Exploring Additive Manufacturing of Polymers
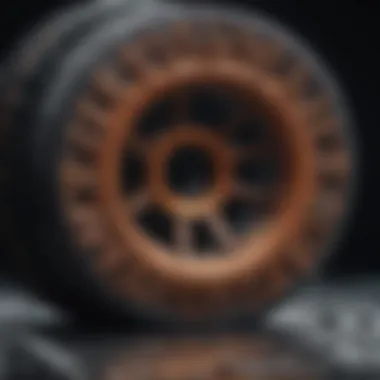
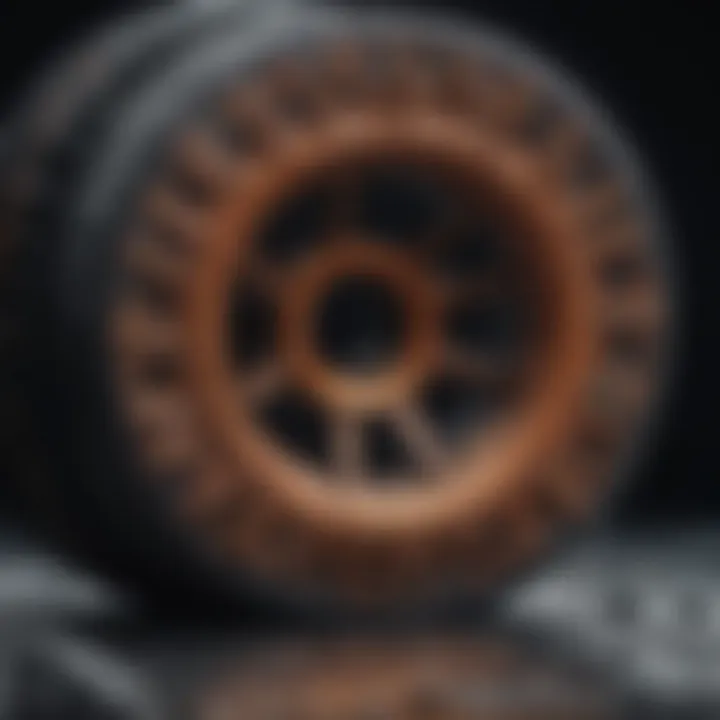
Intro
The landscape of modern manufacturing is continuously evolving, driven by technological breakthroughs and innovative practices. Among these advancements, additive manufacturing of polymers stands out as a transformative force. This technique not only redefines how materials are created but also significantly influences various industries, from aerospace to healthcare.
In this section, we embark on a journey through the core concepts and applications of polymer additive manufacturing. We will explore its foundational principles, delve into the various types of polymers used, and investigate their behaviors during production processes. A keen focus will be placed on the implications of sustainability, as it increasingly shapes the narrative surrounding this technology.
The discussion will extend to the latest advancements in the field, providing insights that will prove invaluable for students, researchers, educators, and professionals alike. By synthesizing various aspects of this topic, we aim to present a comprehensive guide that elucidates the significance, challenges, and future of polymer additive manufacturing.
Article Overview
Summary of Key Findings
The additive manufacturing of polymers reveals a myriad of possibilities. Key findings include:
- The flexibility of design that additive manufacturing offers, enabling the creation of complex geometries previously deemed impossible.
- The diversity of polymers suitable for additive manufacturing, such as acrylonitrile butadiene styrene (ABS), polylactic acid (PLA), and thermoplastic elastomers.
- Significant advancements in materials science that enhance the mechanical properties of printed objects.
Research Objectives
The objective of this article is twofold:
- To provide a detailed understanding of the principles and methods of polymer additive manufacturing. This includes investigating how different polymer types behave during the manufacturing process and how their unique properties can be leveraged to enhance performance.
- To discuss the implications of sustainability and future trends. This encompasses the exploration of bio-based materials, waste reduction, and energy-efficient production techniques, all of which are crucial in the context of environmental stewardship.
In essence, this exploration aims to illuminate the evolving role of polymer additive manufacturing in reshaping production methodologies across various industries.
Prologue to Additive Manufacturing
Additive manufacturing represents a radical shift in how materials are designed, produced, and brought to life. This innovative approach, often identified with 3D printing, enables the creation of complex structures layer by layer, a process that offers numerous advantages over traditional subtractive methods. In the contemporary manufacturing landscape, understanding additive manufacturing is not just beneficial, but essential.
Embracing this method opens doors to unparalleled creativity and customization, providing designers and engineers the ability to iterate quickly on prototypes without the prohibitive costs normally associated with tooling.
Consider this: traditional manufacturing often resembles sculpting from a block—removing material until the desired shape emerges. In stark contrast, additive manufacturing is like building a sculpture from the ground up, where layers of material come together to create intricate designs. This type of manufacturing isn't just a gimmick; it has tangible benefits across industries ranging from healthcare to aerospace.
A key aspect to appreciate in additive manufacturing is its versatility. Polymers, in particular, are at the heart of this technology due to their moldability, lightweight properties, and resilience. Further, the rapid development of material science contributes positively, broadening the range of suitable polymers, which can then be tailored for specific applications.
Additionally, considerations around sustainability and environmental impacts are emerging increasingly in discussions today. Additive manufacturing can significantly reduce waste compared to conventional methods—an important factor as we face growing concerns over resource depletion.
By understanding the basics of additive manufacturing, one gains insight into the entire lifecycle of product development, from conceptualization up to the finished product. By digging into specific elements, benefits, and potential challenges, we set up a comprehensive exploration of this subject.
