper, and aluminum, each with distinct characteristics. These materials influence the performance and reliability of the bonds created during manufacturing.
- Challenges Faced: Despite its advantages, IMC wire bonding presents several challenges, including thermal stress, wire deformation, and interface instability. Addressing these challenges is vital for the longevity and performance of electronic devices.
Research Objectives
The primary objectives of this article are:
- To delve into the types of bonding methods utilized in IMC wire bonding.
- To explore the materials applied and their impacts on performance.
- To identify the challenges faced during the wire bonding process.
- To discuss emerging trends and advancements that may shape the future of this technology.
Key Results and Discussions
This section focuses on the main findings and their implications within the semiconductor packaging landscape.
Main Findings
- Standardization in Techniques: The standardization of IMC wire bonding techniques enhances compatibility across various platforms. This leads to improved production efficiency and product quality.
- Material Innovations: Continuous advancements in materials science contribute to the development of new alloys and composites. These innovations have the potential to reduce costs and enhance performance.
"Understanding the nuances of IMC wire bonding is essential for engineers and technologists in the semiconductor realm".
Implications of Findings
The findings presented have profound implications:
- Improved Reliability: By understanding the challenges and methods, manufacturers can create devices that withstand environmental stresses, enhancing product reliability.
- Technological Advancements: The exploration of new materials and methods fosters innovation, paving the way for next-generation electronic devices.
In summary, IMC wire bonding is integral to the semiconductor packaging process. By exploring the methods, materials, and challenges associated with this technique, we can appreciate its importance in the production of reliable and efficient electronics.
Preface to Wire Bonding
IMC wire bonding is a critical process within the field of semiconductor packaging. It is essential for establishing reliable electrical connections between semiconductor devices and their substrates. The significance of this technique cannot be overstated, as it plays a pivotal role in ensuring the performance and longevity of electronic components. This section will elucidate the importance of IMC wire bonding, highlighting the specific elements and benefits that make it a cornerstone in the manufacturing of modern electronics.
Definition of Wire Bonding
IMC, or intermetallic compound, wire bonding refers to a process where wire bonds form conductive pathways between component leads and substrates through metallic interconnections. During this process, a thin wireβtypically made from gold, aluminum, or copperβis thermally or ultrasonically bonded to both the die and the package lead. The advent of IMC wire bonding has allowed for decreasing sizes of electronic packages while enhancing performance reliability.
Historical Context
The history of wire bonding dates back to the mid-20th century when it emerged as a response to the need for miniaturization in electronics. Early methods were rudimentary, often requiring manual precision. However, as technology evolved, so did the techniques applied to wire bonding. By the 1980s, the introduction of thermosonic bonding marked a significant milestone, allowing for the reliable attachment of wires to semiconductor devices at lower temperatures. Today, IMC wire bonding techniques continue to evolve, driven by advancements in materials science and automation, making them indispensable in the production of integrated circuit packages.
Fundamentals of Wire Bonding
Understanding the fundamentals of wire bonding is critical for both practitioners in the field and academicians studying semiconductor packaging. Wire bonding serves as a bridge between the silicon chips and the external circuitry, ensuring reliable electrical connections. Mastery of the basics enhances oneβs ability to diagnose issues, optimize processes, and innovate new solutions in the realm of electronic packaging.
Wire bonding methods have been pivotal in the advancement of microelectronics. With the persistent drive for miniaturization and efficiency, comprehending these techniques contributes to better design and implementation of electronic components. Knowledge of fundamentals lays the foundation for engaging with complex topics, such as bonding reliability and applications in diverse industries.
Basic Principles
Wire bonding relies on principles of metallurgy, physics, and engineering. At its core, the process involves joining two surfaces together using a thin wire, typically made of gold, aluminum, or copper. The selected wire material must possess the appropriate electrical and thermal properties. Each bonding method, whether thermosonic, thermal compression, or ultrasonic, employs specific parameters to achieve the desired results.
Key aspects include:
- Thermal Energy: Most wire bonding methods utilize heat to soften or melt the metal surfaces, enhancing molecular adhesion.
- Mechanical Stress: The application of pressure assists in achieving a strong bond. The interplay between heat and pressure is crucial for proper bonding.
- Surface Interaction: Clean and properly prepared surfaces lead to better bonding quality. Any contaminants can become barriers to effective fusion.
