Exploring the Versatility of Epoxy Film Adhesives
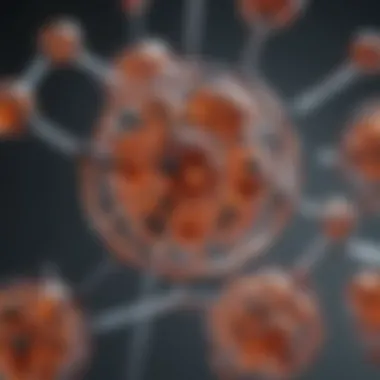
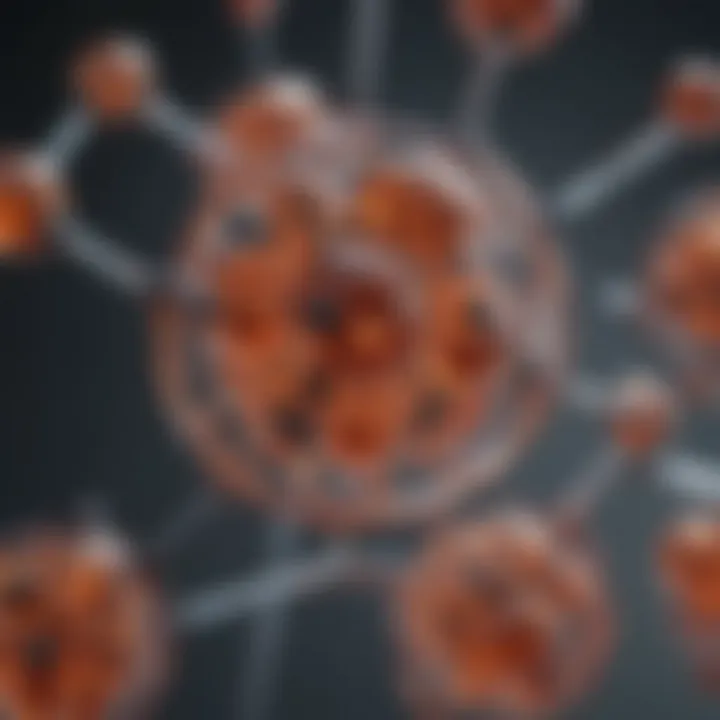
Intro
In today’s fast-paced world, adhesive technologies are making waves across a multitude of industries, and epoxy film adhesives are no exception. These specialized adhesives, which may appear as thin sheets or films, offer a unique blend of strength and versatility. They serve as a critical component in applications ranging from aerospace to automotive manufacturing, underscoring their relevance in modern engineering and design.
Epoxy film adhesives are particularly valued for their exceptional bonding capabilities, chemical resistance, and thermal stability. The precision that they afford during the assembly processes makes them a favorite among engineers and technicians alike. However, not all epoxy adhesives are created equal; their formulations can vary dramatically, influencing both performance and application suitability.
As we delve into this intricate world, we will explore not only the fundamental properties that make epoxy film adhesives stand out but also the latest trends shaping their usage in sustainable practices. From examining their manufacturing processes to their diverse application scenarios, this exploration seeks to provide a comprehensive understanding of both established and emerging practices in adhesive technology.
Prolusion to Epoxy Film Adhesive
The journey through the realm of adhesives often leads us to encounter numerous compounds, but few resonate with the same versatility and effectiveness as epoxy film adhesives. Understanding this topic is vital, as these adhesives serve as silent heroes in a multitude of industries, binding materials together with remarkable strength and longevity. In this segment, we shed light on essential characteristics and the significance of epoxy film adhesives within various practical applications.
One notable aspect is their ability to endure harsh environments, which makes them invaluable for applications where standard adhesives might falter. They excel in both structural and non-structural bonding, and their range of temperatures and chemical resistance sets them apart. Furthermore, they facilitate efficient bonding methods that are often less labor-intensive than traditional adhesives, offering time and cost savings. Through uncovering how these adhesives operate, users can make informed choices tailored to their specific needs.
Defining Epoxy Film Adhesives
Epoxy film adhesives are two-part adhesives composed of resin and hardener. These are available in a film form and are usually applied to surfaces before curing. Upon curing, they transform into a rigid, durable bond that can withstand a variety of stresses. Their unique molecular structure allows for excellent adhesion to a variety of substrates, which includes metals, composites, and plastics. These adhesives are known for their superior mechanical properties, making them remarkably effective in challenging environments, such as aerospace and automotive sectors.