"Additive manufacturing is transforming what is possible in design and production, allowing for creations that were previously thought unfeasible."
Defining Additive Manufacturing
Additive manufacturing, broadly defined, encompasses a variety of technologies that build objects by adding material in successive layers. This process stands in direct contrast to traditional manufacturing techniques, which often involve subtracting material from a larger block or forging new inputs through high-energy processes.
Generally speaking, additive manufacturing can be broken down into several methods, including fused deposition modeling and stereolithography, which are popular within the realm of polymer fabrication. Each technique has its unique features and applications, demonstrating the adaptability of this approach to meet diverse manufacturing needs.
Historical Context
The journey of additive manufacturing dates back several decades, finding its origin in the 1980s with the pioneering work of Chuck Hull. He developed stereolithography, the first documented 3D printing method, which allowed for the rapid production of prototypes. Over the years, advancements in technology laid down the pathway for numerous other techniques and materials to emerge, tailoring additive manufacturing to a wider array of applications today.
As this technology has progressively evolved, industries have embraced these methods not only for prototyping but also in full-scale production. Cutting across fields, from automotive to healthcare, additive manufacturing stands as a cornerstone for innovation in design and production.
Key Terminology
When diving into additive manufacturing, it's crucial to be acquainted with certain terms to facilitate understanding:
- 3D Printing: Commonly used interchangeably with additive manufacturing, it primarily refers to the process of creating three-dimensional objects from digital files.
- Filament: This is the thermoplastic material used in Fused Deposition Modeling, typically sold in spools.
- Layering: A fundamental principle in additive manufacturing, referring to the method of building parts one layer at a time.
- Support Structures: Temporary constructs added during the printing process to support overhanging features, removed in post-processing.
These terms foster a better foundational grasp on the subject, preparing readers for deeper discussions on the applications and implications of polymer additive manufacturing in the following sections.
Types of Additive Manufacturing Technologies
Understanding the different sorts of additive manufacturing technologies is crucial because they directly affect the manufacturing process and the properties of the finished product. Each technology has unique advantages, limitations, and ideal use cases, making them suitable for various applications. This diversity in additive manufacturing processes allows for better optimization of materials, costs, and production speed, tailoring solutions to specific needs within a wide array of industries.
In this section, we will explore several primary technologies employed in polymer additive manufacturing, providing insights into their operation, applications, and impact on manufacturing.
Fused Deposition Modeling (FDM)
Fused Deposition Modeling, commonly known as FDM, is one of the most widely recognized and utilized 3D printing technologies. In the FDM process, a thermoplastic filament is fed into a heated nozzle, where it is melted and extruded layer by layer to build up the final part. This approach is appreciated for its simplicity and cost-effectiveness, making it particularly popular among hobbyists and small businesses.
The benefits of FDM are numerous:
- Material Variety: A wide range of thermoplastics can be used, from common ones like polylactic acid (PLA) to more advanced materials such as acrylonitrile butadiene styrene (ABS).
- Accessibility: The technology is relatively affordable, with many desktop 3D printers available at reasonable prices.
- Ease of Use: User-friendly design and operation make it approachable for amateurs and experts alike.
However, it is not without challenges; for instance, parts might pose strength issues along the z-axis due to the layer bonding process, leading to potential weaknesses in applications requiring high mechanical performance.
Stereolithography (SLA)
Stereolithography is a pioneering technology in the field of additive manufacturing. It employs an ultraviolet (UV) laser to cure liquid resin layer by layer. SLA is known for creating exceptionally detailed and smooth parts, making it ideal for applications that demand high precision.
Key advantages of SLA include:
- High Resolution: SLA can produce intricate designs with surface finish quality that other methods struggle to match.
- Material Options: There are a variety of resins available, each imparting unique properties—from flexibility to temperature resistance.
This method can also disappoint if you need large parts, as the build volume is often limited, leading to longer print times. Additionally, the post-processing of SLA prints generally involves cleaning and curing, which adds complexity to the workflow.
Selective Laser Sintering (SLS)
Unlike both FDM and SLA, Selective Laser Sintering uses a laser to fuse powdered material. In SLS, a laser selectively melts or sinters the powder particles together. Upon completion of each layer, a new layer of powder is rolled onto the build platform, and the process repeats.
SLS stands out due to its ability to:
- Create Complex Geometries: The powder serves as support during printing, allowing for intricate designs without needing additional supports.
- Material Versatility: Materials such as nylon and metal powders can be utilized, expanding the applications of SLS significantly.