These principles dictate the performance and reliability of the bond, influencing the overall functionality of the device.
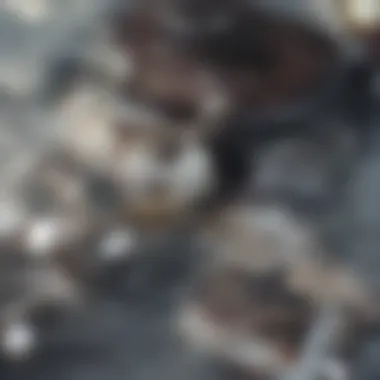
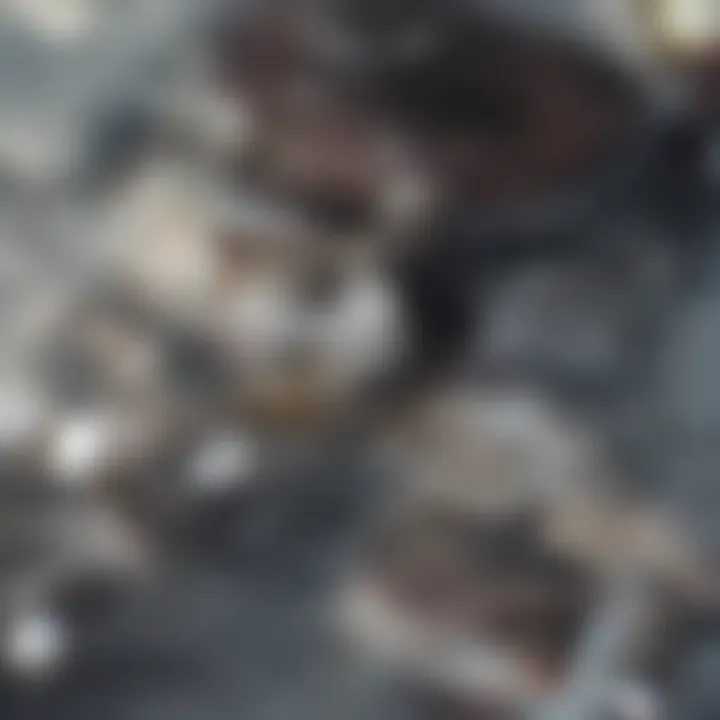
Bonding Mechanics
The mechanics of bonding involve multiple variables that can affect the outcome of the wire bonding process. Each bond requires a careful balance of temperature, pressure, and time.
- Temperature: For thermosonic bonding, a combination of heat and ultrasonic energy is used to facilitate the bond. This requires precise temperature control to prevent damage to sensitive components.
- Pressure: The application of mechanical force is another critical factor. High pressure levels can lead to deformation, while insufficient pressure may result in weak bonds. The right balance fosters effective compression of materials to enhance contact area.
- Time: The duration of applied heat and pressure must be monitored. Excessive exposure can degrade materials, while insufficient time can hinder proper adhesion. Timing is essential for achieving optimal bond quality.
"The effectiveness of wire bonding is fundamentally linked to its mechanical processes, impacting the reliability of electronic devices."
In summary, the fundamentals of wire bonding encompass basic principles that govern the bonding process and the mechanics that influence bond quality. A thorough grasp of these elements establishes a vital context for understanding the complexities and innovations associated with IMC wire bonding.
Types of Wire Bonding Techniques
Wire bonding is an essential process in semiconductor packaging. It connects integrated circuits to their packages and substrates. Different techniques have been developed, each with specific advantages and applications. Understanding these techniques is crucial for professionals in the field. They help ensure reliability and performance of the final product.
Thermosonic Bonding
Thermosonic bonding combines heat and ultrasound for wire bonding. This method uses a heated tool and applies ultrasonic energy to create a bond at lower temperatures than traditional methods. The synergy of heat and sound results in excellent mechanical and electrical connections.
The process begins with wire contact to the bonding pad. The ultrasonic energy is then applied while the tool heats the interface. This technique is especially useful in attaching fine wires, commonly utilized in applications where space is limited. Thermosonic bonding is advantageous for materials like gold and aluminum, which offer corrosion resistance and other beneficial properties.