The essential nature of epoxy film adhesives goes beyond mere adhesion. They often deliver additional benefits, like protecting against moisture and corrosion. It's important to recognize that the effectiveness of these adhesives also hinges upon proper surface preparation and environmental conditions during application.
Historical Context and Development
The evolution of epoxy film adhesives can be traced back to the mid-20th century. Originally developed for aerospace applications, their formulation has since expanded significantly as technological advancements took hold. During the initial development, these adhesives were tailored for high-performance bonding in demanding situations, especially at high altitudes.
As industries progressed, the demand for stronger, lightweight materials grew, and epoxy film adhesives became a staple in manufacturing processes. Not only did they allow the bonding of dissimilar materials, but their heat resistance made them an attractive option for sectors where component integrity is critical. As we ventured into the 21st century, continuous innovation has seen the introduction of new formulations that cater to specific needs, including eco-friendly options that align with today's sustainability goals.
"The development of epoxy film adhesives represents a blend of science and practical application that has transformed various industries."
Chemical Composition and Properties
Understanding the chemical composition and properties of epoxy film adhesives is pivotal for anyone looking to harness their potential. Most notably, the effectiveness of these adhesives hinges on their formulation, which combines various chemical components that impart the desired mechanical and thermal characteristics. Moreover, the significance of this topic lies in its direct correlation with application suitability across different industries.
Key Chemical Components
Epoxy film adhesives are typically crafted from a mix of basic ingredients that are finely balanced to yield superior performance. Here are some of the key components:
- Epoxy Resins: The backbone of any epoxy adhesive, these resins are known for their excellent adhesion properties, allowing them to bond effortlessly with a variety of substrates. The selection of resin is critical; for instance, bisphenol A or bisphenol F are popular choices due to their robustness.
- Curing Agents: Integral to the hardening process, these chemicals react with the epoxy resin to initiate the curing. Hardeners can vary—some are aliphatic, while others are aromatic, influencing the final adhesive properties. For example, anhydride hardeners provide good heat resistance but require precise handling.
- Fillers and Additives: These are included to modify specific characteristics of the adhesive such as flexibility, viscosity, or thermal stability. Common fillers include silica and talc, used to enhance mechanical strength, while certain additives may improve resistance to UV light or chemicals.
In essence, the careful selection and balance of these components dictate not only the initial performance of the adhesive but also its longevity and durability under various environmental conditions.
Adhesive Properties and Characteristics
The properties of epoxy film adhesives can make or break their performance in real-world applications. Each characteristic contributes to an adhesive's efficiency and practicality, catering to specific needs in multiple sectors.
- Adhesion Strength: This is arguably one of the most crucial properties. Epoxy adhesives typically offer superior adhesion due to their chemical bonding capabilities, making them suitable for high-performance applications where reliability is key. Interestingly, the strength can vary significantly depending on the surface finish of the materials being bonded.
- Temperature Resistance: Many epoxy adhesives can withstand extreme temperatures without losing their adhesive properties. Some formulations can resist heat in excess of 230°C (446°F). This aspect is invaluable in applications like aerospace, where exposure to harsh conditions is commonplace.
- Chemical Resistance: The capacity of epoxy adhesives to resist degradation from various chemicals is another hallmark feature. This resilience makes them ideal for automotive and industrial applications involving exposure to solvents and oils.
- Cure Time and Workability: Every application has its time constraints. The cure time of epoxy adhesives can be adjusted through the choice of curing agents, which is essential for optimizing processing times in manufacturing scenarios.
"The true essence of epoxy film adhesives is in their unique balance of properties that cater to a range of demanding applications across industries."
For further research, you can delve into detailed resources on Wikipedia or explore related discussions on Reddit.
Manufacturing Processes
In the realm of epoxy film adhesives, understanding the manufacturing processes is crucial for a variety of reasons. These processes not only determine the physical and chemical properties of the adhesive but also influence its performance, reliability, and cost-effectiveness. The way these adhesives are produced affects their composition, which in turn has a direct impact on their application potential. With various industries relying on high-performance adhesives, ensuring that manufacturing techniques meet stringent standards is paramount.
Overview of Production Techniques
Production of epoxy film adhesives involves multiple techniques designed to create a material that meets specific criteria for performance and durability. One common method is the solvent casting process, where a blend of epoxy resin and hardener is dissolved in a solvent. This solution is then spread onto a substrate, forming a thin film once the solvent evaporates. This technique allows for uniform thickness and can be easily adjusted to meet specific application needs.