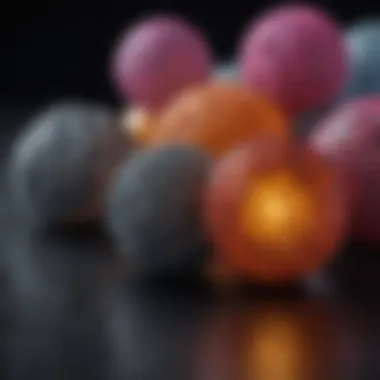
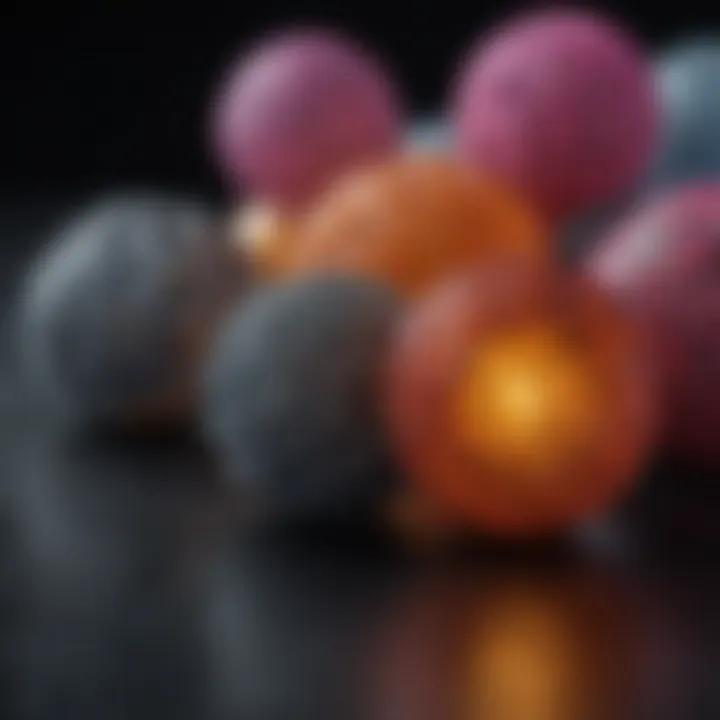
One of the downsides is the cost of the machines and materials. It's generally more expensive than FDM and not as accessible for casual users. Yet, in industrial applications, its advantages in strength and functional capability often outweigh these limitations.
Binder Jetting
Binder Jetting operates differently, as it involves the mixing of a powder material with a liquid binder that holds the particles together. A print head deposits the binder onto the powder bed layer by layer. Once printed, the object requires post-processing like curing or infiltration to enhance strength and durability.
Benefits include:
- Rapid Production: Fast printing speeds lead to quicker turnaround times compared to other methods.
- Cost Efficiency: This approach often requires less material, making it a cost-effective option for producing large quantities of parts.
However, the parts produced typically have lower density and mechanical properties than those made by processes like SLS or SLA, which may limit their application in some areas.
Digital Light Processing (DLP)
Digital Light Processing shares similarities with SLA but differs by using a digital light projector to cure the entire layer of resin at once. This leads to faster printing times since it does not rely on a laser scanning point by point.
The advantages of DLP include:
- Speed: Since an entire layer is cured simultaneously, it can produce parts much quicker than its SLA counterpart.
- Precision: Like SLA, it provides excellent detail and surface finish, making it suitable for intricate parts.
Yet, one should be wary of potential limitations regarding the range of available materials and their mechanical properties. The complexity of DLP printer setup and maintenance can also be a drawback for users unfamiliar with it.
Material Selection in Polymer Additive Manufacturing
The choice of materials in polymer additive manufacturing is not just an afterthought; it's a fundamental element that directly influences the performance, durability, and cost-effectiveness of any produced object. Selecting the right materials involves pondering over their thermal, mechanical, and chemical properties, as well as their compatibility with the chosen additive manufacturing process. A misstep here could lead to undesirable outcomes, such as structural failures or poor aesthetics. Therefore, comprehending the significance of material selection is crucial for anyone involved in this field.
Types of Polymers Used
In additive manufacturing, various polymers serve different purposes. Here are the most commonly used types:
- PLA (Polylactic Acid): This bioplastic is favored for its ease of use and environmental friendliness. Often used in FDM printers, it’s ideal for prototypes and artistic projects.
- ABS (Acrylonitrile Butadiene Styrene): Renowned for its strength and impact resistance, ABS is widely used in industrial applications. Its ability to withstand higher temperatures makes it suitable for functional parts.
- PETG (Glycol-modified Polyethylene Terephthalate): Known for its transparency and chemical resistance, PETG combines the best of both worlds—flexibility and strength, making it ideal for containers and mechanical parts.
- Nylon (Polyamide): This polymer is recognized for its toughness and flexibility. It’s particularly common in functional prototypes and products subject to significant wear.
Choosing among these polymers often leads to a balancing act between their physical properties and the intended application. A robust understanding is needed to align the right polymer with the specific needs of a project.
Thermoplastics vs. Thermosets
When it comes to selecting materials in additive manufacturing, one of the major distinctions lies between thermoplastics and thermosets:
- Thermoplastics are materials that become pliable upon heating. They can be recycled and reshaped multiple times without altering their chemical properties. Common thermoplastics include PLA and ABS. Their ability to easily undergo remelting allows for adjustments in design or re-utilization of waste material.
- Thermosets, in contrast, are materials that harden permanently after being shaped and cured. They can’t be remelted or reshaped after the curing process. Common examples include epoxy resins, often used in high-performance applications where structural integrity and heat resistance are paramount.
The choice between thermoplastics and thermosets revolves around the requirements of the final product, including factors such as temperature resistance and mechanical strength.
Composite Materials
Composite materials are increasingly gaining traction in the realm of additive manufacturing. A composite usually combines two or more distinct materials to create a new material with enhanced properties. Here are some notable benefits and elements to consider:
- Improved Properties: Composites often exhibit superior mechanical performance than the individual materials used. For instance, carbon fiber reinforced polymers bring together light weight and exceptional strength.
- Tailored Solutions: By adjusting the ratio of the components, manufacturers can enhance specific properties like flexibility, impact resistance, or thermal stability.
- Cost-Effectiveness: Sometimes, combining materials can result in savings, as using high-performance fibers only where necessary can lower the overall material costs.
However, challenges exist when working with composites, such as ensuring good adhesion between the layers and the complexities involved in their processing.