Considerations for thermosonic bonding include:
- Control of temperature to avoid damaging the substrate.
- Maintenance of the ultrasonic tool to ensure consistent performance.
Thermal Compression Bonding
In thermal compression bonding, mechanical pressure and heat are applied simultaneously. This technique is distinct as it requires no ultrasonic energy. The process works by using a heated bonding tool that compresses the wire against a gold pad. The heat enables the metal surfaces to diffuse, creating a strong metallurgical bond.
This bonding method is often employed in applications where the bond must withstand high reliability demands, such as automotive or aerospace. Thermal compression bonding is particularly suitable for copper wire. It provides excellent performance in terms of bonding strength and resistance to environmental factors.
Factors to keep in mind include:
- The need for precise temperature control, as too much heat can damage the components.
- The requirement for high-quality bonding tools, as they directly affect bond quality.
Ultrasonic Bonding
Ultrasonic bonding is a process that utilizes high-frequency ultrasonic waves to create a bond between materials, typically without the need for heat or pressure. This technique is highly effective for joining dissimilar materials or for applications that cannot tolerate high temperatures.
In ultrasonic bonding, a wire is vibrated at ultrasonic frequencies while it is pressed against the bond area. This causes the surfaces to soften and create a bond without melting them. As a result, this technique allows for bonding on sensitive components and delicate materials, making it suitable for applications in the medical field and other industries where heat can be detrimental.
Important considerations for ultrasonic bonding include:
- Selection of appropriate materials, as compatibility can affect bonding efficacy.
- Careful control of process parameters to ensure optimal bond quality without damaging the substrates.
Overall, the choice of wire bonding technique depends on the specific application requirements, materials involved, and desired bond characteristics. Understanding the strengths and limitations of each method allows professionals to make informed decisions in their use of IMC wire bonding.
Materials Used in Wire Bonding
In the realm of IMC wire bonding, the choice of materials is fundamental to achieving reliable and effective connections. Various factors dictate this choice, including the application's demands, the types of devices being bonded, and the operational environment. Understanding the materials used not only impacts the performance of electronic circuits but also affects long-term reliability and functionality.
Wire Types and Specifications
The wires used in IMC wire bonding play a pivotal role in ensuring strong electrical connections. Common wire materials include gold, aluminum, and copper. Each type exhibits unique characteristics.
- Gold Wire: Often regarded as the standard due to its excellent conductivity and resistance to oxidation. However, it is costlier than other materials.
- Aluminum Wire: A popular choice due to its good conductivity and lower cost. It's suitable for applications where cost is a significant consideration but may be less effective under harsh environments.
- Copper Wire: Known for its superior electrical performance, but requires proper handling to prevent tarnishing. Furthermore, copper bonding requires specific techniques to achieve optimal results.
Specifications of these wires, such as diameter and tensile strength, are crucial as they determine the wire's suitability for various bonding techniques. Wires with smaller diameters can be used in high-density applications, while thicker wires serve well in more robust connections. Careful selection based on these criteria ensures that bonding processes yield the desired quality and reliability.
Substrate Materials
Substrate materials also significantly influence the IMC wire bonding process. The choice of substrate determines bond strength and electrical performance. Common substrate materials include silicon, ceramic, and metals.
- Silicon: Widely used due to its compatibility with semiconductor fabrication processes. Siliconβs properties make it ideal for high integration density applications.
- Ceramic: Offers excellent thermal and chemical stability which is advantageous in harsh environments. However, its brittleness must be taken into account when utilizing bonding techniques.
- Metal: Used for high-performance applications that require enhanced thermal conductivity. Choices like copper and aluminum alloys are prevalent and are often coated with materials that enhance bonding capability.
When choosing a substrate, considerations include thermal expansion coefficients and surface roughness. The right substrate ensures that wire bonds maintain integrity, even under varying thermal and mechanical stresses.