Another method, film extrusion, employs heat and pressure to mold the adhesive into the desired thickness, often used in the mass production of film adhesives. This approach not only strengthens the adhesive properties but also improves the speed of production.
- Benefits of these techniques:
- Considerations:
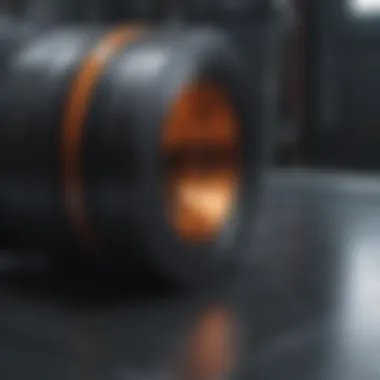
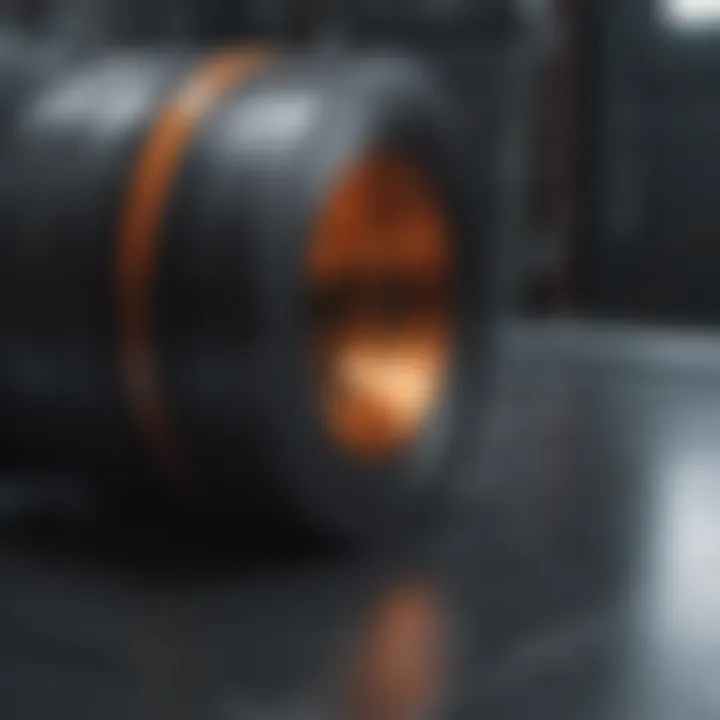
- Flexibility in producing various thicknesses
- Scalability for mass production
- Optimized formulations can improve adhesion properties
- Environmental impact due to solvents
- Need for precise control over temperature and pressure
Quality Control Measures
Strict quality control measures are essential in the production of epoxy film adhesives to ensure consistency and performance. The slightest variation in formulation or processing conditions can lead to subpar adhesives that fail to meet the rigorous demands of industries like aerospace and automotive.
Quality assurance begins with rigorous raw material testing. Before any manufacturing begins, the epoxy resin, hardener, and any additives are subjected to thorough analysis. These tests assess not only chemical composition but also potential impurities that might affect adhesive performance.
Once the adhesive is manufactured, it undergoes several evaluations, including:
- Cohesion Tests: Ensuring the adhesive holds together under stress.
- Adhesion Tests: Evaluating how well the adhesive bonds to various substrates.
- Thermal Testing: Determining resistance to high and low temperatures.
Regular audits and batch testing help maintain quality over production cycles, ensuring products meet or exceed industry standards.
"Quality control is the backbone of adhesive manufacturing; without it, we would be playing dice with reliability."
In summary, the manufacturing processes of epoxy film adhesives play a vital role in determining their effectiveness. By focusing on advanced production techniques and implementing rigorous quality controls, manufacturers can create adhesives that perform well under a wide range of conditions, ultimately leading to more successful applications across various fields.
Performance Metrics
In the realm of epoxy film adhesives, understanding performance metrics is crucial for professionals who've got their hands in applications spanning from aviation to electronics. These metrics not only gauge the effectiveness of adhesives but also illuminate paths for innovation and improvement, guiding formulations that meet stringent industry standards.
Temperature Resistance
Temperature resistance in epoxy film adhesives is of utmost importance, especially in high-stakes environments like aerospace and automotive industries. Characters such as thermal stability define how an adhesive maintains its bonding strength when exposed to variable heat.