Process Parameters in Additive Manufacturing
Understanding process parameters in additive manufacturing is critical for optimizing quality, performance, and efficiency in producing polymer components. This intricate process involves several factors that can change the outcome of a printed part, ultimately influencing its mechanical properties, visual appeal, and functionality. Fine-tuning these parameters not only enhances the overall quality but also contributes to the economic feasibility of polymer additive manufacturing.
Temperature Control
Temperature control plays a pivotal role in the success of additive manufacturing processes. Each polymer has its own thermal properties that need to be understood and managed effectively. For instance, during Fused Deposition Modeling (FDM), the extrusion temperature must be high enough to melt the thermoplastic for printing but low enough to avoid degrading the material. The temperature of the build platform is equally significant; if it's too low, the printed layers may warp or not adhere properly, resulting in structural failures.
Moreover, in processes like Selective Laser Sintering (SLS), maintaining the right temperature is essential for ensuring that powder particles fuse correctly without forming unwanted defects.
Overall, the benefits of meticulous temperature control include:
- Improved adhesion between layers
- Enhanced mechanical properties of the final product
- Reduced risk of warping and cracking
Layer Thickness and Print Speed
Layer thickness is another key parameter that directly affects both the resolution of the final product and the time taken to print it. Thinner layers yield finer details and smoother finishes but at the expense of longer print times. Conversely, thicker layers can dramatically reduce production time but may lead to a rougher surface finish, impacting aesthetic and functional qualities. When assessing print speed, it’s worth noting that higher speeds can lead to less time but might compromise the quality and accuracy of the part.
Each application might require a different approach; for instance, rapid prototyping would benefit from faster speeds and thicker layers, while intricate designs would demand precision with thinner layers.
A few considerations include:
- Finding the ideal balance between speed and quality
- Evaluating the specific needs of the end-use application
- Understanding how these parameters interact with each other
Post-Processing Considerations
Post-processing is the final step in additive manufacturing but should never be an afterthought. It can make or break the final quality of a 3D printed polymer component. Common post-processing techniques include sanding, painting, and coating, which enhance mechanical properties, improve aesthetics, and can even protect against environmental factors. For instance, applying a sealant can prevent moisture absorption in certain polymers, which could otherwise lead to performance issues.
Moreover, the choice of post-processing methods may also depend on the initial printing parameters. If the initial layer adhesion was poor due to incorrect temperature settings, the final part might require more intensive treatment to regain its integrity.
To successfully navigate this phase, keep these points in mind:
- Determine the necessary post-processing before starting the print job.
- Consider the effects of chosen methods on material properties.
- Be aware of regulatory considerations if the parts are intended for medical or aerospace applications.
"The complexity of the additive manufacturing process does not end with the printing; post-processing is where the magic can either solidify or nullify the results."
By being aware of these process parameters and their implications, manufacturers can ensure that the end products meet—or even exceed—expectations. This deep dive into temperature control, layer thickness, print speed, and post-processing will aid in unlocking the full potential of polymer additive manufacturing.
Applications of Polymer Additive Manufacturing
Polymer additive manufacturing has emerged as a keystone in the evolving landscape of modern manufacturing. The versatility of additive techniques aligns perfectly with the diverse requirements of various industries. Whether it’s creating intricate prototypes or manufacturing functional products, the applications are only limited by our imagination. Understanding these applications holds paramount importance as they not only showcase the capabilities of the technology but also signify where the future development might lead.
Prototyping
One of the most notable uses of polymer additive manufacturing is in prototyping. This stage is often where ideas begin to take form, allowing designers and engineers to transition from concepts to tangible products. With the capacity to produce complex geometries at a fraction of traditional costs and time, 3D printing has revolutionized the way prototypes are conceived.
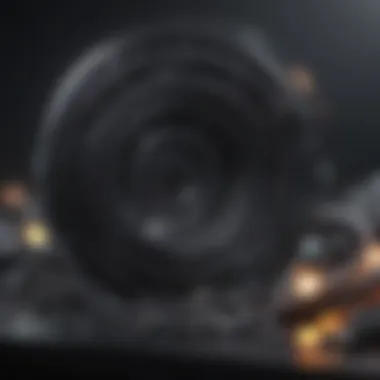
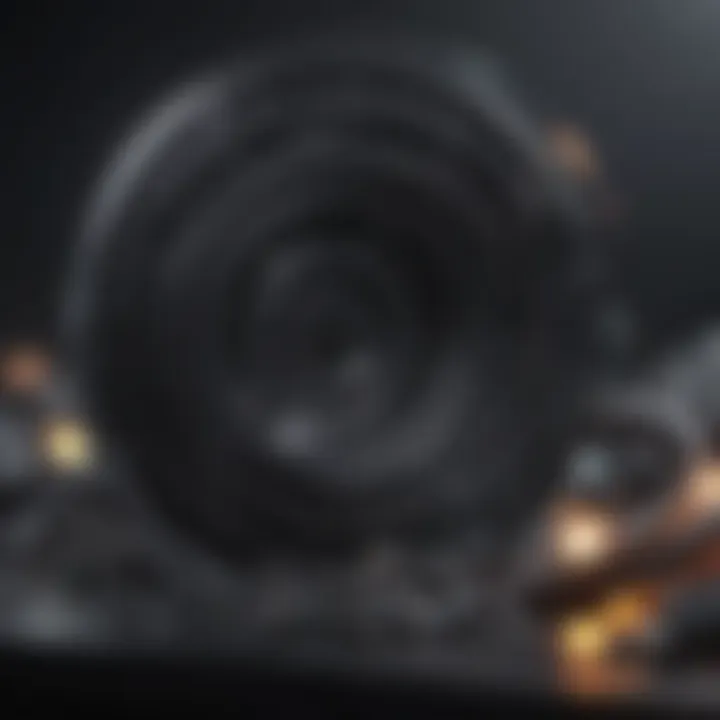
- Speed: Traditional methods might take weeks for prototype to be ready, 3D printing can cut that to days or even hours.