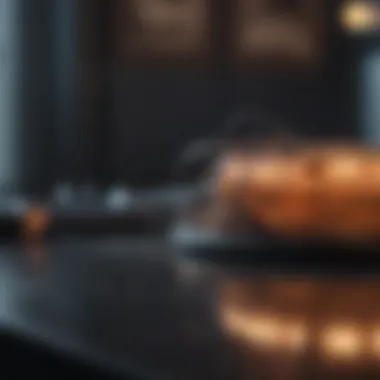
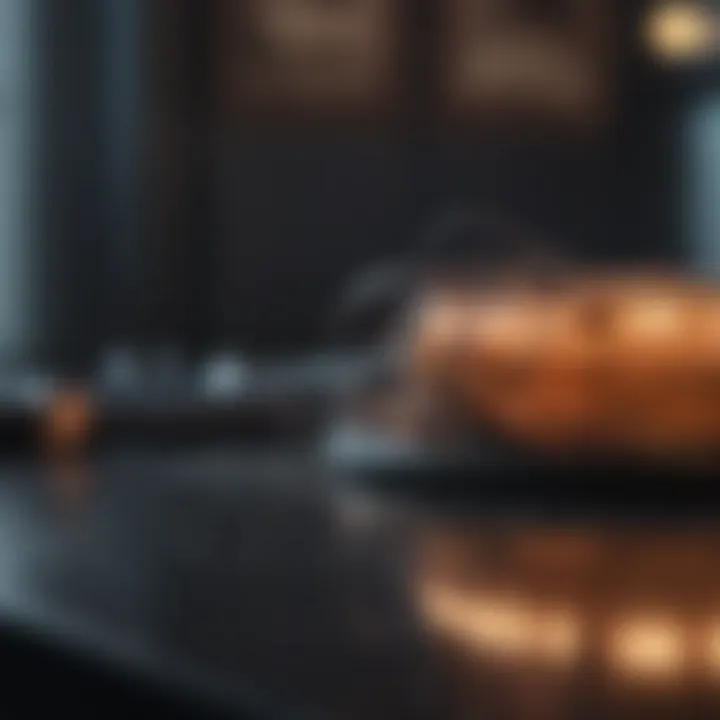
Applications of Wire Bonding
The section on applications of IMC wire bonding is crucial for understanding the practical implications and benefits of this bonding method in various industries. IMC wire bonding plays a significant role in ensuring reliable connections necessary for the functionality and longevity of electronic devices. The growing complexity of circuitry in modern electronics further underscores the need for advanced bonding techniques. This section focuses on three main sectors: consumer electronics, automotive, and medical devices. Each of these areas showcases the adaptability and critical nature of IMC wire bonding.
Consumer Electronics
IMC wire bonding serves an essential role in the consumer electronics sector. This industry demands lightweight, compact, and highly efficient devices. Wire bonding techniques provide excellent solutions for manufacturers looking to optimize space without sacrificing performance. Products like smartphones, tablets, and laptops rely on intricate circuit designs where IMC wire bonding ensures the stability of electrical connections.
Moreover, the combination of thermal stability and good electrical conductivity in bonded wires contributes to device reliability. In a market where users expect quick access to technology, effective wire bonding can lead to fewer malfunctions and longer device life. The continuous demand for smaller size and higher performance drives innovation in this area.
Automotive Industry
In the automotive industry, IMC wire bonding is vital for the production of advanced electronic systems. Modern vehicles are equipped with numerous electronic control units that handle everything from engine management to infotainment systems. Here, bond strength and durability are paramount.
The application of IMC wire bonding helps ensure that connections can withstand the harsh conditions of automotive environments, including extreme temperatures and vibrations. This durability is crucial for functions like safety systems and navigation, where reliability directly impacts performance. Car manufacturers increasingly implement wire bonding in applications like power distribution, battery management systems, and sensor technologies. Automotive electronics are on the rise, making effective bonding techniques indispensable.
Medical Devices
In medical device manufacturing, IMC wire bonding has become increasingly important due to the critical nature of these applications. Devices such as pacemakers, glucose monitors, and imaging systems must maintain high reliability. Any failure in connectivity can have severe consequences for patients.
The biocompatibility of materials used in conjunction with wire bonding is also a concern. Medical devices often require wires that do not cause adverse reactions. IMC wire bonding techniques can accommodate such requirements, allowing for the creation of safe and effective medical technology. As technology evolves, the integration of advanced sensors and wireless communication systems in medical devices further benefits from robust bonding methods.
"The efficiency of IMC wire bonding in enhancing the reliability of electronic connections cannot be overstated; it is foundational in sectors where precision is critical."