- The ability to sustain integrity even at extreme temperatures can prevent catastrophic failures that often stem from thermal degradation.
For instance, in the aerospace sector, adhesives must withstand conditions far beyond the average heat levels experienced in normal operation. The formulation of high-performance epoxy film adhesives often involves the addition of specific fillers or modifiers, enhancing their resistance to thermal creep and dimensional changes.
Some of these adhesives can endure temperatures ranging from -60°C to 150°C or more, ensuring reliability in demanding conditions. The repercussions of ignoring temperature resistance can be severe, resulting in delamination or joint failure.
Mechanical Strength and Durability
Mechanical strength and durability are the cornerstones of epoxy film adhesive performance. A deep dive into these aspects shows why they matter immensely. Adhesives need to withstand both static and dynamic loads without breaking down. Mechanical properties are often quantified through metrics like tensile strength, shear strength, and elongation at break.
- High tensile strength means the adhesive can resist pulling forces, while excellent shear resistance ensures it can handle lateral forces effectively.
Durability is about longevity. It relates to how well the adhesive performes0 over time when exposed to environmental factors such as humidity, UV rays, and chemicals. For example, automotive applications necessitate adhesives that can resist wear-and-tear while maintaining strength through years of service and exposure to varying elements.
"The longevity and performance reliability of an adhesive has a direct impact on the safety and efficacy of the final product."
Cure Time and Workability
Cure time and workability are intertwined aspects of epoxy film adhesives that dictate how conveniently they can be utilized. In many industries, time is money, and quicker curing can translate to greater efficiency.
- Epoxy adhesives generally require a defined period to reach optimal bond strength after application. This factor greatly varies based on environmental conditions and specific formulations.
Workability refers to the ease of application before cure completion. Some epoxies set rapidly, favoring projects that demand quick turnaround. Conversely, others offer extended working times, allowing for adjustments during application. In critical operations, knowing the exact cure time is essential to avoid rework that could lead to operational delays or increased costs.
In summary, performance metrics serve as the guiding compass for evaluating epoxy film adhesives. Just like fine-tuning a race car, understanding and optimizing these aspects ensures optimal performance in the field.
Applications Across Industries
The significance of epoxy film adhesives resonates through various sectors, making them fundamental to many manufacturing and repair processes. These adhesives yield substantial advantages owing to their unique properties, like high strength, resistance to environmental factors, and versatility in applications. Understanding the role these adhesives play in different industries offers deeper insights into their operational effectiveness and potential for innovation.
Aerospace Applications
In the aerospace industry, epoxy film adhesives are paramount. They are utilized to bond structural components of aircraft and spacecraft, critical for safety and performance. The high strength-to-weight ratio of these adhesives is particularly beneficial; it allows lightweight construction methods that enhance fuel efficiency. Bonding materials such as composites, metals, and plastics, epoxies deal effectively with harsh operating conditions where temperature fluctuations or environmental exposure are common. The ability to maintain structural integrity during extreme pressure changes is crucial in aerial applications.
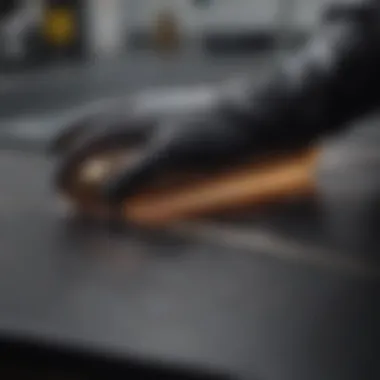
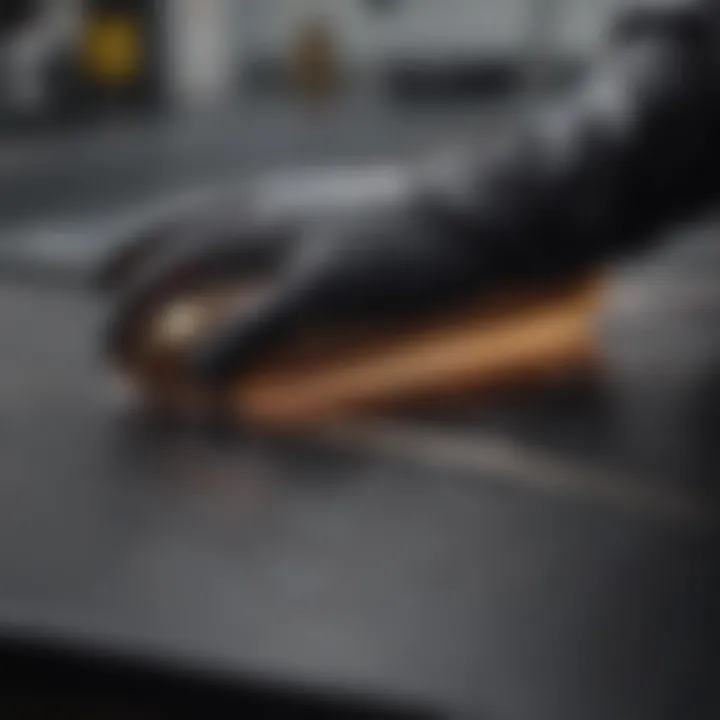
- High Strength: These adhesives are known for their exceptional mechanical properties, which ensure that components remain intact even under significant stress.