- Cost-Effectiveness: Financially, it is more feasible since less material waste occurs and adjustments can be made swiftly without incurring significant expenses.
- Iterative Design: Designers can test various designs easily, making modifications based on real-world feedback, ensuring that the final product is fine-tuned to meet market needs.
Medical Devices
The medical field is another area where the applications of polymer additive manufacturing are particularly noteworthy. Customized medical devices, anatomical models, and even bioprinting of tissues are all realms being explored.
- Customization: Custom prosthetics and orthotics can be produced specifically for individual patients, leading to greatly improved comfort and effectiveness.
- Anatomical Models: Practitioners can have access to accurate models of patient anatomy for pre-surgical planning, reducing the risks associated with operations.
- Regenerative Medicine: This is a growing field where bio-inks are utilized to create complex tissue structures, potentially restoring function in the future.
Aerospace and Automotive Industries
In industries like aerospace and automotive, where precision and material performance is paramount, polymer additive manufacturing finds significant applications. The ability to produce components with lightweight characteristics contributes greatly to fuel efficiency.
- Lightweight Structures: Aircraft parts manufactured through additive techniques can be made lighter without compromising strength, leading to better fuel economy.
- Rapid Tooling: The production of molds and tooling can be accelerated, allowing for faster turnaround without sacrificing the quality or durability of the parts.
- Complex Design Capabilities: Geometric limitations that are present with traditional methods surmount when additive manufacturing is employed. This opens up new avenues to experiment with innovative designs that enhance performance.
Consumer Products
Consumer goods also benefit from polymer additive manufacturing. This industry sees everything from fully-realized products to unique, custom items that cater to specific customer desires.
- Personalized Items: Companies can create tailor-made items, like custom phone cases or jewelry. This personalization drives consumer engagement and improves satisfaction.
- Small Batch Production: For small businesses or startups, additive manufacturing allows them to produce products in small quantities without needing massive investments in inventory.
- Trend-Driven Designs: Quickly changing market trends may make traditional manufacturing methods unsuitable, but additive production allows for agile response to consumer demands.
"In the ever-evolving world of manufacturing, the applications for polymer additive technology are not just innovative but essential for keeping pace with modern demands."
In summary, the applications of polymer additive manufacturing span a broad spectrum, each bringing unique benefits and solutions to industry challenges. From rapid prototyping to custom medical devices, the implications of this technology suggest a future where tailored solutions could dominate the manufacturing landscape, meeting the specific needs of various sectors efficiently and effectively.
Advantages of Polymer Additive Manufacturing
The realm of polymer additive manufacturing (AM) brings forth a myriad of advantages that mark a significant leap in production methods and design possibilities. As industries increasingly lean towards this innovative approach, it becomes crucial to understand the specific benefits associated with polymer-based additive manufacturing. These benefits not only shape the efficiency and effectiveness of production but also influence the future trajectory of manufacturing processes across various sectors.
Design Flexibility
One of the standout features of polymer additive manufacturing is the remarkable design flexibility it offers. Traditional manufacturing methods often confine designers to standardized shapes and processes, leading to constraints on creativity. However, with additive manufacturing, complex geometries that would be nearly impossible to create using traditional means become feasible.
For instance, consider the development of intricate lattice structures in lightweight components. AM allows for the design of such structures that optimize material usage while also enhancing performance. Designers are no longer confined by molds or tooling; they can prototype and produce parts directly from digital files, allowing for rapid iterations and modifications without incurring excessive costs. This flexibility is not just beneficial for prototype development but plays a vital role in customizing products to meet specific client demands. Moreover, these design capabilities open doors to innovative applications in fields as varied as fashion, architecture, and even consumer electronics.
Material Efficiency
Material efficiency stands out as another prominent advantage of polymer additive manufacturing. This technology is inherently more resource-efficient compared to conventional subtractive methods. In many traditional approaches, a significant portion of the initial material is cut away, leading to wastage. For example, machining a metal part may result in up to 70% of the original material being discarded.
In contrast, polymer additive manufacturing employs a layer-by-layer construction process that minimizes waste. Such processes only use the material required to build the item, often resulting in a reduction of waste by as much as 90%. This efficiency not only reduces costs associated with raw material procurement but also lessens environmental impact. In an era where sustainability is becoming increasingly critical, adopting polymer AM presents an opportunity for manufacturers to align with eco-friendly practices.
Shorter Lead Times
The speed of production is a third notable advantage of polymer additive manufacturing. Traditional manufacturing processes can be bogged down by lengthy setup times, tooling changes, and extensive human labor, all of which extend lead times. In a competitive marketplace, the ability to produce parts quickly can significantly enhance a company’s responsiveness to market demands and customer requirements.
Additive manufacturing enables a streamlined approach where designs can transition directly from the digital model to production without the need for physical molds or tooling changes. This results in production times that can be significantly cut down to just hours or days. For example, consider the effect this has on industries like automotive or medical device manufacturing, where being first to market can make a sizable difference to a company’s success.