Challenges in Wire Bonding
Challenges in IMC wire bonding play a crucial role in the field of semiconductor packaging. Despite the advancements in technology, reliability and compatibility issues persist. This section examines these challenges, highlighting their implications for efficiency and effectiveness in wire bonding processes.
Bonding Reliability Issues
Bonding reliability is a primary concern in IMC wire bonding. Inconsistent bonding can lead to significant product failures, especially in critical applications. Factors affecting reliability include surface contamination, temperature fluctuations, and mechanical stress during operation.
- Surface Quality: Clean surfaces are paramount. Any foreign particles can impede the bond, causing failures.
- Thermal Stress: Variations in temperature can weaken the bond. This is especially true for devices that operate in extreme conditions.
- Mechanical Forces: The bond must withstand forces during operation. If the bond is not robust enough, it can fail, leading to circuit malfunctions.
These issues necessitate rigorous testing and quality assurance measures to ensure that the bonds can withstand operational stresses over time.
Material Compatibility
Another significant challenge in IMC wire bonding is material compatibility. Different materials used in wire bonding and substrates can react poorly with each other. Understanding these compatibility issues is vital for achieving optimal performance.
- Material Selection: The proper selection of materials is critical. Gold, copper, and aluminum are commonly used, but each has its specific advantages and disadvantages.
- Intermetallic Formation: During the bonding process, intermetallic compounds may form, which can affect reliability. Monitoring and choosing the right bonding techniques can mitigate these risks.
- Coating Technologies: Some materials may require coatings to enhance bonding. The choice of coating can also affect compatibility.
In summary, addressing the challenges of bonding reliability and material compatibility is essential. They directly impact the performance and longevity of semiconductor devices, making them key considerations in IMC wire bonding.
Quality Control in Wire Bonding
In the realm of IMC wire bonding, quality control serves a fundamental purpose. This process ensures that the bonds created are not only reliable but also meet the strict performance criteria needed in semiconductor applications. Quality control focuses on various aspects, from material selection to the final product inspections. Ensuring high-quality bonds directly contributes to the longevity and performance of electronic devices.
Unreliable wire bonding can result in catastrophic failures, which are not only costly but also detrimental to user safety. Hence, applying robust quality control measures is essential. These measures include systematic inspections and rigorous testing methods designed to catch issues early, minimizing potential problems later in the manufacturing process.
Inspection Techniques
Inspection techniques are vital components of quality control in wire bonding. They help in identifying defects or inconsistencies in the bonding process. Various methods can be evaluated for effectiveness and accuracy:
- Visual Inspection: This is the primary step in quality assurance. Trained personnel use magnifying glasses or digital imaging systems to assess bond formation. They look for flaws such as incomplete bonds or wire misalignment.
- Automated Optical Inspection (AOI): This method utilizes advanced imaging technology to detect defects. It compares the actual bond image against a predetermined acceptable standard, allowing for quick identification of errors.
- X-ray Inspection: X-ray technology is employed to view the internal structure of the wire bonds. This inspection method allows for the detection of invisible issues, such as hidden cracks or voids. It is essential for confirming bond integrity without damaging the components.
Each method has its advantages and drawbacks, necessitating a tailored approach depending on the specific aspects and requirements of the production process.
Testing Methods
Testing methods are critical for validating the integrity and reliability of wire bonds. Several approaches are tailored to uncover potential weaknesses and prevent future failures:
- Pull Test: This method involves applying a force to the wire bond in a controlled manner. The aim is to determine the strength of the bond and its resistance to external stresses. A successful bond will withstand the applied force without detaching.
- Shear Test: Similar to the pull test, this technique evaluates the bond strength by applying shear force. The test helps in assessing the intermetallic compound (IMC) layer that forms during bonding, critical for the bond's long-term durability.
- Dye Penetrant Testing: This non-destructive method uses colored dye to highlight surface cracks or defects. It is useful in further verifying the bond quality unnoticed through visual inspection alone.
Implementing comprehensive testing alongside inspection techniques creates a robust quality assurance framework. This dual approach supports the advancement of reliable, high-performance electronic systems in varied applications.