- Temperature Resiliency: Epoxy film adhesives can withstand high temperatures, which is essential for sustained flight environments.
Automotive Utilization
The automotive sphere also greatly benefits from epoxy film adhesives. These are used extensively in vehicle assembly, impacting various parts from the body to electronics. Adhesives in cars must ensure strength while also being lightweight, and this is where epoxy performs exceptionally well. With advancements in electric vehicles, the need for effective adhesion of lightweight materials, such as in battery assemblies, is growing. Epoxy adhesives meet these increasing demands by providing robust joints that are essential for modern vehicles.
- Corrosion Resistance: Automotive applications often expose materials to corrosive environments, and epoxy seals protect joints from moisture and salt.
- Improved Aesthetics: Using adhesives instead of traditional fasteners can create smoother surfaces, enhancing the vehicle's visual appeal.
Electronics Assembly
In electronics, epoxy film adhesives have carved a niche due to their insulating properties and ability to bond dissimilar materials. They are used to encapsulate components, protecting them from moisture and environmental interference. The application of these adhesives in printed circuit boards (PCBs) and LED technology illustrates their utility. They not only ensure secure attachment of components but also help with heat dissipation, which is vital for performance.
"The versatility of epoxy adhesives enables their use where mechanical stresses and thermal management are both critical."
- Thermal Conductivity: Some formulations allow heat dissipation, which helps prevent overheating of sensitive components.
- Electrical Insulation: The insulating properties of epoxy protect sensitive electronic parts from interference and ensure longevity.
Construction and Civil Engineering
The construction industry leverages epoxy film adhesives for diverse applications, ranging from bonding panels to repair and strengthening structural components. They enhance the integrity and durability of buildings and other constructions. For example, epoxy is crucial in applications requiring strong bonds in cold weather or damp environments, where traditional adhesives might fail.
- Structural Bonding: Epoxy’s exceptional bonding capacity implements reliable connections in precast and cast-in-place concrete, crucial for high-strength construction.
- Repair Works: When retrofitting older buildings, these adhesives can provide the necessary strength and stability without the need to replace materials, making them a cost-effective solution.
Innovations in Adhesive Technologies
The landscape of adhesive technologies is evolving rapidly, especially within the realm of epoxy film adhesives. As industries push the boundaries of design and performance, innovations become essential not only for meeting existing demands but also for anticipating future challenges. This section zeroes in on the advancements taking shape in formulation and the intriguing applications of nanotechnology, both of which are pivotal for modern adhesives.
Advancements in Formulation
The formulation of epoxy film adhesives has undergone significant transformation over recent years. Traditionally, these adhesives were developed with certain baseline properties, leaving little room for customization. Now, however, manufacturers have begun to experiment with new ingredients and techniques to create products that offer tailored solutions for specific applications.
Key Elements of Modern Formulations:
- Hybrid Compositions: By blending traditional epoxy resins with other biocompatible or high-performance materials, formulators can enhance specific properties, such as flexibility and resistance to environmental factors.
- Low-Viscosity Formulations: These innovations allow for easier application and better wetting of surfaces, ensuring stronger bonds. This is particularly important in thin film applications where consistency is crucial.
- Cure Mechanisms: Innovative curing agents and systems—like UV or heat-activated methods—enable more efficient processing without compromising on bond strength.
Such formulation advancements not only improve performance but also streamline production processes, making them more efficient. Manufacturers can now adapt quickly to market needs, which is invaluable as competitiveness increases in various sectors that rely heavily on adhesives.