"The effectiveness of polymer additive manufacturing often translates to drastic reductions in time and costs, making it a pivotal component in modern manufacturing strategies."
In short, the advantages of polymer additive manufacturing span across design flexibility, material efficiency, and reduced lead times. By capitalizing on these benefits, businesses are positioning themselves not only to thrive in a changing landscape but also to innovate and inspire in their respective industries.
Challenges in Polymer Additive Manufacturing
Navigating the landscape of polymer additive manufacturing isn't just a walk in the park. This field presents several hurdles that if not properly addressed, could pose significant roadblocks on the path to innovation. Understanding these challenges is crucial for students, researchers, educators, and professionals alike. Tackling material limitations, achieving high surface finish quality, and scaling production efficiently are essential considerations that define the success of any additive manufacturing project.
Material Limitations
In the realm of polymers, the type and quality of materials can either make or break a project. While there is a wide variety of polymers available, each with its own set of properties, not all of them are suited for every application. For instance, some thermoplastics, known for their ease of printing, might lack the strength needed for industrial applications. Conversely, high-performance polymers, while strong, often come with increased costs and complexities in the printing process.
Moreover, many polymers exhibit anisotropic behavior, meaning their properties can differ based on the direction in which they're printed. This variability can impact the final product's reliability and performance. For instance, a part might display robustness in one orientation but could crack easily in another.
To address these issues, ongoing research is focused on the development of new polymer blends and composites that balance performance and manufacturability. By exploring options beyond traditional materials, manufacturers can craft tailored solutions.
Surface Finish Quality
Surface finish is another sticky point in polymer additive manufacturing. The aesthetic and functional quality of a final product often hinges on its surface. Poor surface finish can lead to dissatisfaction and even product failure. A rough finish could affect how parts stack together or lead to issues in sealing applications, thus impacting their overall reliability.
The layering process distinct to additive manufacturing can introduce visible lines or other artifacts that detract from the visual appeal and performance. Techniques such as sanding, smoothing, or adding surface coatings can improve quality, but these post-processing steps can add time and cost to production.
Experimenting with nozzle sizes, print speeds, and even environmental conditions during printing play a role in achieving a better surface finish.
Scaling Up Production
As additive manufacturing grows, businesses often strive to expand production. However, scaling up from prototyping to mass production involves significant challenges. One pressing concern is the inconsistency often seen in larger print runs. Factors like machine calibration, environmental variances, and material lot changes can all contribute to discrepancies in product quality.
Furthermore, the speed at which printing occurs is often a limiting factor; many polymer printers are slower than traditional manufacturing methods. Adapting printing technologies like multi-jet fusion or utilizing multiple printing heads can mitigate some of these concerns, but they typically require careful planning and investment.
There is also the issue of cost efficiency. While additive manufacturing is lauded for customization, those benefits might not always align with high-volume production needs. Manufacturers must weigh the pros and cons of potential increased labor and material costs against traditional manufacturing approaches.
"Understanding these challenges enables us to unlock the full potential of polymer additive manufacturing, transforming hurdles into gateways for innovation."
Future Trends in Polymer Additive Manufacturing
The landscape of polymer additive manufacturing is constantly changing, and keeping an eye on future trends is vital for various stakeholders—whether they’re engineers in a lab, entrepreneurs starting new businesses, or hobbyists keen on the latest tech. Understanding what the future holds can provide insights into new opportunities, innovation pathways, and potential challenges. Here, we will explore key components that shape the future of this intriguing field, focusing on advancements in material science, the integration of artificial intelligence and machine learning, and considerations for sustainability.
Advancements in Material Science
Material science plays a crucial role in pushing the limits of what can be achieved in additive manufacturing. New materials are continuously developed to meet specific needs across industries. For example, bio-based polymers are gaining traction for applications in the medical field, thanks to their biocompatibility and reduced environmental impact.
Moreover, improvements in polymer properties through techniques like molecular engineering are paving the way for materials that combine light weight with enhanced strength, making them suitable for sectors like aerospace and automotive. Thus, the importance of keeping abreast with these developments cannot be overstated.
"The advancement of material science is akin to adding more colors to an artist's palette; the more options available, the richer the creation can become."
Integration with AI and Machine Learning
Artificial intelligence and machine learning are no longer buzzwords; they’re becoming integral to polymer additive manufacturing. These technologies streamline the design process by analyzing vast datasets to optimize printing parameters, enhancing energy efficiency and reducing waste. AI can also aid in predictive maintenance, identifying potential machine issues before they arise, saving costly downtime.