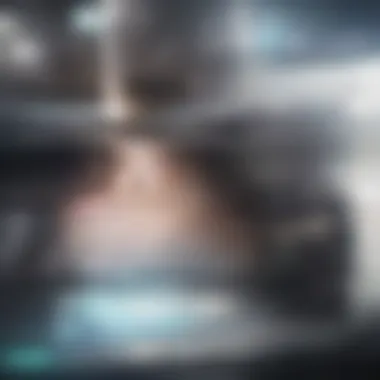
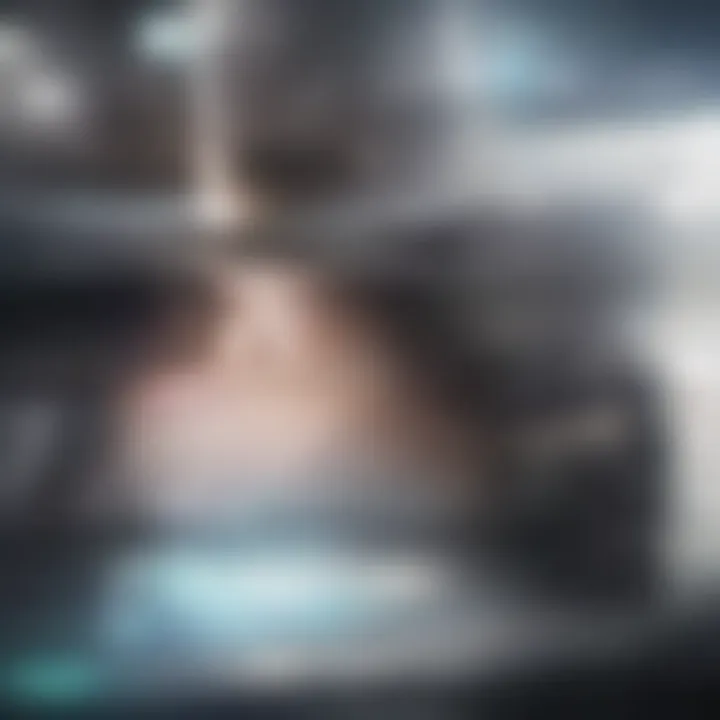
"Effective quality control in wire bonding not only prevents defects but also enhances overall product reliability, critical for maintaining competitive advantage in the electronics industry."
The future of quality control in IMC wire bonding will likely include increased automation and smarter technology integration. This progression is necessary for meeting the demands of modern electronics, where reliability and performance are paramount.
Recent Advancements in Wire Bonding
Recent advancements in IMC wire bonding represent pivotal strides in semiconductor packaging technology. The integration of new methodologies and technologies signifies not only progress but also a response to the evolving demands of the electronics industry. As devices become more compact and complex, the bonding processes must evolve to maintain reliability and performance. This section will detail two vital areas of innovation: automation and robotics, and nano-bonding techniques. Both areas provide significant benefits that enhance efficiency and effectiveness in wire bonding operations.
Automation and Robotics
Automation is reshaping the landscape of IMC wire bonding. By introducing robotic systems into the bonding process, manufacturers gain numerous advantages. One prominent benefit is the increase in precision and consistency. Robotic arms equipped with advanced sensors achieve highly accurate placements of bonds. This is crucial for minimizing defects, which can have profound effects on device performance.
Efficient automation also results in faster production cycles. Automated systems can operate at high speeds, reducing operational costs by lowering the time required for each bonding process. Furthermore, automation reduces the risk of human error, which is significant in high-stakes environments like semiconductor manufacturing.
- Key benefits of automation in IMC wire bonding include:
- Enhanced accuracy and reduced defects
- Increased throughput and efficiency
- Lower operational costs and reduced waste
Moreover, the adoption of automated inspection technologies complements this trend. These systems can identify and assess bond quality in real time, allowing for immediate adjustments and ensuring adherence to high standards.
Nano-bonding Techniques
Nano-bonding techniques represent another groundbreaking advancement in the field of wire bonding. The growing demand for miniaturized electronic components necessitates precise bonding on a nanoscale. Nano-bonding enables manufacturers to achieve better interconnect performance by using advanced materials and methods that secure wires with minimal physical footprint.
This technique allows for bonds that are not only smaller but also more reliable, contributing to the longevity of electronic devices. The materials used in nano-bonding often exhibit superior electrical and thermal properties, making them suitable for high-performance applications.