Nanotechnology Applications
Nanotechnology offers a captivating frontier in the development of epoxy adhesives. By manipulating materials at the molecular level, companies can create adhesives with enhanced properties that traditional methods struggle to achieve. The integration of nanoparticles into epoxy formulations brings forth substantial benefits, reshaping the capabilities of these adhesives.
Benefits of Nanotechnology in Adhesive Applications:
- Improved Mechanical Properties: Nanoparticles can significantly strengthen the adhesive matrix, resulting in enhanced tensile strength and impact resistance.
- Enhanced Thermal Stability: The coupling of nanoparticles with epoxy can lead to better heat resistance, widening their applicability in high-temperature environments.
- Barrier Properties: Epoxy adhesives infused with specific nanoparticles can be engineered to create barriers against moisture and gases, crucial for industries like aerospace and electronics—places where reliability is paramount.
In practical terms, a manufacturer might incorporate silica nanoparticles to boost the hardness and durability of an epoxy adhesive for use in structural bonding applications. This added resilience can markedly lengthen the lifespan of components, allowing for both economic and performance-related advantages.
"Innovations in adhesive technologies are not just about making stronger adhesives but also about creating smarter materials that can adapt to their environments."
As the field progresses, there are ethical considerations regarding the sustainability of sourcing these nanomaterials, which manufacturers must address. Balancing performance with environmental impact will be essential.
The merging of advanced formulations and nanotechnology not only represents a shift in how epoxy films are perceived but also opens up a whole world of possibilities across various industrial domains. As researchers continue to explore these innovations, we are bound to see a ripple effect that could redefine the standards for adhesive technologies.
Sustainability and Environmental Impact
Sustainability is now a central consideration in various industries, and the field of adhesives is no exception. The use of epoxy film adhesives, while valuable for their strength and versatility, poses certain environmental challenges that need to be tackled earnestly. This section delves into the importance of sustainability in the context of epoxy film adhesives, examining eco-friendly alternatives and strategies for recycling and waste management. The goal is not just to comply with regulations but to proactively embrace methods that keep our planet’s future in mind.
Eco-Friendly Alternatives
As environmental awareness grows, there's an increasing shift toward adopting eco-friendly alternatives in adhesive technologies. Eco-friendly epoxy film adhesives can be crafted to minimize harmful emissions and reduce VOCs, or volatile organic compounds. These alternatives often utilize renewable resources, which means leveraging raw materials that do not deplete the earth’s finite resources. Some notable options include:
- Water-Based Epoxy Adhesives: These formulations substitute solvents for water, greatly reducing harmful emissions. They can provide the same performance as traditional options, but with a smaller environmental footprint.
- Bio-Based Epoxy Resins: Derived from renewable materials like plant oils, these resins offer a sustainable path. While still in their development stages in large-scale applications, their potential is vast, tapping into a market that cares about origin and impact.
- Low-Emission Curing Agents: Utilizing alternative curing agents that produce fewer emissions offers a double benefit—maintaining the bonding quality while lessening environmental impact.
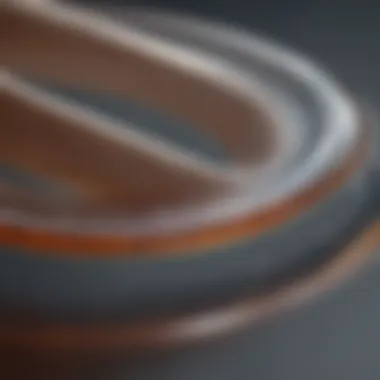
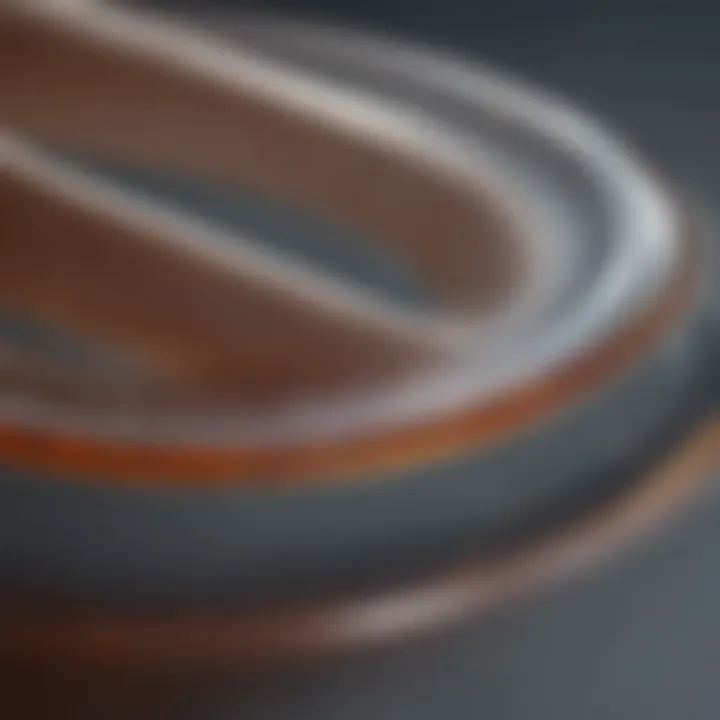
"Shifting towards eco-friendly alternatives not only benefits the environment but also aligns with a growing consumer preference for sustainable practices."