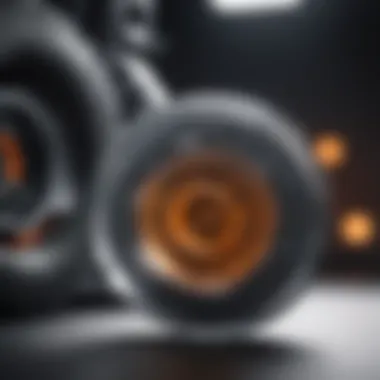
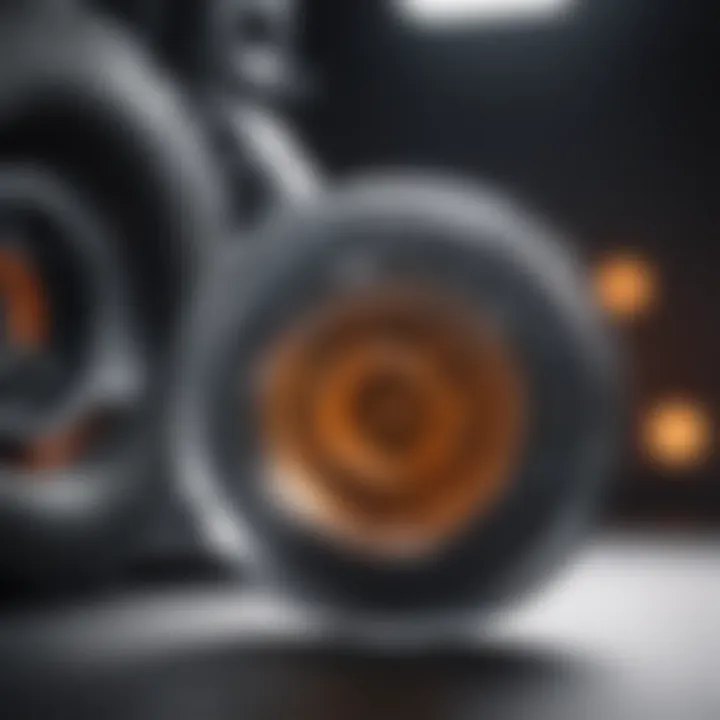
In terms of design, generative design algorithms can produce innovative geometries that are often beyond human imagination. The integration of AI in monitoring printing processes allows for real-time adjustments, leading to higher quality and consistency in printed parts. Coupled with machine learning, such systems can learn from each build, continually improving the process.
Sustainability Considerations
As the world becomes increasingly aware of environmental issues, sustainable practices in additive manufacturing are becoming essential. The need for eco-friendly materials and processes is more than just a trend; it’s a necessity for future viability. This includes developing biodegradable polymers and recycled materials for printing, diminishing the carbon footprint.
Sustainable approaches also encompass energy efficiency in production. Innovations that reduce energy consumption during the printing process contribute to more sustainable practices.
Companies and researchers are also looking into life cycle assessments of materials to gauge their environmental impact, which can influence manufacturing choices heading into the future. Engaging with sustainability isn’t just good for the planet; it’s also good for business. Consumers are increasingly favoring brands that prioritize sustainability, which can be a significant factor in market competitiveness.
Regulatory and Standardization Issues
In the realm of additive manufacturing, particularly within the polymer sector, regulatory and standardization issues play a crucial role. They ensure not only the safety and quality of the products being manufactured but also foster consumer trust and industry credibility. As this technology evolves, so does the need for a cohesive framework that can adequately address the unique challenges of 3D printing processes. With various applications ranging from medical devices to aerospace components, the stakes are high. Therefore, establishing stringent guidelines becomes a necessity to avoid pitfalls while also promoting innovation.
Industry Standards in Additive Manufacturing
The creation of industry standards in additive manufacturing forms the backbone of quality assurance. These standards facilitate consistency across the production spectrum. Organizations like ASTM International and ISO (International Organization for Standardization) are actively involved in drafting specifications that govern how materials should be used, how processes should be conducted, and how finished products should be tested.
One vital aspect of these standards involves classification based on the types of polymers used. This classification aids in understanding the material properties that dictate their performance in various applications.
- Property specifications: Standards specify tensile strength, elongation at break, and thermal properties, ensuring compatibility for intended applications.
- Process recommendations: Guidelines help manufacturers grasp the best practices for each technology type, whether it's FDM, SLA, or SLS, thus improving outcomes.
- Testing protocols: They outline the methods of verifying product integrity and safety, which is particularly significant in medical or automotive applications where failure can have dire consequences.
As industry standards become more entrenched, they help level the playing field for manufacturers, especially smaller firms that might otherwise struggle to compete with larger corporations possessing more resources.
Compliance Challenges
Compliance challenges are pervasive when discussing regulatory frameworks in additive manufacturing. Manufacturers must navigate a minefield of rules that vary by region and product type. For instance, the medical sector adheres to the FDA regulations in the United States, which adds layers of complexity to product development.
Some of the main hurdles that manufacturers encounter include:
- Diverse regulations: Different countries have unique regulations that can complicate international trade and manufacturing processes.
- Rapid technology evolution: As the technology progresses at a breakneck pace, existing regulations often fail to keep up, leading to grey areas where companies may unintentionally falter.
- Documenting processes: Maintaining comprehensive documentation to prove compliance can be burdensome, especially for smaller companies without dedicated compliance teams.
This need for ongoing dialogue between industry stakeholders and regulatory bodies is crucial. Having a seat at the table can potentially influence the direction regulations take, ultimately facilitating a smoother path for innovation.
In summary, regulatory and standardization issues are not mere formalities; they are essential for ensuring that additive manufacturing remains a viable, safe, and trusted field.
"Proper regulation in additive manufacturing is not just about compliance; it’s about cultivating an environment of trust and innovation that can pave the way for future breakthroughs."
Case Studies in Polymer Additive Manufacturing
Exploring case studies in polymer additive manufacturing serves as a lens through which to scrutinize practical applications of this dynamic technology. These real-world examples not only illustrate the versatility and effectiveness of additive manufacturing but also provide valuable insights into the processes and decisions that shape successful outcomes. By examining specific implementations, practitioners can glean lessons that are essential for future endeavors in the field.