In summary, the fusion of automation and nano-bonding methods is expected to redefine the standards of wire bonding. These advancements ensure that manufacturers can keep pace with the relentless demand for improved performance while navigating the challenges posed by more intricate designs.
The future of IMC wire bonding relies heavily on these innovative practices to drive efficiency and reliability in semiconductor products.
Future Trends in Wire Bonding
The future of IMC wire bonding is characterized by rapid advancements and the integration of new technologies. This section highlights key trends that are likely to shape the industry. Understanding these future trends is crucial for professionals, researchers, and students alike, as they not only impact the efficiency and cost-effectiveness of wire bonding but also the overall innovation in semiconductor applications.
Emerging Technologies
Emerging technologies are set to redefine the landscape of IMC wire bonding. Innovations in materials science are leading to the development of wires that can tolerate higher temperatures and stress. Advanced materials like copper and gold are being optimized for better conductivity and reliability. Moreover, the advent of new bonding techniques is changing the operational paradigms.
One notable trend is the integration of multi-layered bonding approaches. This technique enhances the bonding strength and thermal stability, which is essential for high-performance applications in advanced electronic devices. Additionally, robotic automation and AI-enabled systems are streamlining the bonding process, increasing precision and reducing cycle time.
Adoption of these technologies ensures that companies can produce smaller and more efficient devices, staying competitive in the ever-evolving electronics market. These advancements also come with the potential benefit of reducing material waste, which can lead to more sustainable manufacturing practices.
"Emerging technologies in IMC wire bonding not only enhance performance but also pave the way for eco-friendly production methods."
Market Trends
The market for IMC wire bonding is responding dynamically to global shifts in demand. One prominent trend is the increasing need for miniaturization in electronics. Consumers demand smaller, more efficient devices, which are driving innovations in wire bonding techniques. As a result, manufacturers are investing in research and development to produce finer wires and more precise bonding methods.
Additionally, the rise of 5G technology is influencing market trends significantly. IMC wire bonding plays a pivotal role in the manufacturing of 5G compatible devices. The demand for higher bandwidth and faster data transmission requires the development of advanced bonding techniques to meet these specific needs.
Another key trend is the escalating focus on smart technologies and the Internet of Things (IoT). As more devices become interconnected, the complexity of semiconductor packaging increases, necessitating advancements in wire bonding technologies. Manufacturers are adapting to these trends by employing more sophisticated quality control measures and enhancing reliability in their bonding processes.
Ultimately, staying attuned to these market trends allows companies to innovate and align their strategies to achieve long-term growth in the IMC wire bonding sector.
Epilogue
The conclusion of this article underscores the significance of understanding IMC wire bonding within the semiconductor packaging domain. In an era where electronic devices are becoming increasingly complex, effective wire bonding techniques are essential. They ensure the reliability and efficiency of electronic connections, which directly impact device performance.
Summary of Key Points
This article has examined several critical facets of IMC wire bonding:
- Techniques: Various bonding methods such as thermosonic bonding, thermal compression bonding, and ultrasonic bonding were discussed. Each technique has its unique advantages and challenges, applicable in different scenarios.
- Materials: The specifications of wire types and substrate materials are paramount. The right choices contribute to successful bonding and enhance device longevity.
- Applications: From consumer electronics to medical devices, IMC wire bonding plays a vital role in diverse industries.
- Challenges: Reliability issues and material compatibility remain ongoing concerns within the field. Understanding these challenges can lead to better design and production strategies.
- Future Trends: The integration of automation and nano-bonding techniques illustrate how the industry is evolving to meet higher demands and ensure precision in wire bonding processes.
Final Thoughts
The potential of IMC wire bonding extends beyond current applications, hinting at future advancements that could revolutionize electronic manufacturing. As technology progresses, an emphasis on research and development within wire bonding techniques will be crucial. The profound impact of these techniques on the functionality and efficiency of electronic devices cannot be understated. Furthermore, for students, researchers, and industry professionals, acquiring knowledge about these techniques positions them well in a competitive landscape. Keeping abreast of market trends and technological advancements will be beneficial for advancing careers and contributing to the evolution of modern electronics.
"As innovations unfold, wire bonding will continue to play a key role in shaping the future of electronic devices."
Understanding and applying effective wire bonding processes can provide significant competitive advantages in the electronics sector.