These eco-friendly options do come with challenges, such as the need for extensive research to ensure performance parity with traditional adhesives, but the industry is gradually moving towards addressing these points.
Recycling and Waste Management
Managing waste from epoxy film adhesives is just as crucial as exploring eco-friendly alternatives. Traditional epoxy adhesives, once cured, are often not recyclable and can contribute heavily to landfill waste. However, several strategies can be employed to enhance recycling efforts and reduce environmental harm:
- Curing Technology Innovations: Advances in curing technology have led to the development of adhesives that can be uncured or remolded in certain conditions. This allows for easier recycling and reprocessing.
- Closed-Loop Systems: Some manufacturers are moving towards closed-loop systems where the adhesive waste can be collected and reprocessed into new products, maintaining the material in use and lessening the need for virgin material.
- Education and Training: Educating industry professionals on proper disposal methods and the importance of recycling solutions can foster a culture of sustainability within the sector. Awareness is half the battle; effective practices follow close behind.
- Collaboration with Recycling Facilities: Establishing partnerships with recycling plants that are equipped to handle complex adhesive materials is essential. This strategy can help to elevate recycling rates and reduce overall waste.
In sum, the push towards sustainability in the epoxy film adhesive industry involves a multi-faceted approach that combines eco-friendly alternatives and advanced recycling strategies. With an eye on these practices, the industry can not only reduce its environmental impact but also meet growing market demands for sustainable solutions.
Challenges and Limitations
Understanding the challenges and limitations of epoxy film adhesives is critical for anyone venturing into their application or development. These aspects not only influence the performance of these adhesives but also dictate their usability across various sectors. This segment illuminates the hurdles that need addressing to optimize the advantages of epoxy film technologies.
Performance Limitations
Even though epoxy film adhesives boast impressive properties, they are not without their shortcomings. A few key performance limitations include:
- Temperature Sensitivity: While many epoxies can withstand substantial heat, prolonged exposure to extreme temperature variations can compromise their structural integrity, leading to potential failure in high-stress applications.
- Moisture Absorption: Some formulations tend to absorb moisture, which can lead to degradation in adhesion strength over time. In environments with high humidity, this could be a deal-breaker.
- Brittleness: Epoxy films can become brittle under certain conditions, meaning they may not flex well under mechanical stress. This can limit their effectiveness in applications that require a bit of give and take.
By recognizing these limitations, manufacturers and users can develop strategies to enhance the formulations or select the appropriate adhesive for the job, considering nature of the environment it's put thro.
Regulatory and Compliance Issues
Adherence to regulatory standards is a necessary evil in the world of adhesive technology. Regulatory and compliance issues surrounding epoxy film adhesives encompass various factors that professionals must navigate.
- Health and Safety Regulations: Certain epoxy formulations may contain hazardous components that require careful handling. Compliance with regulations such as OSHA (Occupational Safety and Health Administration) guidelines ensures that users are protected against potential health risks.
- Environmental Regulations: The environmental impact of epoxy adhesives is under increasing scrutiny. Regulations often require manufacturers to limit volatile organic compounds (VOCs) in their products. Some jurisdictions impose strict guidelines on disposal and recycling of unused or expired adhesives, pushing the industry further toward greener options.
- Industry Standards: Industries such as aerospace or automotive often have stringent quality standards. Non-compliance with specific industry benchmarks can lead to product rejection or catastrophic failures, which could have repercussions far beyond the manufacturing floor.