Successful Implementations
One prime example of successful implementation can be found in the automotive industry, where companies leverage additive manufacturing to create complex components faster and at reduced costs. For instance, BMW has utilized polymer-based 3D printing to manufacture customized interior parts for their vehicles. This approach enables them to achieve a high level of design flexibility. By using Fused Deposition Modeling (FDM), they can quickly iterate designs, significantly shortening the product development cycle.
Another noteworthy case is Nike’s use of additive technology for creating bespoke shoe insoles. Using selective laser sintering, Nike produces lightweight structures tailored for individual athletes, enhancing performance and comfort. Through this innovation, they have not only improved customer satisfaction but also streamlined their inventory management.
These instances show how case studies reveal practical applications that can guide future initiatives in polymer additive manufacturing.
Lessons Learned
From these case studies, several critical lessons emerge, guiding future practitioners in polymer additive manufacturing.
- Flexibility and Adaptability: Many companies that successfully integrated additive manufacturing emphasize the importance of being flexible in design. Iterative processes enable teams to adapt products based on real-time feedback, which enhances the final output.
- Material Selection: Choosing the appropriate polymer material is paramount. Companies like Ford found that experimenting with composite materials can yield stronger and lighter components, underscoring the significance of understanding material properties and their implications on performance.
- Investment in Technology: Commitment to upgrading technology has proven beneficial. Businesses investing in the latest printing equipment typically see better accuracy and efficiency in production, as seen in General Electric’s use of advanced polymer printers for their aerospace components.
"It’s not just about having the technology, but also knowing how to harness its potential effectively."
The End and Implications
The exploration of additive manufacturing in the context of polymers is not merely an academic exercise; it speaks to the core of modern manufacturing principles and practices. Understanding the intricacies of this technology can significantly influence how industries approach design, production, and sustainability.
One of the pivotal elements of this discussion is the capacity for customized production. In traditional manufacturing, producing a specific part often required extensive tooling and setup, leading to high costs and substantial waste. In contrast, additive manufacturing allows for precision and flexibility. For instance, designers can iterate product designs almost at will, paving the way for innovations that resonate with consumer needs. This adaptability is invaluable, especially in tech-driven markets where change is a constant.
Moreover, the sustainability considerations surrounding additive manufacturing warrant serious attention. By leveraging this technology, companies can reduce excess material usage and minimize the carbon footprint associated with production. For example, structures that were once overly bulky can now be tailored to be lightweight yet robust. This might seem trivial, but in fields such as aerospace, every gram saved can enhance efficiency.
Finally, as regulatory frameworks become more comprehensive, the importance of standardization cannot be understated. Industries must navigate compliance to ensure that additive manufacturing meets safety and quality benchmarks, while also fostering innovation.
To sum it up, the implications of this topic stretch far and wide, from fostering design innovation to addressing environmental concerns, presenting a framework for sustainable production.
Summary of Key Points
- Customization: Additive manufacturing enables bespoke designs tailored to specific needs, thereby driving innovation.
- Efficiency: Reducing waste and improving material usage are central tenets of this technology, making it an environmentally-friendly choice.
- Regulatory Landscape: As the industry matures, compliance and standardization become vital, ensuring safety and quality in production processes.
Future Outlook
Looking ahead, the future of polymer additive manufacturing is poised for remarkable growth. Advancements in material science promise to introduce new polymers with enhanced properties, making them suitable for more demanding applications. For example, researchers are exploring bio-based materials that not only meet performance standards but also contribute to sustainability goals.
The integration of artificial intelligence and machine learning into the manufacturing process stands to revolutionize production efficiency. These technologies can optimize print parameters in real-time, further reducing waste while enhancing the quality of the end products.
Consideration of sustainability will likely drive research and development efforts, aligning with global shifts towards eco-friendly practices. Companies that seize the opportunity to innovate responsibly will not only stand out in a crowded marketplace but can also lead significant change towards environmental stewardship.
Academic Journals
Academic journals are among the first stops for anyone interested in the groundbreaking realm of polymer additive manufacturing. These journals publish research that undergoes rigorous peer review, ensuring that the information is credible and scientifically valid. Journals such as "Additive Manufacturing" and "Journal of Polymer Science" frequently offer articles focusing on new materials, innovative printing techniques, and detailed case studies of successful implementations. By diving into this literature, one can gain insights into not just successful trials but also failures that can offer lessons to future researchers.
Some key aspects of academic journals include:
- Peer Review Process: Ensures quality and reliability in the published findings.
- Cutting-Edge Research: Often features the latest advancements in polymer materials and printing technologies.
- Variety of Case Studies: Showcases real-world applications and outcomes of additive manufacturing.
This exploration into academic literature allows one to grasp where the technology currently stands and what gaps may still exist.
Industry Reports
While academic publications are invaluable, they often focus on theory and scientific understanding. Industry reports, on the other hand, can present perceptions and trends based on real-world application. Companies like PwC, McKinsey, and Gartner publish comprehensive reports that cover market analysis, forecasts, and competitive landscapes within the additive manufacturing sector. These reports not only provide statistical data but also include insights from industry veterans, making them essential reading for professionals wanting to stay ahead of the curve.
Industry reports can enhance one's understanding by providing:
- Market Trends: Insights into which areas of polymer additive manufacturing are experiencing growth.
- Economic Impact Analysis: Understanding the financial implications can help in strategic planning.
- Consumer Perspectives: Reports often include feedback from end-users, illuminating how the market perceives various technologies.
By tapping into both academic journals and industry reports, stakeholders are better equipped to navigate the increasingly complex world of additive manufacturing, ensuring that they're backed by both theoretical and practical knowledge.