Future Trends in Epoxy Film Adhesive Technology
In an ever-evolving industrial landscape, the future of epoxy film adhesive technology is crucial for stakeholders across various fields. The role they play along with advancements not only impact production efficiency but also sustainability practices and product performance. Exploring these future trends allows industries to stay competitive and innovative in their approaches. Here are some key areas to consider that contribute to the ongoing development of epoxy film adhesives.
Emerging Market Opportunities
The demand for epoxy film adhesives is on the rise, creating new market opportunities. Different industries, such as aerospace, automotive, and electronics, are on the hunt for robust, versatile adhesives that can meet increasing performance requirements.
- Aerospace Sector: There’s a heightened focus on lightweight materials which are essential for reducing fuel consumption. Epoxy film adhesives offer superior bonding capabilities without adding significant weight. Companies are likely to invest in research aimed at developing adhesives that withstand extreme conditions, fostering growth in this market.
- Automotive Innovations: As electric vehicles become more prevalent, the need for durable adhesives suited for battery and structural components is critical. Future trends indicate that epoxy film adhesives will evolve to enhance thermal and chemical resistance, making them perfect candidates for automotive assembly.
- Electronics Miniaturization: In electronics, compact device designs require adhesives that maintain bond strength while occupying minimal space. There's a growing opportunity for formulations that allow for faster curing times as devices demand shorter production cycles.
The convergence of these trends emphasizes a broader shift towards high-performance, specialized adhesives that cater to specific needs.
Projected Advances in Research and Development
As the demand for epoxy film adhesives surges, so does the focus on R&D to refine their properties and applications. Researchers are making strides to enhance various aspects, creating a future laden with advancements:
- Smart Adhesives: There's buzz around developing adhesives that can respond to environmental changes. These smart adhesives might change properties based on temperature, moisture, or other factors, optimizing performance in real-time.
- Bio-Based Components: With the call for environmentally-friendly materials echoing louder, epoxy formulations that incorporate bio-based or recycled feedstocks are gaining traction. This approach could vastly reduce the carbon footprint, aligning with global sustainability goals.
"Innovation in epoxy film adhesive technology isn't just about performance; it's linked to the environmental impact and the drive for smarter solutions."
- Nanotechnology Integration: The incorporation of nanomaterials can significantly improve the performance of epoxy adhesives. Enhanced strength, barrier properties, and heat resistance are anticipated outcomes that could elevate these adhesives to a new level altogether.
In summary, the future landscape of epoxy film adhesives is promising, driven by necessity and guided by innovation. Industries that can effectively adopt these trends will not only gain a competitive edge but will also contribute positively to environmental stewardship. The interplay of market demands and technological breakthroughs stands to reshape the way epoxy film adhesives are used, leading to an impactful evolution in several critical sectors.
Closure
The topic of epoxy film adhesives is crucial due to their indispensable role across various industries. They are not just a mere bonding agent; their properties directly influence the success of projects, from aerospace engineering to electronics assembly. In this article, we have highlighted key aspects of epoxy film adhesives, such as their chemical properties, manufacturing processes, and the evolving trends in their utilization.
Key Takeaways
- Diverse Applications: Epoxy film adhesives are used in several fields, showcasing their adaptability and effectiveness.
- Performance Metrics: Temperature resistance, mechanical strength, and workability are vital considerations when choosing the right adhesive.
- Sustainability Issues: The growing emphasis on eco-friendly alternatives paves the way for innovations in adhesive technologies.
- Challenges Ahead: Understanding the limitations and regulatory frameworks is essential for successful implementation in any industry setting.
- Future Directions: There are promising trends in research and market opportunities that hint at groundbreaking advancements in adhesion techniques.
Final Thoughts on Epoxy Film Adhesives
In summary, epoxy film adhesives represent a sophisticated intersection of chemistry and engineering. Their unique properties offer solutions to complex challenges faced by various sectors. As industries move towards more sustainable practices, the potential for epoxy films to evolve is vast. The careful integration of innovative formulations alongside compliance to environmental standards stands to reshape the future landscape of adhesive technology.
"Epoxy film adhesives are more than mere bonders; they encapsulate the future of construction and manufacturing."
In the fast-paced world where technology and design are evolving, understanding the nuances of these adhesives is essential for students, researchers, and professionals. The knowledge gathered from this detailed exploration positions stakeholders to make informed decisions that could significantly impact their fields.